WFL cycles
The right cycle for every machining job
Standard cycles
Turning, drilling and milling
The technology cycles from WFL simplify programming considerably and are a direct route to achieving the desired production result. The wide range of technology solutions fulfils all machining requirements.
- Thread turning
- Grooves
- Relief grooves
- Machining with contour protection
- Thread relief grooves
- Thread cutting
- Chains of threads
- Drilling, grinding and cutting with dwell time
- Drilling with chip breaking
- Deep hole drilling
- Tapping with or without compensating chuck
- Boring
- Gun drilling
- Drilling with variable feed
- Milling of cylindrical and conical threads
- Face milling on cylindrical pieces
- Milling of key slots
- Turn-milling
- Face milling
- Contour milling
- Milling of rectangular studs
- Milling of circular studs
- Milling of rectangular pockets
- Milling of circular pockets
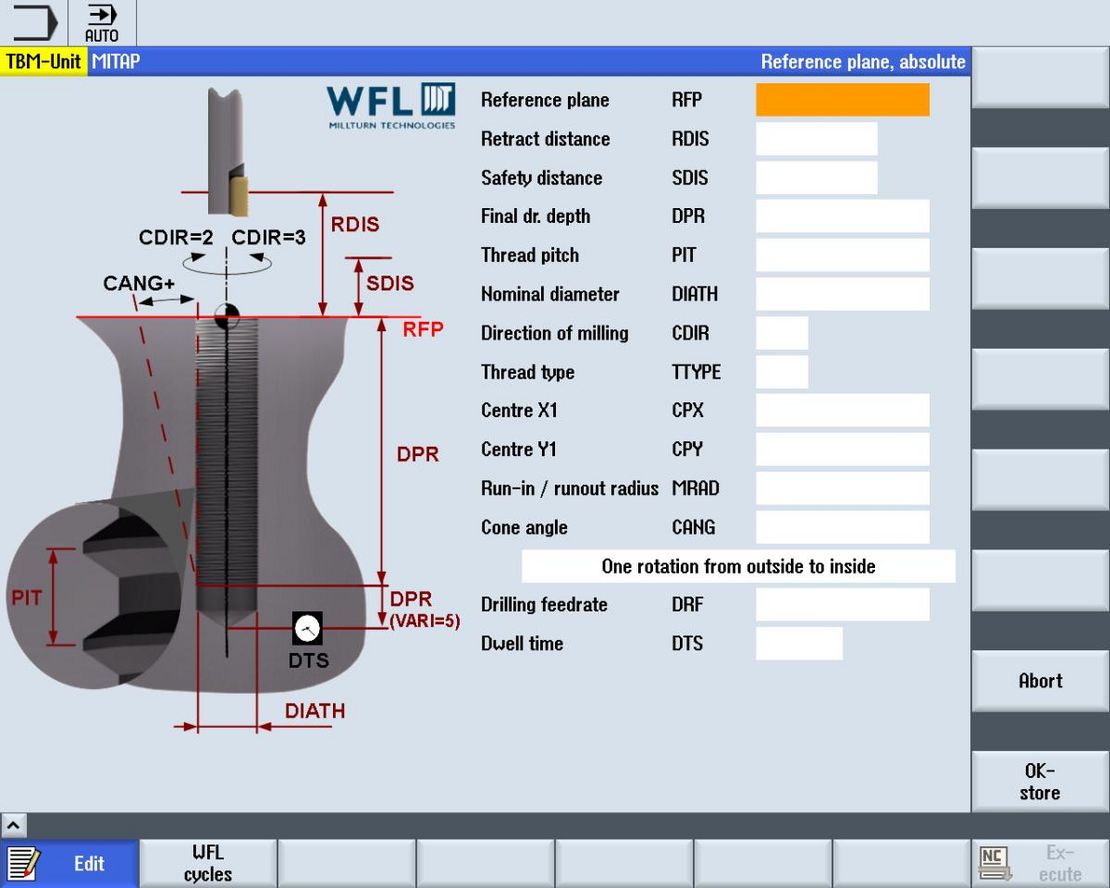
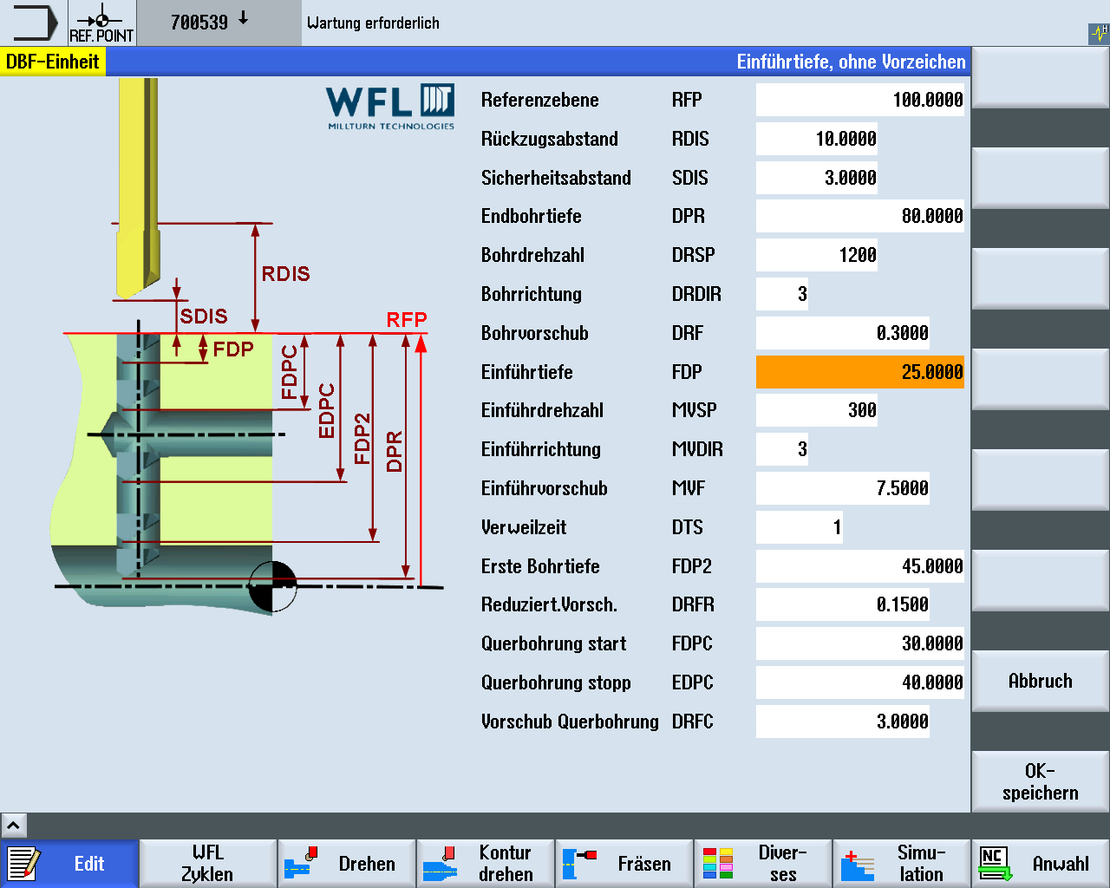
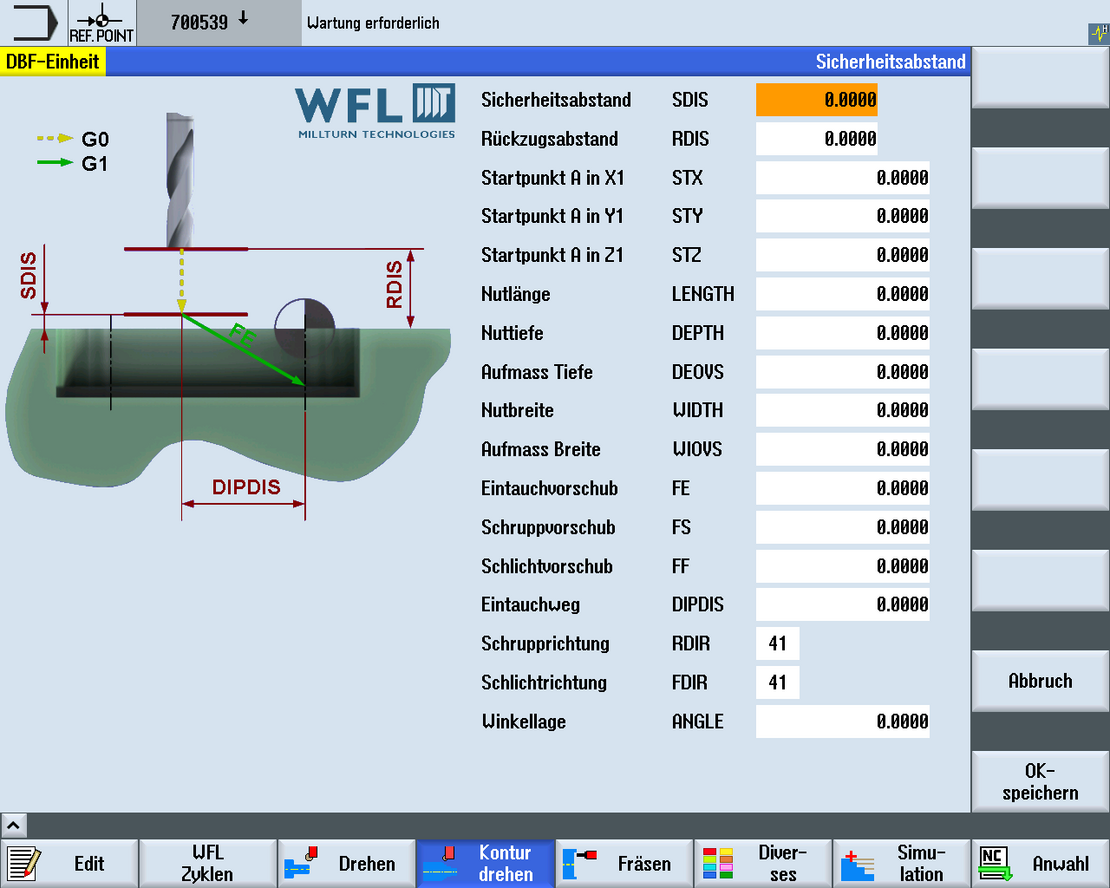
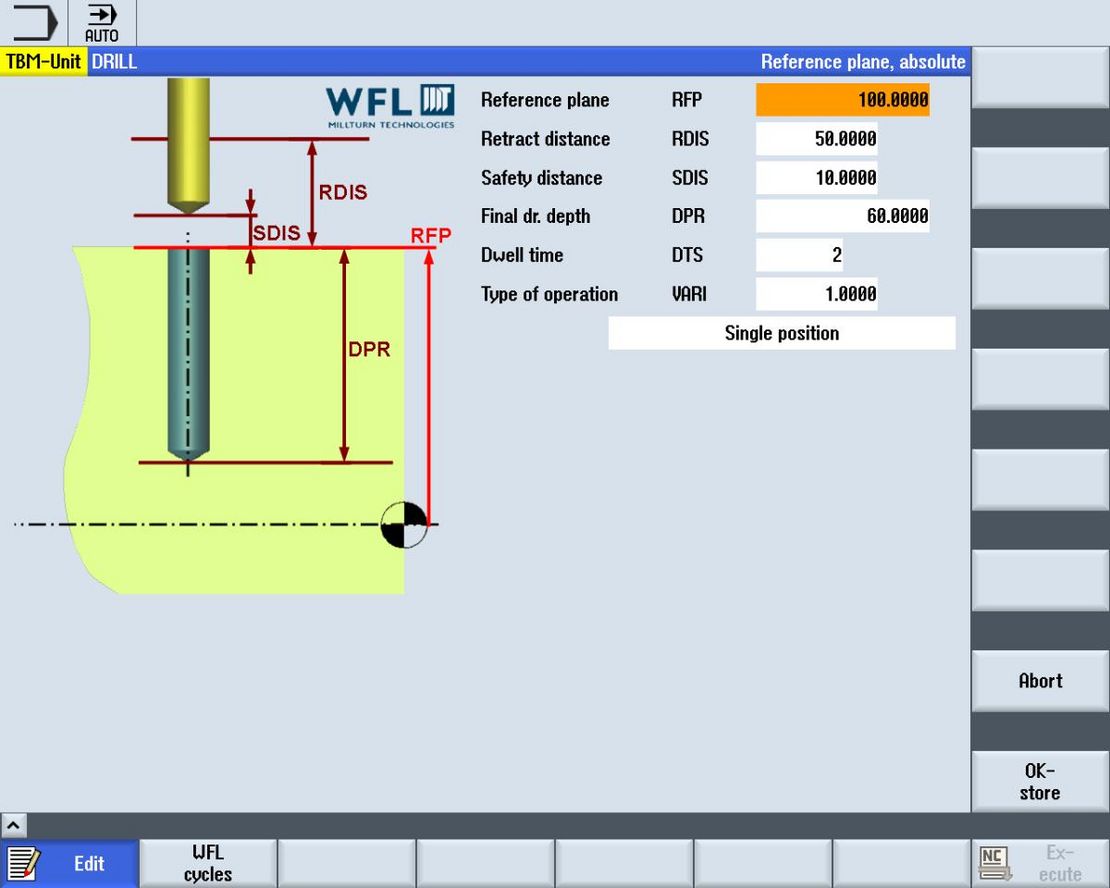
Machining and feed out
Cycle packages for crankshaft machining, for complex multi-axis machining with feed out tools or for a workpiece finish using grinding clearly show that a needs-based cycle configuration allows sector-specific requirements to be handled quickly and efficiently.
