Messen
Höchste Fertigungsgenauigkeit für Ihre komplexen Werkstücke
Um komplexe Werkstücke mit hohen Qualitätsanforderungen prozesssicher herstellen zu können, ist es erforderlich, die Prozesse in einem „closed loop“ Verfahren zu steuern.
Durch die von WFL entwickelten Messverfahren wird höchste Fertigungsgenauigkeit bei engsten Maß- und Lagetoleranzen an komplizierten Werkstücken erreicht. Dabei stehen verschiedenste Messmittel zur Verfügung:
- Manuelles Messen
- In-Prozess-Messen
- Scannendes Messen
- Integrierte Werkstückvermessung an der Dreh-Bohr-Fräseinheit-Einheit
- Ultraschallmessen
- Kalibriereinrichtung inkl. Temperaturkompensation
Unsere Partner für punktgenaue Messungen sind die Unternehmen Blum, Hexagon und Renishaw.
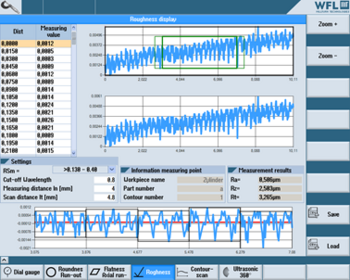
Manuelles Messen
Grundlegend kann das Messen in einem Fertigungsprozess in zwei Bereiche aufgeteilt werden: manuelles und automatisiertes Messen.
Beim manuellen Messen führt der Bediener die Messung und das Messdatenmanagement durch. Beim automatisierten Messen hingegen übernimmt die Maschine das Messen als auch das Messdatenmanagement.
Das manuelle Messen ist immer noch sehr stark in Produktionen verankert, da diese kostengünstiger sind als moderne Messmittel auf einen begrenzten Zeitraum gesehen. Jedoch muss bei manuellen Messungen die potentielle Fehlerquote, die Prozessunterbrechungen und die dadurch entstehende verlängerte Produktionszeit mit berücksichtigt werden.
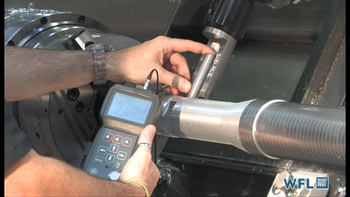
In-Prozess-Messen
Der in der Werkzeugmaschine eingesetzte, schaltende Messtaster ermöglicht in Kombination mit den nachfolgend beschriebenen Messzyklenpaketen die Einbindung verschiedener, intelligenter Mess- und Korrekturstrategien in den Fertigungsprozess. Dabei kann durch genaue, dem Wärmeausdehnungskoeffizienten von Stahl angepasste Linearmaßstäbe und Differenzmessverfahren eine sehr hohe Genauigkeit erreicht werden. Zur Prozessdokumentation können die Messergebnisse auf der Festplatte der Steuerung protokolliert werden. Weiters kann ein Messprotokoll über einen Drucker ausgedruckt werden.
Die Maschine arbeitet dabei im Prinzip wie eine 3D-Messmaschine, wobei hier die Lagemesssysteme der NC-Vorschubachsen (Glasmaßstäbe und rotative Messsysteme) zur Längen- bzw. Durchmessermessung verwendet werden. Es liegt in der Natur der Sache, dass der Einsatz einer Werkzeugmaschine mit ihren rauen Umgebungsbedingungen als Messmaschine gewisse Probleme bezüglich der Messgenauigkeit und Langzeitstabilität mit sich bringt. Man denke nur an die thermischen Einflüsse, die bei einer Messmaschine durch Aufstellung in einem klimatisierten Raum eliminiert werden können.
Die In-Prozess-Werkstückvermessung bringt jedoch viele Vorteile für den Fertigungsablauf mit sich, sodass bei vielen komplexen Fertigungsaufgaben nicht auf sie verzichtet werden kann.
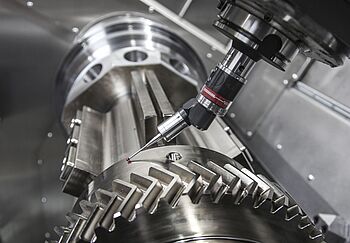
Scannendes Messen
Messsysteme stehen vor großen Herausforderungen, wenn es um die Bearbeitung großer, schwerer und komplexer Werkstücke geht. Mit scannenden Messsystemen können digitale Messungen und analoge Scanvorgänge direkt auf der Maschine durchgeführt werden. Der Analogtaster generiert durch „scannen“ über die Oberfläche in einem Bruchteil der Zeit tausende Messewerte. Schnelles Messen und zwar bis zu 2 m/min ist bei absoluter Genauigkeit möglich. Ein vollautomatisches Rundheits-, Rundlauf-, Planlauf-, Form- und Verzahnungsmessen wird dadurch möglich.
