WFL Millturn Technologies GmbH & Co.KG - The technological leader.
WFL is the only manufacturer worldwide that focuses exclusively on the production of multifunctional turning-boring-milling centers ... more
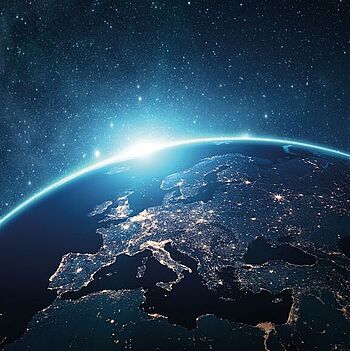
Global contact partner:
Technologies
Combining all machining and measuring operations in one single MILLTURN by WFL will raise the efficiency of your production enormously. This is an investment that pays off in virtually no time.
machining result
News
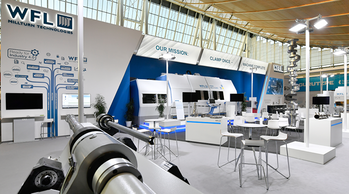
Worldwide
WFL locations
More than
Excited employees
More than
Registered patents
WFL software, service & support
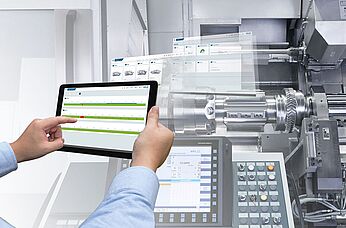
CrashGuard, the patented collision prevention system is a real-time software extension of the CNC control system.
MORE
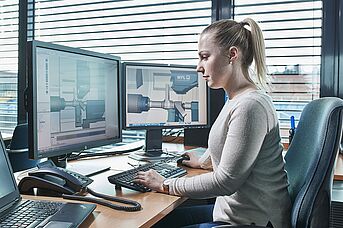
CrashGuard Studio, the realistic 3D simulation software is the ideal tool for testing and optimising CNC programs after they have been created or modified.
mORE
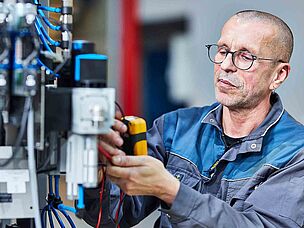
We are close to our customers. Major manufacturers put their trust in WFL’s vast experience. A head start that reflects in WFLs services. Please find here our offers.
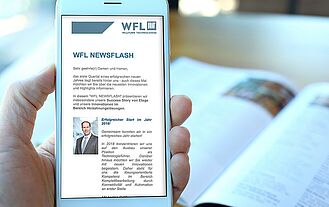
WFL NEWSFLASH
Register now!
The WFL NEWSFLASH informs you about our latest innovations in complete machining, technological highlights and modern services as well as upcoming events and exhibitions.
Register now and do not miss out on any WFL news!
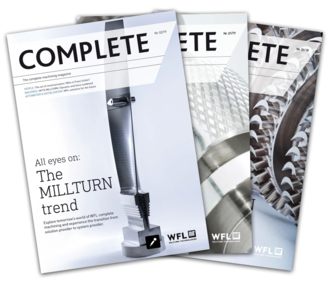
COMPLETE
The complete machining magazine
Explore tomorrow's world of complete machining. Be inspired by innovative technologies, success stories and product highlights.
Dive into the world of WFLs' complete machining.