Cranx – The Crankshaft Profiler
- Cranx-Basic (basic crankshaft package)
- Cranx-Advanced (extended crankshaft package)
- Cranx-Plus (complete crankshaft package)
Utronix – The Virtual U-axis
- Utronix (virtual U-axis)
Other optional cycles:
- Function package for non-rotating feed out tools (bottle boring)
- Function package for rotating feed out tools (tools for U-axis)
- 5-axis machining package and turning with swivelling B-axis
- Turning VAM threads
- Inscribing workpieces
- Deburring by means of 3-axis interpolation (centric holes)
- Rounding of centric holes (3-axis with ball nose type cutter)
- Function package for rounding of (oblique) oil holes
- Function package for grinding work
- Rounding of 90° holes (5-axis with profile milling cutter)
- Cam milling
- Turn-milling of pistons
- Turn-milling of pressure cylinders
- Machining of pilger mill rollers
- Transmission and milling of cylindrical tracks
- Spline interpolation
- 3D tool radius correction
- Engraving the Data Matrix Code
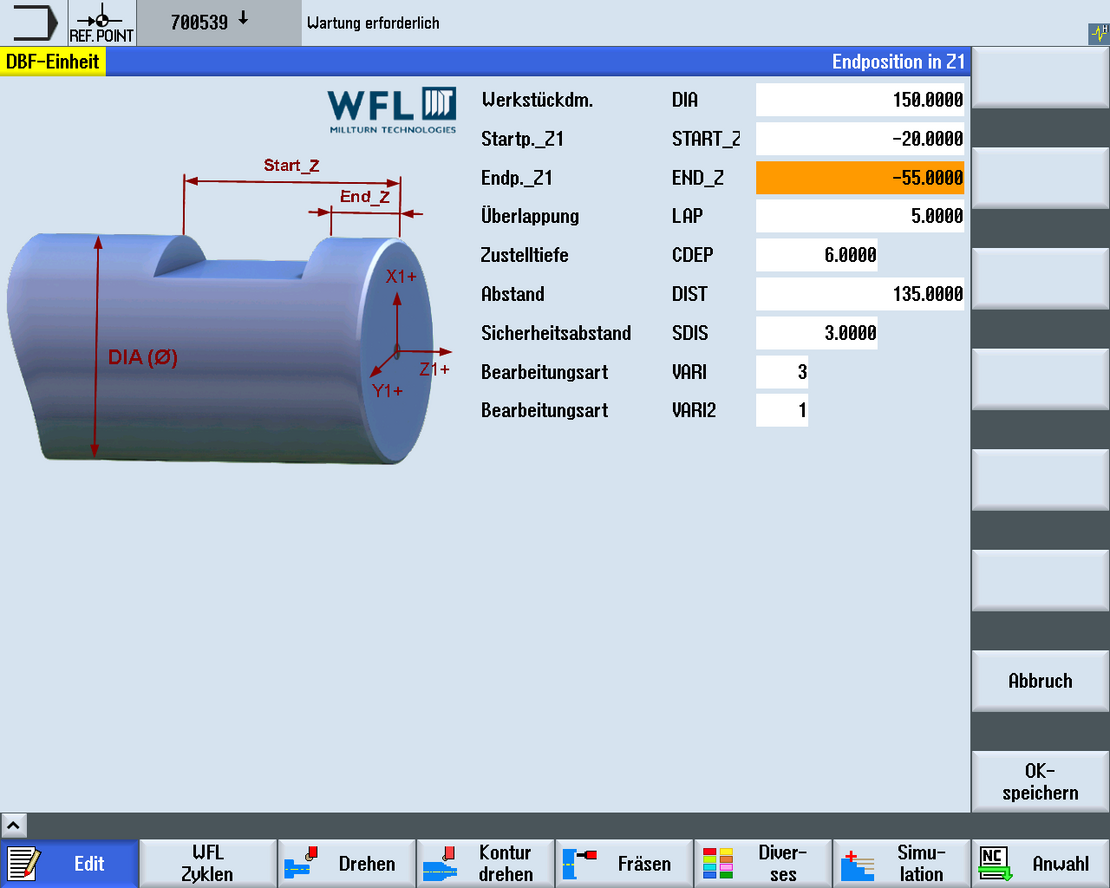
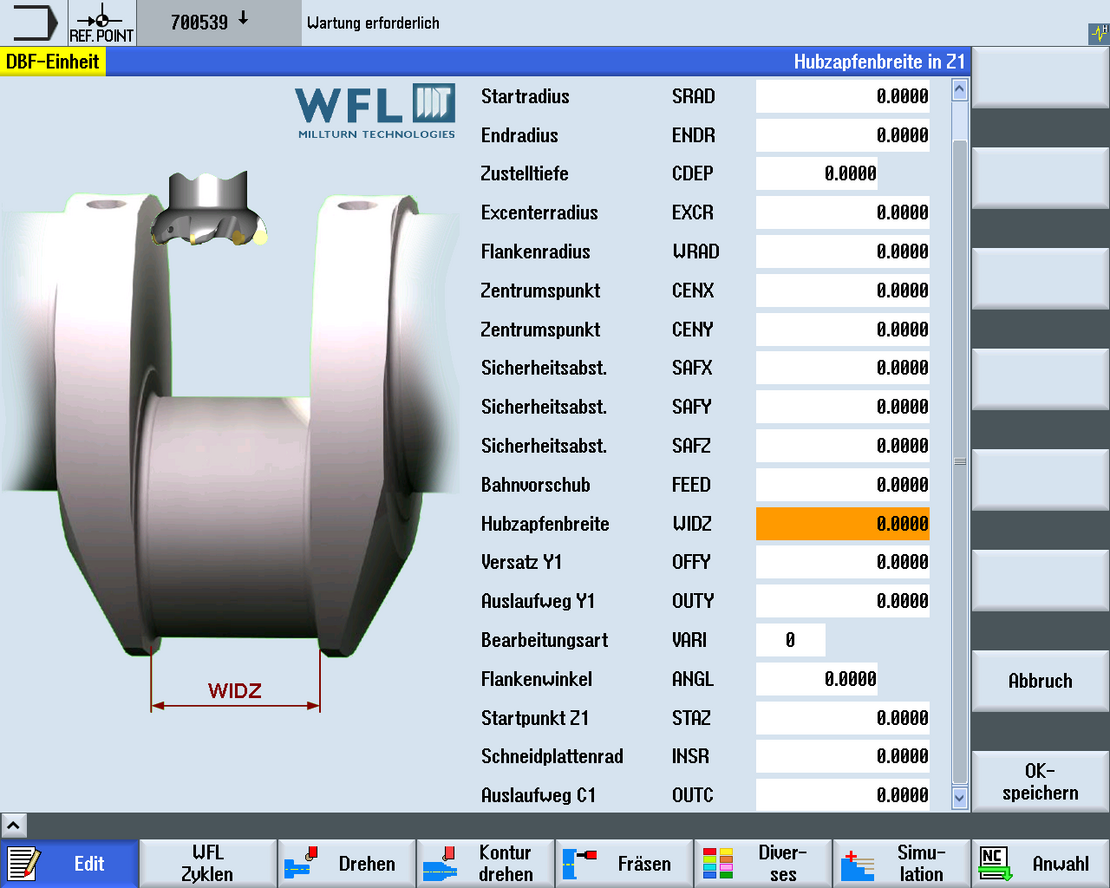
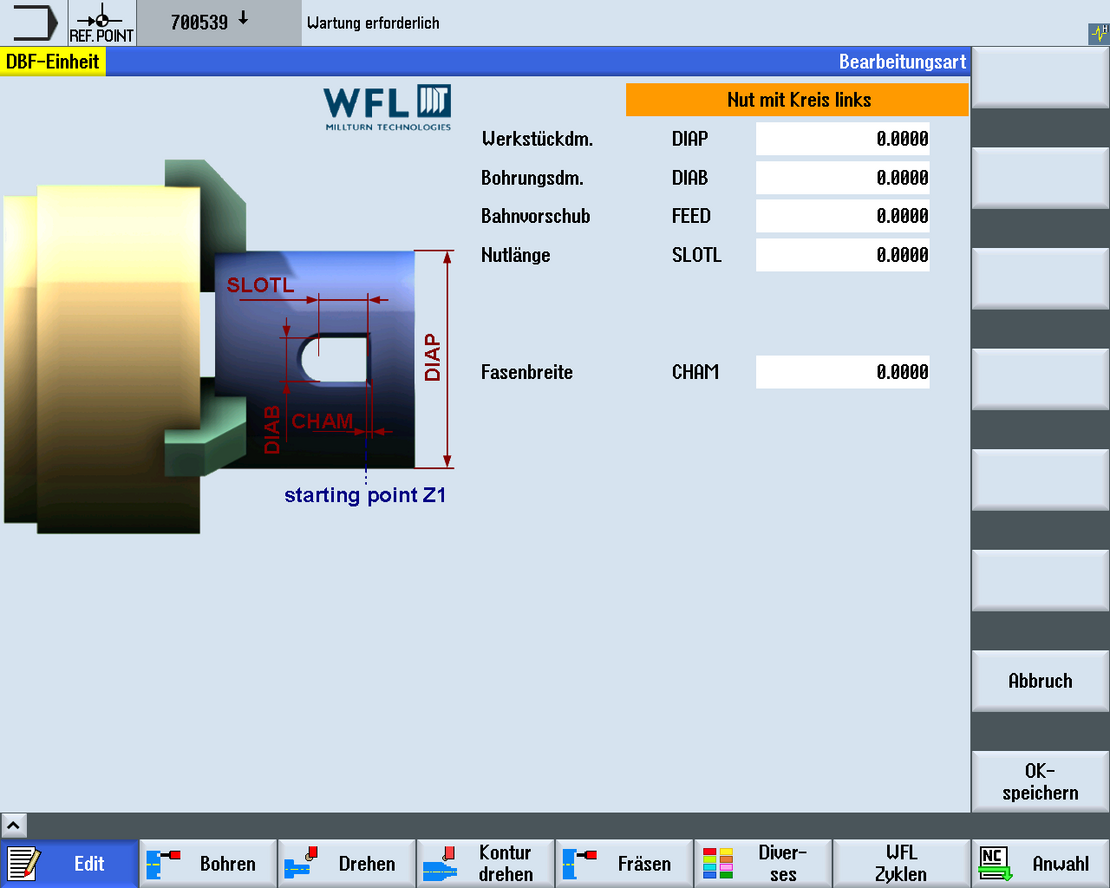
Gear cutting
From filigree internal gears with high accuracy requirements to large external gears that require high roughing efficiency – WFL offers the appropriate technological solution for every type of gear cutting.
- Flanx-Hob (for gear hobbing of external gears)
- Flanx-Spline (for shaping of external and internal gears)
