Incorporating complete machining
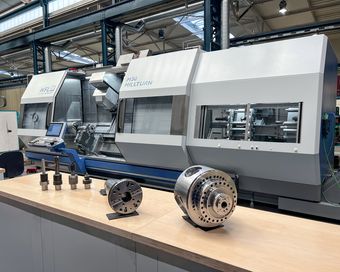
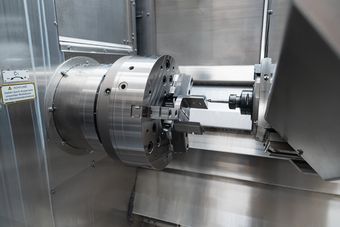
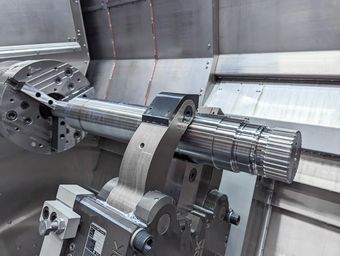
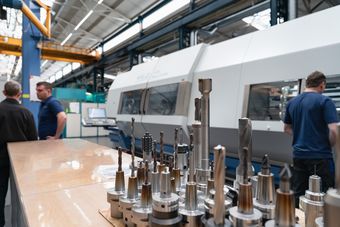

For more than 100 years, WALDRICH COBURG has been manufacturing large, powerful gantry machining centres and gantry grinding machines that are used in a wide range of industries. And when we say large, we mean large.
The passage widths of these machines extend to 14 m and the passage heights to max. 12 m. Workpieces weighing up to 400 tonnes are machined and the machining centres boast a performance of up to 300 kW. So they are real Goliaths amongst machine tools.
WALDRICH COBURG machines are used in the most diverse branches of industry, including the automotive industry, aerospace, the energy industry and general production. Services ranging from general service to applications engineering, production support and contract manufacturing round off WALDRICH COBURG's portfolio. Examples of more specific applications include large marine diesel engines or drive screws for marine engines. Chassis components are produced for the aerospace industry as well as various press moulds for tool and mould construction. Some rail construction and freight train machines have also already been replaced in the vehicle construction industry.
Mechanical engineering in a class of its own
WALDRICH COBURG works principally at project business level. An average of around 20 to 30 projects are implemented each year, most of which are delivered to Europe. The Benelux countries as well as Italy and France are extremely strong markets for the company. In terms of industry technology, the aerospace sector is booming and the markets in the USA and China are on the rise.
The projects are extremely labour- and time-intensive. A complete project can last up to 24 months from the initial customer contact or project planning through to handover and acceptance of the machine. A few months ago, the M50 MILLTURN with a centre distance of 3000 mm entered production at WALDRICH COBURG. It is now used to produce drive components for additional units. Gear wheels, milling spindles and swivel units are further components that are machined on the new turning-boring-milling centre. These are the three product groups that are currently produced on the machine in different variants. The various power chuck and shaft parts measure up to 670 mm in diameter and max. 3000 mm in length and batch sizes range from two to four pieces. The MILLTURN is already being put to good use with this range of parts. "During the procurement process, we placed great emphasis on finding a powerful machine combined with innovative solutions to ensure we could implement a smooth machining process. That was the most important factor for us when it came to making our decision," says Helmut Wall, Head of Production at WALDRICH COBURG.
"Before being able to undertake complete machining with the WFL, we worked with individual machines where we executed one work process or one work step, then moved on to the next machine. This made the machining process extremely tedious. Lead times were considerably longer than they are now," explains Helmut Wall.
Efficient complete machining
WALDRICH COBURG currently combines multi-step production with complete machining, as the throughput for some components needs to be retained due to the good machine utilisation. Lead times have been reduced by one third with the new M50 MILLTURN, which has had an extremely positive impact – production is faster, more efficient and, above all, cheaper. A fantastic achievement! The machine is generally capable of achieving higher performance. WALDRICH COBURG is currently at the start of its learning curve, but this is set to change in the near future.
Before deciding on the MILLTURN from WFL, a detailed catalogue of requirements was drawn up. Much research was carried out into the technological capabilities of such a machine. This was one of the most important aspects for WALDRICH COBURG. The machine had to combine turning, milling, drilling and gear cutting in a single machine. The company was impressed by the technology and innovative strength of the machine. Based on the component dimensions involved in machining, it immediately became clear that an M50 MILLTURN with a centre distance of 3000 mm was required. "For us, complete machining is the key to meeting the demands of modern metalworking, the large number of variants and short delivery times as well as the special quality requirements of our customers. This formed the basis for our decision to purchase. It was also important to us that the machine runs reliably. This is why we decided to use the iControl process monitoring function. A fantastic additional feature that further supports the process and allows us to become even more flexible when it comes to simulations," explains Helmut Wall.
Numerous components are currently produced on the MILLTURN. After machining, these are re-treated and some are sent for heat treatment, gas nitriding, hardening and finally precision grinding. The workpieces are programmed exclusively in-house at WALDRICH COBURG. They are programmed by the Process Engineering team both with Siemens NX and sometimes on the machines themselves. In future, everything is set to be programmed by the Process Engineering team so as to keep the machine free for production.
Complete machining and, as such, WFL, is still uncharted territory for WALDRICH COBURG, but the company is quickly getting to grips with this type of machining and the various turning, drilling, milling and gear cutting technologies. Several machine operators and programmers are currently working in shifts on the WFL.
A sustainable future
In a rapidly developing market environment, automation, digitalisation and sustainability are important considerations for the future of WALDRICH COBURG. A strategy team is working on various topics that will be implemented in future.
Sustainability has been an important theme for some time. Around six years ago, the company invested in a combined heat and power plant by way of ending its dependence on oil. Photovoltaic panels were also installed on all flat roofs of the assembly and production halls. This means that the company sustainably generates its own heat and electricity.
The carbon footprint of the machines has also been put under the microscope. WALDRICH COBURG is currently developing a range of solutions. It is investigating the use of exhaust air and the prevention
of heat build-up at the machines,
amongst other approaches.