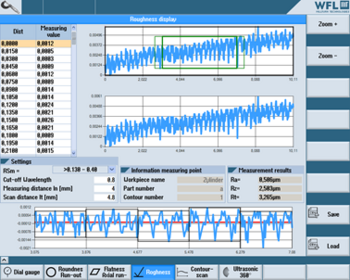
Integrierte Werkstückvermessung an der Dreh-Bohr-Fräseinheit-Einheit
Eine Sondervariante ist ein fix montierter In-Prozess-Messtaster an der Dreh-Bohr-Fräseinheit zur integrierten Werkstückvermessung. Dieser kann vollautomatisch aus- bzw. eingeschwenkt werden, ohne dabei das Bearbeitungswerkzeug auszuwechseln, was die Durchlaufzeit eines Werkstücks reduziert. Vorteile ergeben sich aber auch im Hinblick auf die Genauigkeit, wenn bei sehr engen Toleranzen mit Messschnitt gearbeitet wird.
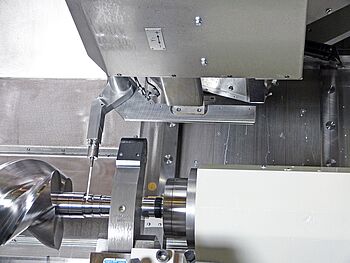
Ultraschallmessen
Die Ultraschallmesseinheit erlaubt es, die Wandstärke von Bauteilen zu messen. Eingesetzt wird diese Methode bei langen Rohren oder tiefen Innenkonturen, welche mit einem Messtaster meist nicht mehr gemessen werden können. Mit den WFL-Messzyklen werden auf einfache Art und Weise die Wandstärken gemessen und ausgewertet. Durch die verschiedenen Auswertungsalgorithmen lässt sich etwa der Zentrumsfehler einer Innenkontur bestimmen.
Die automatische Ultraschall Wanddickenmessung dient der genauen Qualitätsüberwachung sowie der Lagebestimmung von Innen- zu Außendurchmesser (Konzentrizität) bei rohrförmigen Werkstücken, bei denen die Messstelle mit dem herkömmlichen Werkstück-Messtaster nicht erreicht werden kann.
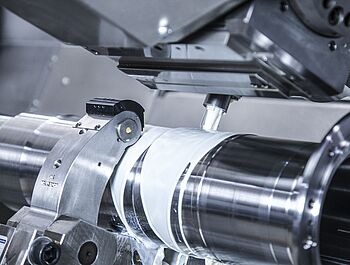
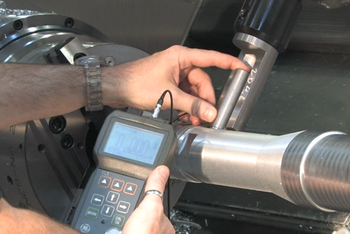
Semi-Automatische Wanddickenmessung |
+ sehr geringe Kosten |
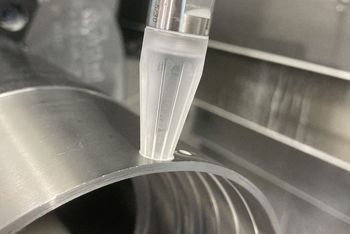
Automatische Wanddickenmessung mit einwechselbarem Messtaster |
+ großer Messbereich 1,5 - 30mm |
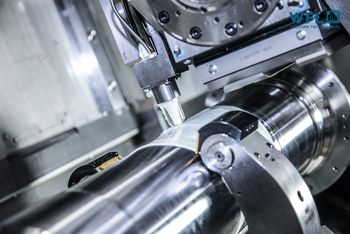
Automatische Wanddickenmessung mit einschwenkbaren Messtaster |
+360° scannen möglich |
Kalibriereinrichtung inkl. Temperaturkompensation
Die mit temperaturstabilisiertem Wasser aus der Rückkühlanlage durchströmte Kalibriereinrichtung ist in Richtung der Y-Achse am Reitstock montiert und mit einer Abdeckhaube versehen, die das Eindringen von Schmutz in den Messraum verhindert.
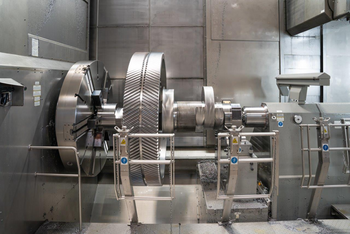