- Flanx-Plus (Flanx-Hob and Flanx-Spline as a cycle package)
- Flanx-LM (for milling of large gears with standard milling tools)
- Flanx-Invo (for milling of external gears)
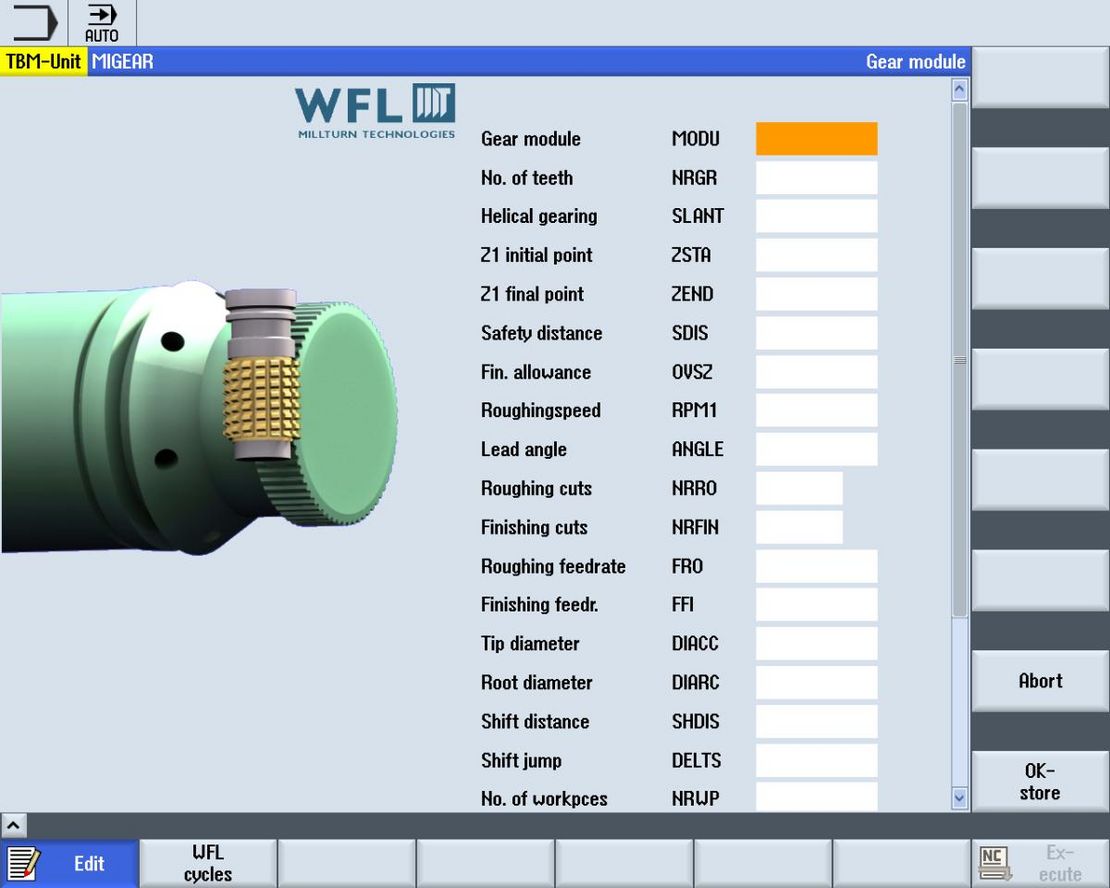
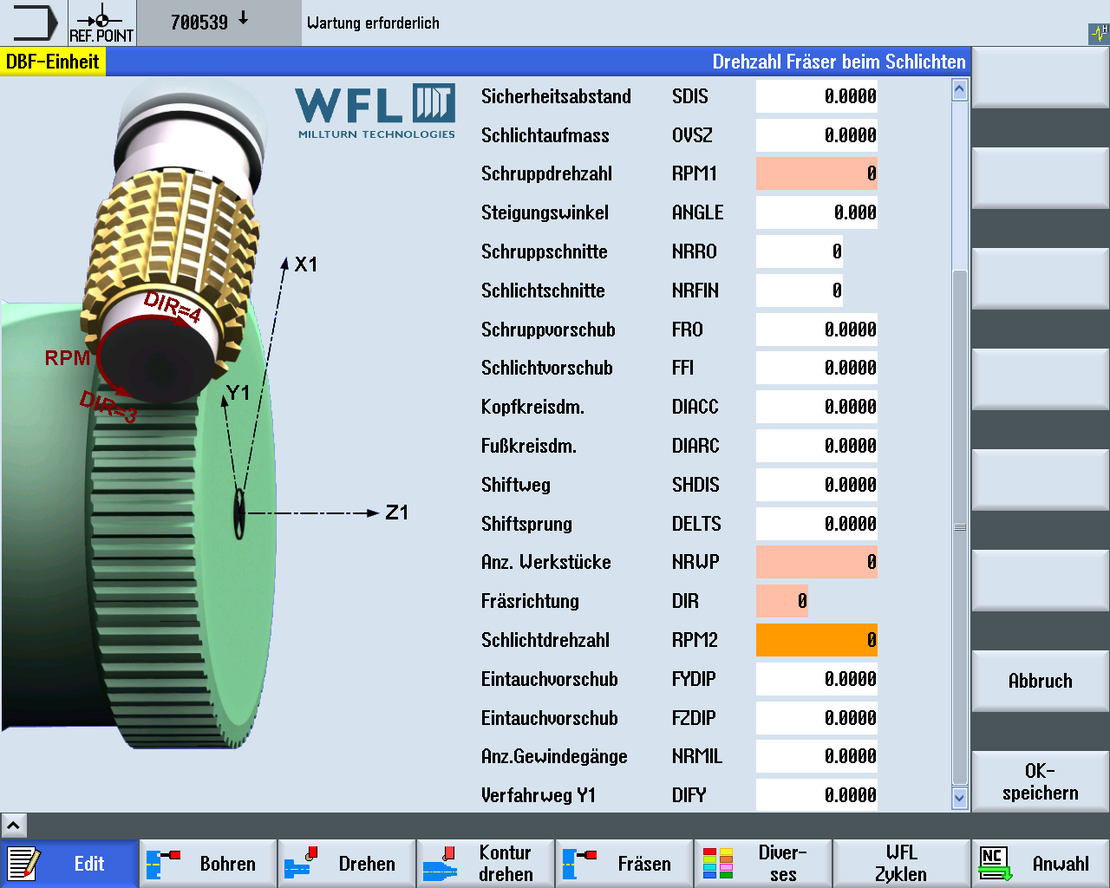
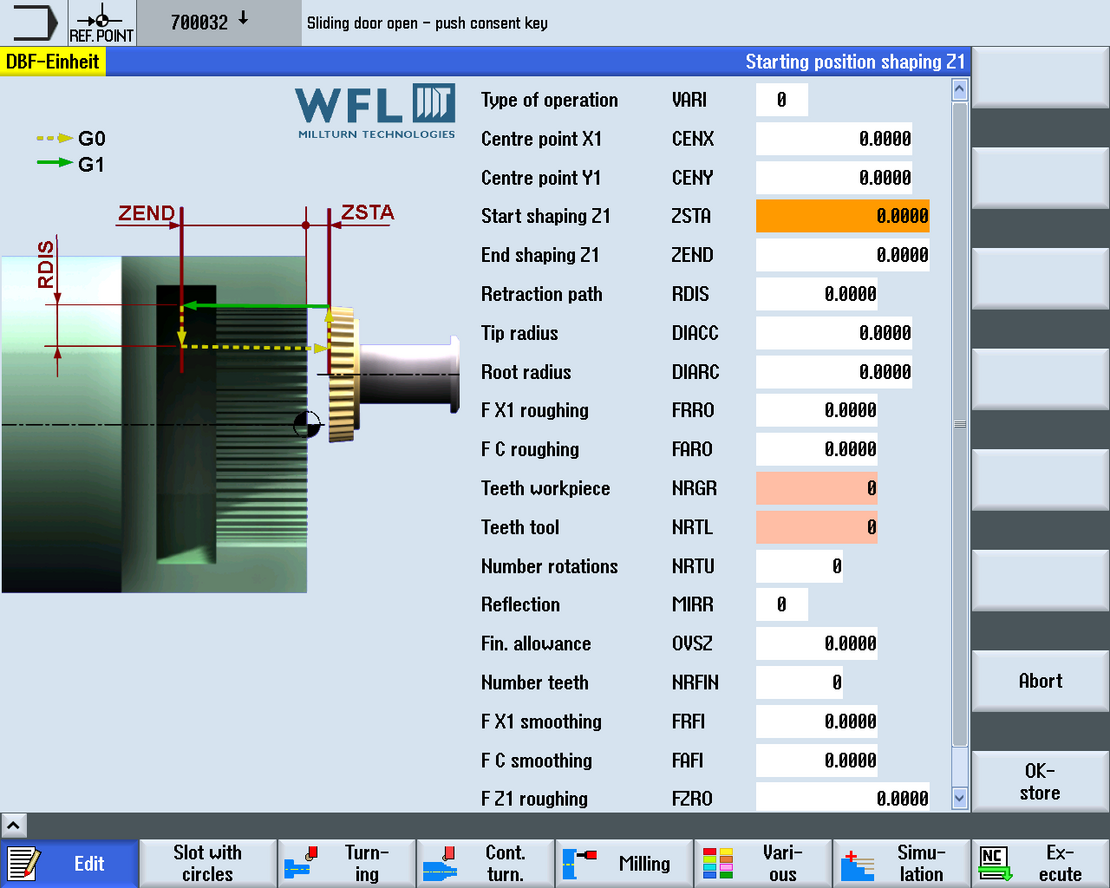
Measuring
High-precision measuring probes, linear direct measuring systems and backlash-free anti-friction guideways transform the MILLTURN into a 3D measuring machine. WFL provides the user with comprehensive modular measuring software and proven expertise for intelligent measuring strategies, which serve to exclude as many error-causing variables as possible, right from the very start.
