Rentrer en orbite le plus efficacement possible
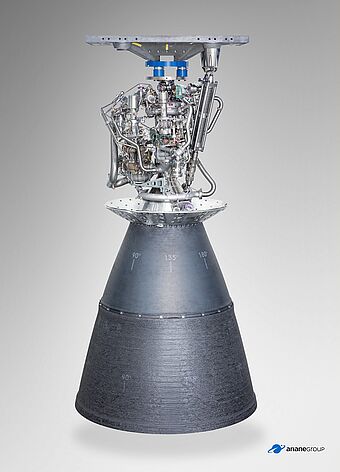
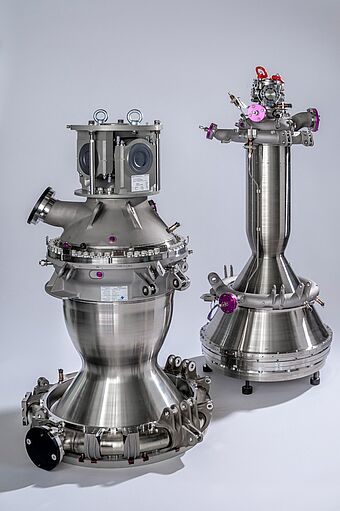
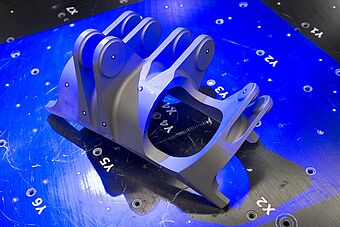
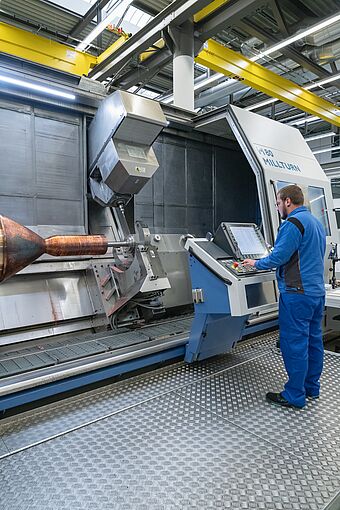
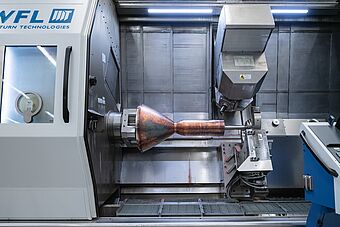
Leader mondial de l'aérospatiale, ArianeGroup travaille pour des clients institutionnels et commerciaux et assure l'indépendance stratégique de l'Europe.
En tant que maître d'œuvre des lanceurs européens Ariane 5 et Ariane 6, ArianeGroup est responsable de l'ensemble du cycle de vie d'un lanceur, de la conception à l'exploitation, en passant par la production et la commercialisation, via sa filiale Arianespace. ArianeGroup emploie environ 7 000 personnes hautement qualifiées en France et en Allemagne. Elle est détenue à parts égales par Airbus et Safran dans le cadre d'une joint-venture. La société est également le maître d'œuvre des missiles balistiques de la marine française. ArianeGroup et ses filiales sont des spécialistes internationalement reconnus des équipements et de la propulsion aérospatiale, des services et de la surveillance de l'espace. Leur expertise est également utilisée dans d'autres secteurs industriels et dans les infrastructures critiques.
-
7 000 employés en Allemagne et en France
-
11 filiales et participations majoritaires
-
Joint-venture à 50/50 entre Airbus et Safran
-
Un chiffre d'affaires de 3,1 milliards d'euros en 2021
L'un des sites clés d'ArianeGroup est Ottobrunn, près de Munich. C'est là que se trouve le centre de propulsion liquide d'ArianeGroup, où sont développés et produits les composants des moteurs des lanceurs européens Ariane. L'accent est actuellement mis sur les chambres de poussée du moteur de l'étage principal d'Ariane 6, le Vulcain 2.1, ainsi que sur le nouveau moteur de l'étage supérieur ré-allumable, Vinci.
Un aperçu du monde des voyages dans l'espace
Stefan Winter, responsable de la production à Ottobrunn, nous donne quelques informations intéressantes lors d'une visite des installations de production : "Nous avons près de 300 employés ici à Ottobrunn, dont environ 100 travaillent à la production. Tous les processus de fabrication de nos composants sont réalisés en interne, ce qui nous permet d'avoir des délais très courts. La majorité de nos processus sont réalisés dans notre centre de production, de l'usinage au soudage (EB et TIG) à l'intégration et aux tests de qualité. La galvanisation et le nettoyage des composants ont lieu dans des bâtiments voisins. Ces courtes distances sont un énorme avantage pour nous."
