Mesure
Précision de fabrication maximale pour vos pièces à usiner complexes
Pour pouvoir fabriquer des pièces à usiner complexes associées à des exigences de qualité élevées avec une grande sécurité de procédé, il faut gérer les procédés en « boucle fermée ».
Le procédé de mesure développé par WFL permet d’obtenir une précision de fabrication maximale associée à des tolérances de mesure et de position extrêmement faibles sur des pièces à usiner complexes. Pour ce faire, il existe toutes sortes d’instruments de mesure :
- Mesure manuelle
- Mesure intégrée
- Mesure par balayage
- Mesure de pièce intégrée sur la tête de tournage-perçage-fraisage
- Mesure à ultrasons
- Dispositif de calibrage avec compensation de température
Nos partenaires pour des mesures précises sont les entreprises Blum, Hexagon et Renishaw.
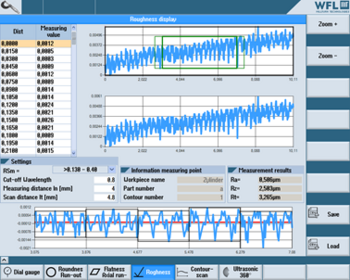
Mesure manuelle
De manière générale, la mesure dans un procédé de fabrication peut être divisée en deux domaines : la mesure manuelle et la mesure automatique.
Dans le cas de la mesure manuelle, l’opérateur réalise la mesure et la gestion des données de mesure. Dans le cas de la mesure automatique, en revanche, c’est la machine qui prend en charge la mesure et la gestion des données obtenues.
La mesure manuelle est toujours solidement ancrée dans la production, car elle reste moins coûteuse que les instruments de mesure modernes, en particulier sur une période de temps limitée. Cependant, dans le cas de mesures manuelles, il faut tenir compte de la marge d’erreur potentielle et de l’allongement du temps de production qui en résulte.
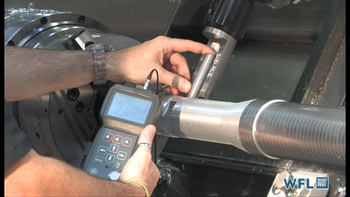
Mesure intégrée
Le palpeur de mesure de commutation utilisé dans la machine-outil permet, en association avec les paquets de cycles de mesure décrits ci-après, l’intégration de différentes stratégies intelligentes de mesure et de correction dans le procédé de fabrication. Ce faisant, des règles linéaires précises, adaptées aux coefficients de dilatation thermique de l’acier et un procédé de mesure différentielle permettent d’obtenir une très grande précision. Les résultats de mesure peuvent être enregistrés sur le disque dur de la commande à des fins de documentation des procédés. De plus, il est possible d’imprimer un protocole de mesure au moyen d’une imprimante.
La machine fonctionne en principe comme un instrument de mesure machine 3D. Les systèmes de mesure de position des axes d’avance CN (règles en verre et systèmes de mesure rotatifs) sont employés pour la mesure du diamètre et de la longueur. Il se peut que l’utilisation d’une machine-outil en tant qu’instrument de mesure machine dans des conditions ambiantes difficiles pose des problèmes de précision de mesure et de stabilité à long terme. Il suffit de penser aux influences thermiques, qui peuvent être éliminées sur un instrument de mesure machine en l’installant dans une pièce climatisée.
La mesure de pièce intégrée apporte cependant de nombreux avantages pour le déroulement de la fabrication, si bien qu’elle est indispensable pour de nombreuses tâches de fabrication complexes.
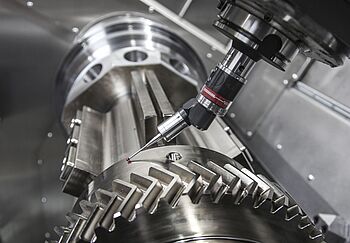
Mesure par balayage
Les systèmes de mesure sont confrontés à des défis de taille en ce qui concerne l’usinage de grandes pièces à usiner lourdes et complexes. Les systèmes de mesure par balayage permettent de réaliser des mesures numériques et des procédés de numérisation analogiques directement sur la machine. Le palpeur analogique génère en une fraction de seconde des milliers de valeurs de mesure sur la surface en une opération de « balayage ». Possibilité de mesure rapide et ce jusqu’à 2 m/min en cas de précision absolue. Cela permet une mesure de sphéricité, de circularité, de planéité, de forme et de denture entièrement automatique.
