Measuring
Ultimate manufacturing accuracy for your complex workpieces
To manufacture complex parts with high quality requirements, processes must be controlled in a ‘closed loop’.
The measurement method developed by WFL enables maximum manufacturing precision to be achieved with the tightest dimensional and positional tolerances on complex workpieces. A range of measuring tools are available to this end:
- Manual measuring
- In-process measuring
- Scanning measurement
- Integrated workpiece measurement at the turning-boring-milling unit
- Ultrasonic measurement
- Calibration device incl. temperature compensation
We work together with the companies Blum, Hexagon and Renishaw to ensure the most precise measurements possible.
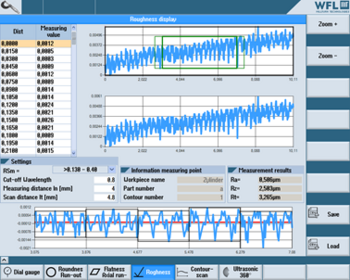
Manual measuring
In the manufacturing process, measurements can essentially be divided into two types: manual and automated measurements.
In the case of manual measurements, the operator is responsible for taking the measurements and managing the measurement data. In the case of automated measurements, on the other hand, the machine takes care of the measurements and of management of the measurement data.
Manual measurement is still commonly used in manufacturing as it is cheaper than using modern measuring equipment over the short term. However, with manual measurements it is necessary to take into account the potential error rate, process interruptions and the resulting increase in production times.
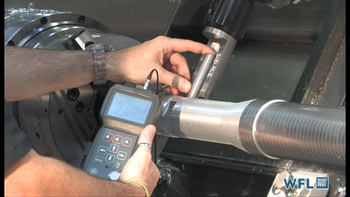
In-process measuring
In combination with the measurement cycle packages described below, the switching measuring probe used in the machine tool allows the integration of a range of smart measurement and correction strategies in the manufacturing process. This allows a very high level of accuracy to be achieved thanks to the precise linear scales adjusted to the thermal expansion coefficients of steel and the differential measurement process. The measurement results can be stored on the hard drive of the control system for the purpose of process documentation. A measuring protocol can also be printed out on a printer.
The machine essentially functions like a 3D measuring machine, except the position measuring systems of the NC feed axes (glass scales and rotating measurement systems) are used to measure length and diameter. Using a machine tool as a measuring machine necessarily brings about problems with measurement accuracy and long-term stability due to the tough environment in which it operates. Consider, for example, the thermal influences that can be eliminated by installing a measuring machine in a room with air-conditioning.
However, there are many benefits to in-process workpiece measurement, which has become an essential feature of many complex manufacturing tasks.
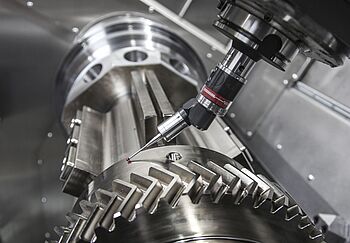
Scanning measurement
The machining of large, heavy and complex workpieces poses significant challenges for measuring systems. With scanning measurement systems, digital measurements and analogue scanning processes can be carried out directly on the machine. The analogue probe ‘scans’ the surface to generate thousands of measurement values in the blink of an eye. Quick measurements of up to 2 m/min are possible with complete accuracy. This makes fully automatic roundness, run-out, axial run-out, shape and teeth measurement possible.
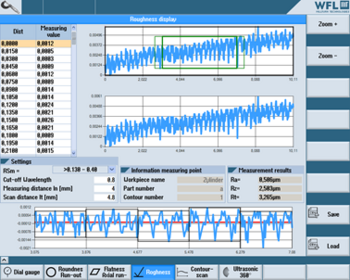
Integrated workpiece measurement at the turning-boring-milling unit
One special variant is an in-process measuring probe fixed on the turning-boring-milling unit for integrated workpiece measurement. This can be swivelled in or out fully automatically without swapping the machining tool, thereby reducing workpiece lead time. It also has a beneficial effect on precision when working with measuring cuts for very tight tolerances.
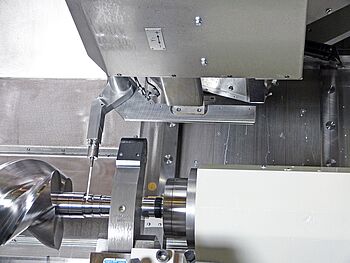
Ultrasonic measurement
The ultrasound measuring unit enables measurement of the wall thickness of components. This method is used for long pipes or deep internal contours that cannot be measured using a measuring probe. The WFL measuring cycles allow wall thicknesses to easily be measured and analysed. For example, the different analysis algorithms can be used to determine the centring error of an internal contour.
Automatic ultrasonic wall thickness measurement is used for precise quality monitoring as well as position determination of inside to outside diameter (concentricity) for tube-shaped workpieces for which the measuring point cannot be reached with conventional workpiece measuring probes.
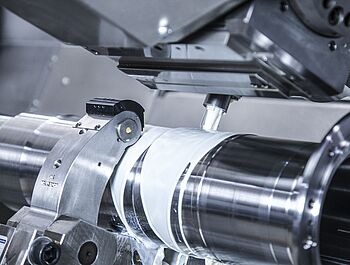
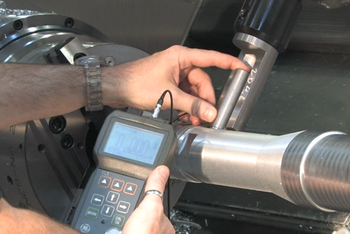
Semi-automatic wall thickness measurement |
+ Very cost-effective |
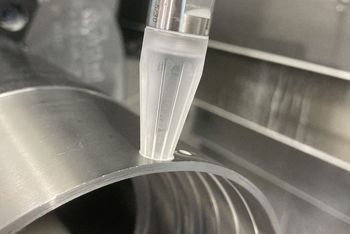
Automatic wall thickness measurement with automatically loading measuring probe |
+ Large measuring range of 1.5–30 mm |
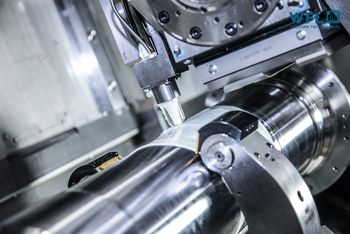
Automatic wall thickness measurement with swivelling measuring probes |
+ 360° scanning possible |
Calibration device incl. temperature compensation
Temperature-stabilised water from the coolant system flows through the calibration device, which is mounted on the tailstock in the direction of the Y-axis and has a cover which prevents ingress of dirt into the measurement space.
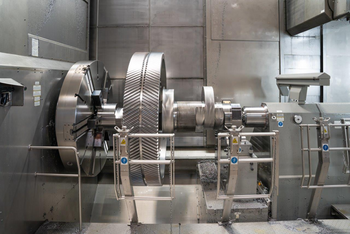