Pour quitter la Terre et son attraction gravitationnelle, une fusée a besoin de beaucoup d'énergie. Les lanceurs Ariane y parviennent grâce à des propulseurs à poudre qui délivrent une poussée d'environ 13 tonnes de poussée et font décoller les fusées de 800 tonnes dans les deux minutes qui suivent le lancement. L'étage principal, équipé du moteur Vulcain-2, qui démarre en premier après le compte à rebours, fournit une poussée supplémentaire jusqu'à ce que la fusée atteigne une altitude d'environ 160 kilomètres, environ neuf minutes après le lancement. Dans l'espace, l'étage supérieur prend le relais. Il est propulsé par le moteur HM7B pour Ariane 5 et Vinci pour Ariane 6. Selon la mission, ce moteur est opérationnel pendant environ 15 minutes pour placer l'étage supérieur avec les satellites dans l'espace sur la bonne orbite.
La chambre de poussée, le "cœur" du moteur du moteur Vinci d'Ariane 6 a été développée et fabriquée à Ottobrunn.
Vinci travaille avec de l'hydrogène et de l'oxygène cryogéniques comme cycle d'expansion : "D'abord, l'hydrogène circule autour de la chambre de combustion, les gaz produits sont utilisés pour actionner les pompes à carburant, puis sont injectés dans la chambre de combustion, explique Stefan Winter, chef de la production.
"Il n'existe qu'un seul moteur à cycle expandeur présentant ce niveau de performance dans le monde entier. Alors que les moteurs cryogéniques conventionnels ont presque toujours besoin d'un générateur de gaz pour entraîner les turbopompes, ce processus fonctionne différemment dans la chambre de combustion de Vinci.
Avec le moteur avec cycle d’expansion, bien que l'hydrogène puisse passer par les canaux de refroidissement pour refroidir la chambre, sa conception intelligente signifie qu'il reste longtemps dans la chambre, jusqu'à ce qu'il soit aussi chaud que possible. Nous utilisons ensuite le gaz en expansion pour actionner les turbopompes. C'est le grand avantage du moteur Vinci".
Une M80 Millturn est utilisée pour produire le moteur Vinci
La plupart des pièces du moteur d'Ottobrunn sont fabriquées sur une machine WFL M80. Cela inclut également la base du corps de la chambre de combustion du moteur. La base du corps est d'abord préparée pour le tournage du contour intérieur, puis pour le tournage et le fraisage du contour extérieur. Ces deux processus étaient auparavant réalisés sur deux machines.
Grâce à la M80 Millturn, les deux processus : le tournage et le fraisage sont combinés et le fait de serrer une seule fois la pièce assure une opération stable. C'est un énorme avantage, surtout pour les pièces longues et fines comme la chambre de combustion de Vinci. Le système de serrage à point zéro offre également une flexibilité maximale dans la production. "C'est excellent", souligne M. Winter.
Un alliage spécial est utilisé pour le corps de base du moteur Vinci. L'alliage breveté cuivre-argent-zirconium se caractérise par une résistance élevée, une excellente valeur de transfert thermique et une excellente usinabilité, ce qui est particulièrement pertinent pour la chambre Vinci. En raison de la conception allongée et mince de cette pièce, les propriétés de ce matériau sont très importantes. Le matériau est d'abord coulé en blocs, puis forgé dans la forme souhaitée. La qualité est assurée par des ultrasons, puis la production est lancée.
Les principales étapes de production d'une chambre de combustion Vinci après la livraison de l'ébauche sont le tournage, le fraisage, la galvanisation, le soudage et enfin la finition.
Plus de 80% de la charge de travail est réalisée avec la M80.
En outre, des essais de coupe pour l'avenir sont également réalisés sur la M80. La conception robuste et l'excellente cinématique offrent plus de possibilités que prévu. Les premiers essais sur le Tour-Fraiseur Multifonctions M80 ont déjà été réalisés avec des outils de coupe en céramique. À moyen terme, il est également prévu de réaliser ce procédé sur la machine WFL pour l'Inconel et le nickel.
"Je suis très confiant que nous pourrons le faire sur la machine WFL", déclare M. Winter.
Esprit d'innovation pour la technologie et le personnel
La Millturn est actuellement utilisée pour fabriquer d'autres composants que les pièces Vinci. L'équipe de production utilise également la machine pour produire des pièces satellites, ainsi qu'en R&D et pour la construction de gabarits.
"Ce mélange permet d'utiliser au mieux la capacité de la machine", explique Stefan Winter. "Je suis également un fan des travaux de développement, car il s’agit de répondre aux besoins de demain afin d’être capable de relever de nouveaux défis. Par exemple, nous travaillons actuellement sur les composants du futur moteur - Prometheus."
Les différentes versions du moteur Prometheus seront alimentées par de l'hydrogène et de l'oxygène liquide ainsi que du méthane. Cette génération sera le premier moteur européen à combustion contrôlée, ce qui permettra de s'adapter aux conditions de vol du lanceur pendant les différentes phases de la mission. Un système numérique assurera le contrôle sur une plage allant de 30 à 100 % de la poussée maximale. Prometheus sera également équipé d'une intelligence artificielle et d'un système de surveillance de l'état de santé qui permettra d'effectuer des diagnostics sur le fonctionnement du moteur.
La famille des propulseurs Prometheus bénéficie aussi largement des dernières technologies d'impression 3D. Les pièces produites de cette manière représentent 70 % du poids total du moteur.