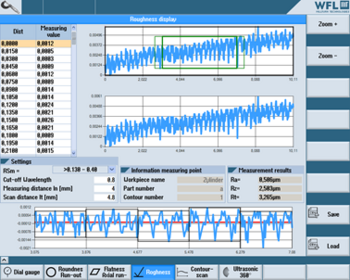
Mesure de pièce intégrée sur la tête de tournage-perçage-fraisage
Une variante spéciale est un palpeur de mesure fixe monté sur la tête de tournage-perçage-fraisage pour une mesure de pièce intégrée. Celui-ci peut être pivoté vers l’extérieur ou vers l’intérieur de manière entièrement automatique, sans changer l’outil d’usinage, ce qui permet de réduire le temps d’exécution d’une pièce à usiner. Il y a aussi des avantages en termes de précision, en cas de travail avec une passe de mesure avec des tolérances très faibles.
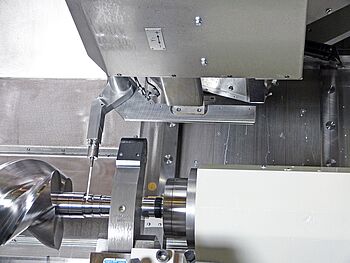
Mesure à ultrasons
L’unité de mesure à ultrasons permet de mesurer l’épaisseur de paroi des composants. Cette méthode est utilisée pour les longs tuyaux ou les contours intérieurs profonds, qui ne peuvent la plupart du temps pas être mesurés à l’aide d’un palpeur de mesure. Les cycles de mesure WFL permettent de mesurer et d’évaluer facilement les épaisseurs de paroi. Les différents algorithmes d’évaluation permettent par exemple de déterminer l’erreur de centrage d’un contour intérieur.
La mesure à ultrasons automatique de l’épaisseur de paroi a pour objectif une surveillance précise de la qualité ainsi qu’une détermination de la position du diamètre intérieur par rapport au diamètre extérieur (concentricité) sur les pièces à usiner en forme de tuyau pour lesquelles le point de mesure ne peut pas être atteint avec le palpeur de mesure de pièce à usiner traditionnel.
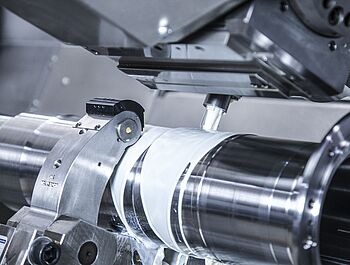
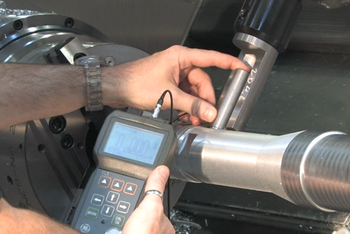
Mesure semi-automatique de l’épaisseur de paroi |
+ coûts très faibles |
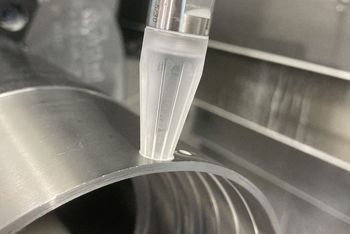
Mesure automatique de l’épaisseur de paroi avec palpeur de mesure interchangeable |
+ vaste plage de mesure de 1,5 à 30 mm |
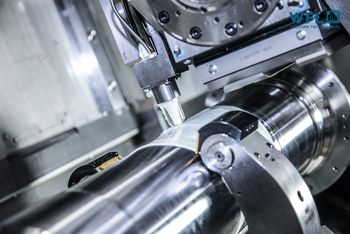
Mesure automatique de l’épaisseur de paroi avec palpeur de mesure pivotable |
+ possibilité de balayage à 360° |
Dispositif de calibrage avec compensation de température
Le dispositif de calibrage traversé par de l’eau stabilisée en température provenant de l’installation de refroidissement est monté sur la contre-poupée dans le sens de l’axe Y et muni d’un couvercle qui empêche la saleté de pénétrer dans le local de mesure.
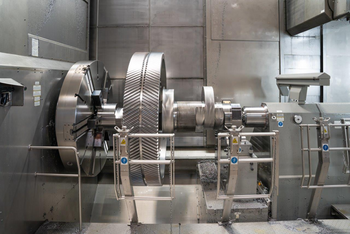