Standard measurement cycle package
- Probing with any axis
- Two-point measurement
- Storage in measuring point compensation memory or zero-point offset
- Calibration of measuring probe
Extended measurement cycles package
- Parallelism check on the milling spindle axis to the Z1-axis
- Ultrasound wall thickness measurement
- Wireless transfer of measurement data from hand-held measurement devices
- Function package for measuring roundness and concentricity
- Recording of measurement data on hard drive
- Incremental tool correction via metal contact
Recording measurement data
Scanning
- Roundness, run-out, flatness and axial run-out
- Surface measurement
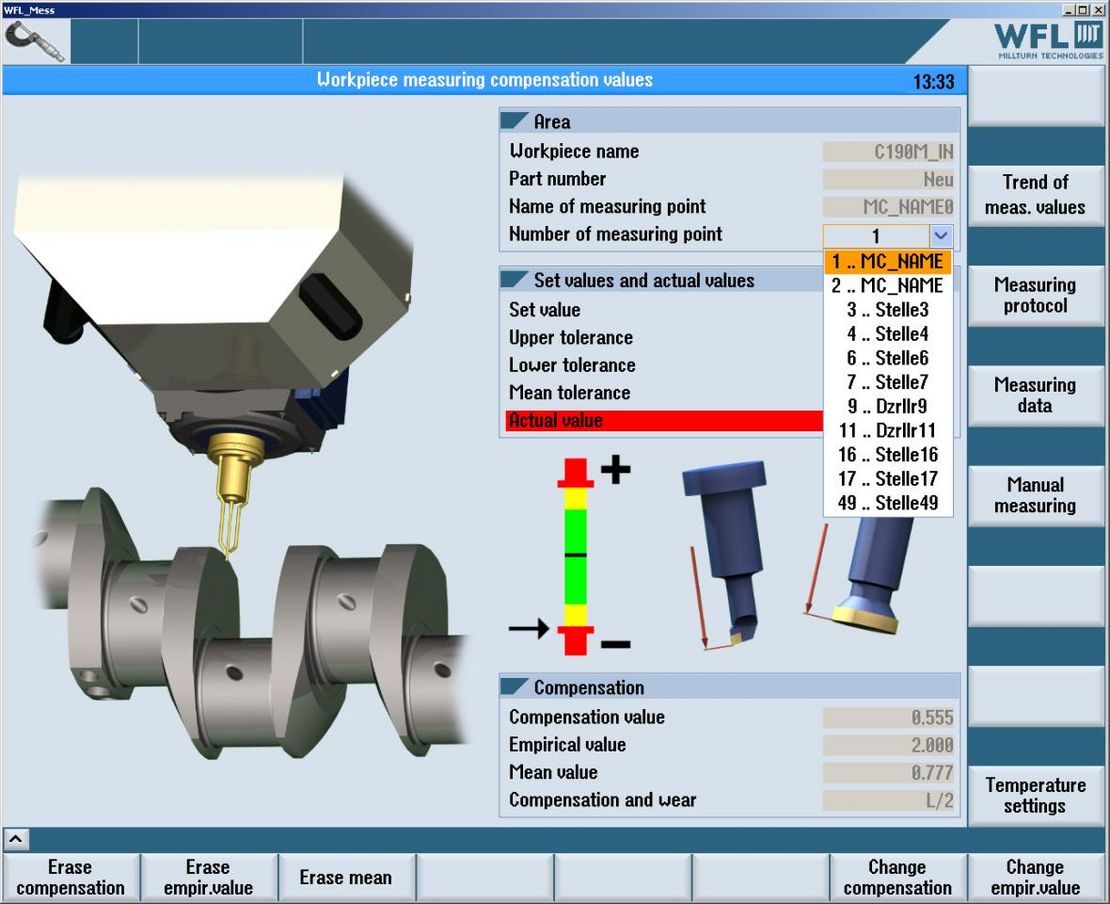
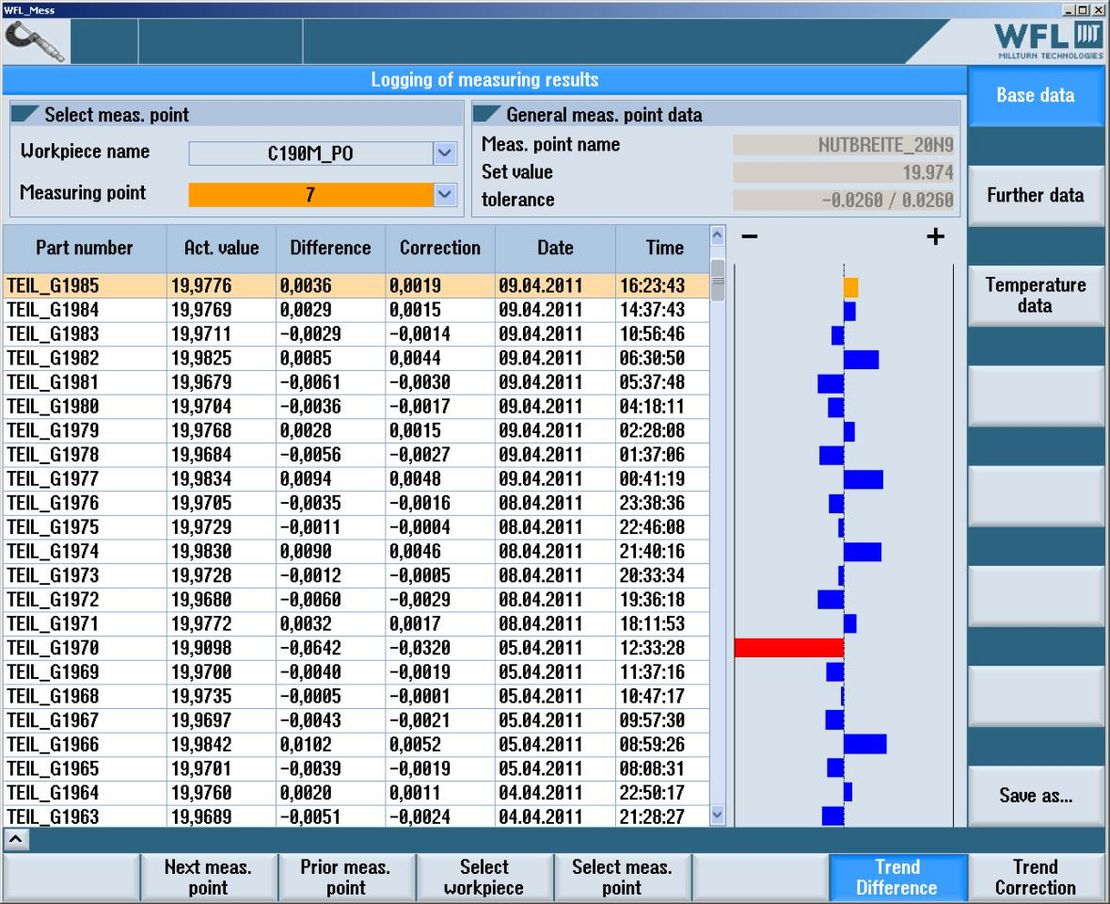
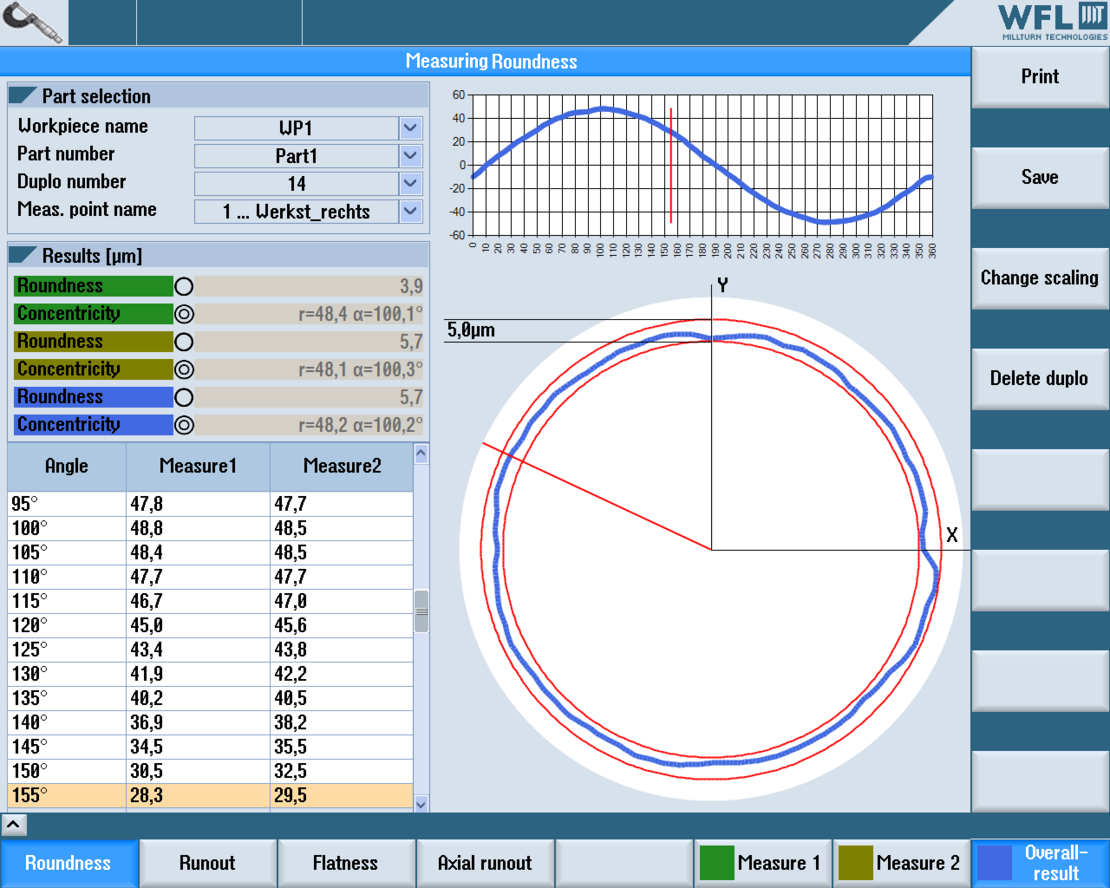
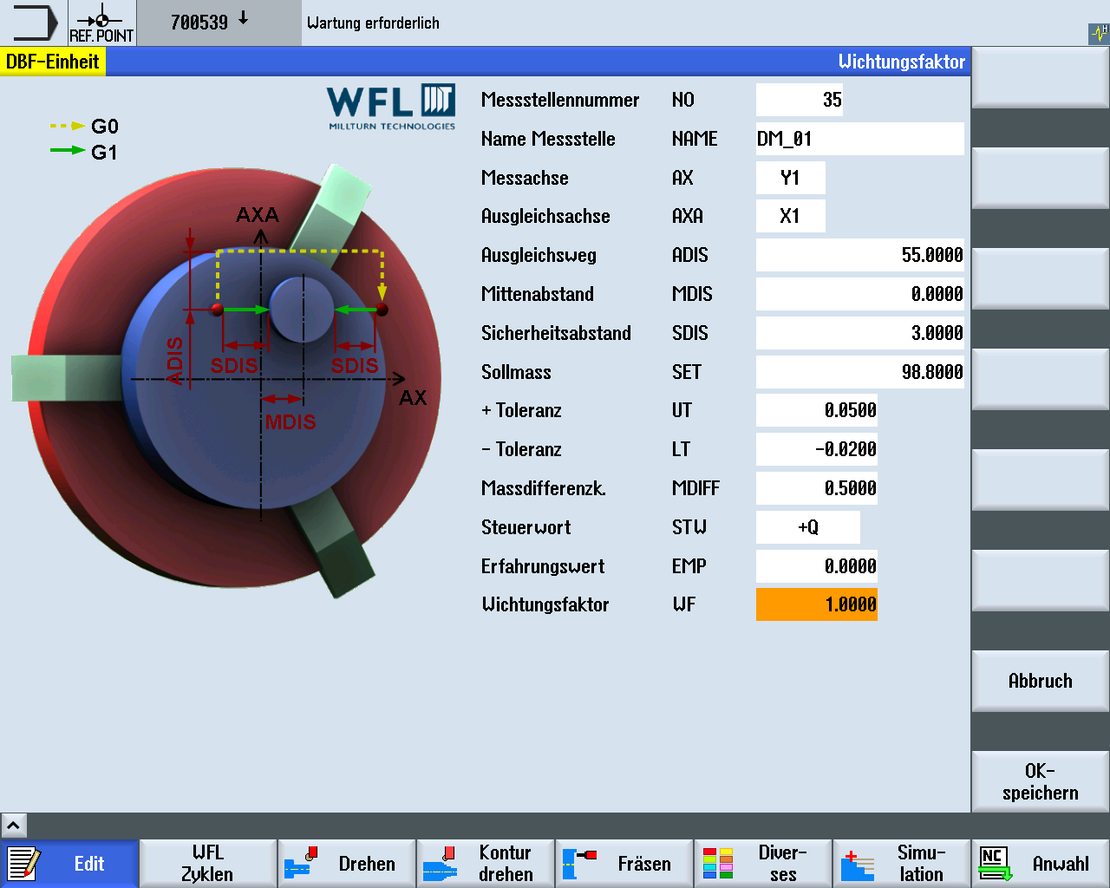
Tool control
Turning, drilling and milling tools can be measured using the tool control cycles.