"Le Tour-Fraiseur Multifonctions WFL est très bien adapté à tous ces futurs projets, passionnants", déclare Stefan Winter.
Il faut une équipe motivée d'ingénieurs et d'ouvriers qualifiés pour donner vie à tout cela. En particulier, les machines très complexes telles que la WFL nécessitent des employés excellents et consciencieux. Lorsque le processus de finition d'une pièce d'une valeur supérieure à un demi-million d'euros se déroule sur la machine, c'est un moment de tension pour les employés. "Il est difficile de trouver de bons employés, c'est pourquoi nous sommes toujours à la recherche de bons travailleurs qualifiés", déclare M. Winter.
"En tant que responsable de la production, il est particulièrement important pour moi de rendre le lieu de travail intéressant pour les employés. Nous avons principalement des ingénieurs et des techniciens supérieurs qui travaillent dans la production à Ottobrunn. Les bons travailleurs qualifiés ont soif de connaissances et ont donc besoin d'être stimulés et soutenus. C'est pourquoi nous essayons de rendre les postes de travail aussi intéressants que possible. Notre objectif à moyen terme est de disposer d'un pool de personnel spécialisé affecté à une machine et que celle-ci soit également mise en œuvre de manière indépendante, de la programmation à la production du composant. Nous déploierons ensuite cette rotation des tâches sur d'autres machines. Au cours des 5 prochaines années, je veux faire évoluer la production dans ce sens", déclare M. Winter avec conviction.
Il ajoute également : "Nous travaillons avec des matériaux extrêmement coûteux, conformément aux normes industrielles les plus strictes et aux niveaux de qualité les plus élevés. Lorsqu'une fusée est lancée, il n'y a pas de seconde chance, nous n'avons donc pas le droit à l'erreur. Un personnel soucieux de la qualité est essentiel ici et nous l'avons."
Pourquoi un Tour-Fraiseur Multifonctions WFL ?
"En ce qui concerne les temps d'usinage, notre investissement dans le M80 Millturn / 3000mm a apporté une énorme valeur ajoutée", explique Stefan Winter. Cette machine a remplacé un tour 3 axes et une fraiseuse 3 axes. Un système de serrage à point zéro a été mis en place sur la M80, de sorte que le réglage est toujours très rapide.
Cela a permis de réduire les délais et les temps d'attente d'au moins 30 %.
"L'un des principaux avantages de la machine WFL est son grand magasin d'outils. En raison de l'usinage de l'Inconel, nous avons toujours entre quatre et six outils en service. C’est pourquoi le concept de magasin modulaire est intéressant.
De plus, auparavant nous devions gérer trois processus avec trois programmes CN minimum. Aujourd'hui, il nous suffit de lancer un seul programme CN pour le même travail. La gestion de la configuration est également beaucoup plus facile, car il y a moins de données à gérer. C'est un grand pas en avant", explique M. Winter avec enthousiasme.
Lorsqu'on lui demande pourquoi il a opté pour un Tour-Fraiseur Multifonctions, modèle M80, M. Winter répond : "En fin de compte, la cinématique et les références de la machine nous ont convaincus. Un approvisionnement rapide en pièces de rechange, des composants provenant de fabricants renommés et aussi la proximité du fabricant étaient également importants pour nous."
La machine est équipée d'un magasin prismatique Pick-up qui intègre entre autres une barre d'alésage système WFL. "Nous avons travaillé avec WFL et Sandvik pour nous procurer une barre d'alésage spéciale de 1,4 m de long afin qu'à l'avenir, nous puissions également usiner le contour intérieur de la Vinci sur la WFL."
"La machine devait également répondre à certaines exigences de fiabilité et de précision avec une tolérance d'environ 1/100 dans la plage de travail requise. C'est notre exigence. Les influences de la température jouent un rôle énorme ici, c'est pourquoi notre atelier de production est également climatisé. Nous vérifions et contrôlons régulièrement la température des machines. Avec ces nombreux avantages nous pouvons vraiment dire que WFL est à la pointe de la technologie", déclare M. Winter.
Les surfaces d'étanchéité sont fabriquées chez ArianeGroup en utilisant sur le Tour-Fraiseur Multifonctions M80 la fonction Utronix (un axe U virtuel). "À environ 135 degrés, nous devons usiner une surface d'étanchéité de 28 mm autour d'un trou de 20 mm avec une barre d'alésage. La fonction Utronix est donc souvent utilisée dans ce cas", explique M. Winter à propos du processus d'usinage.
M. Winter souligne également l'avantage que représente la nouvelle machine pour la fabrication d'un démonstrateur de buse : "On nous a demandé de construire un démonstrateur de buse. Le défi consistait à fabriquer un contour intérieur conique complexe avec des canaux de refroidissement. Grâce à la stabilité de la machine, nous avons pu réaliser le processus de brochage sur une longueur de près de 500 mm. La combinaison de la stabilité, de la flexibilité et de la zone de travail requise dans la machine permet d'aborder et de réaliser ce type d'usinage spécial."