- Calibrating the tool probe
- Measuring the tool automatically
- Measuring the cutting radius
- Measuring the tool manually
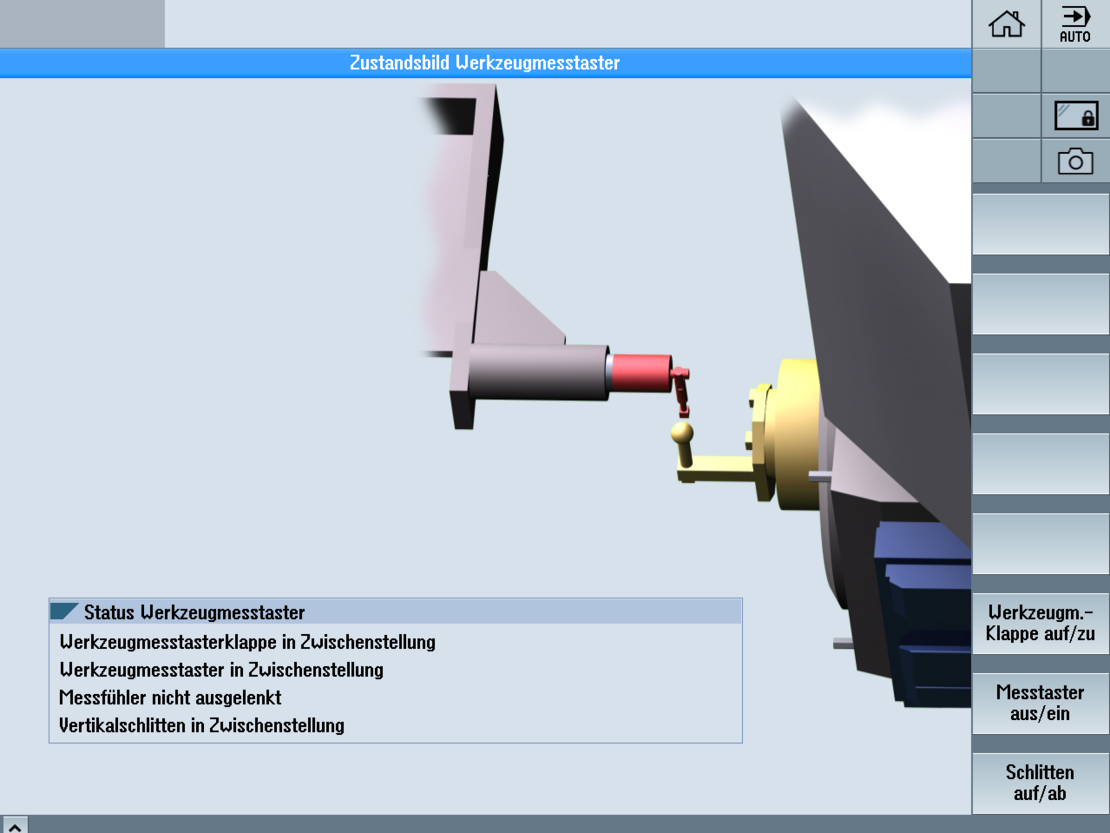

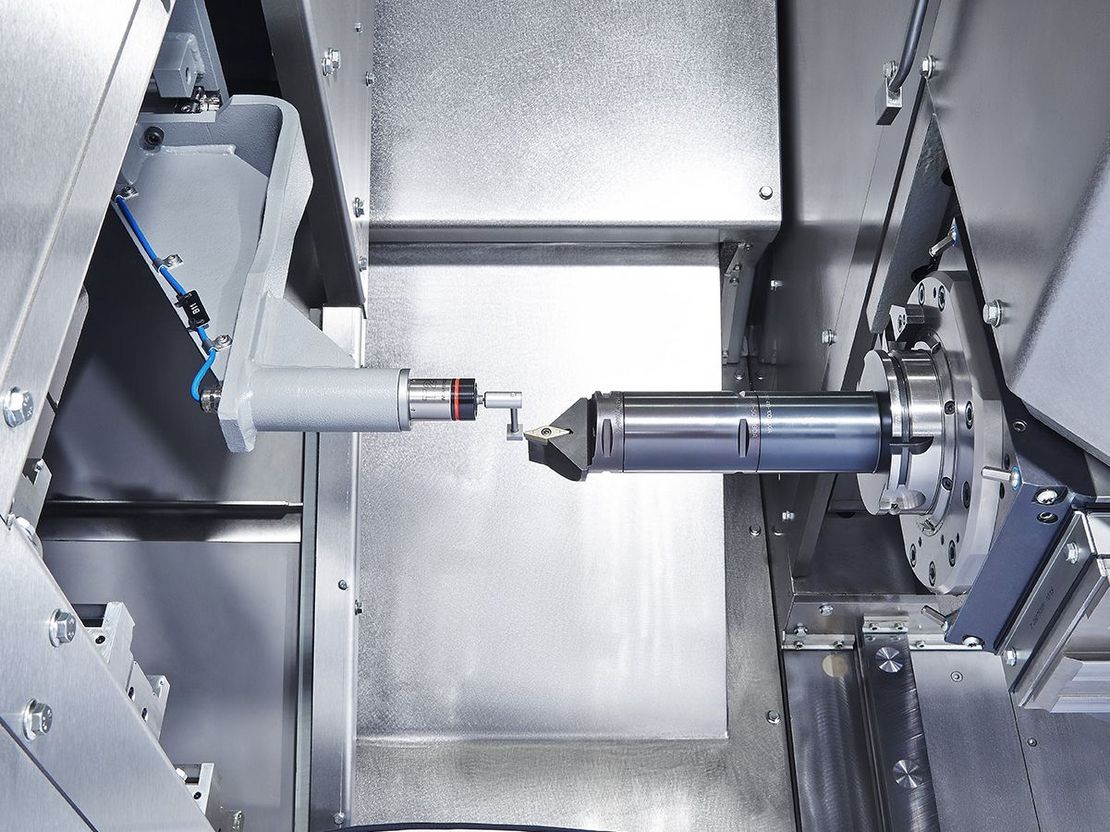
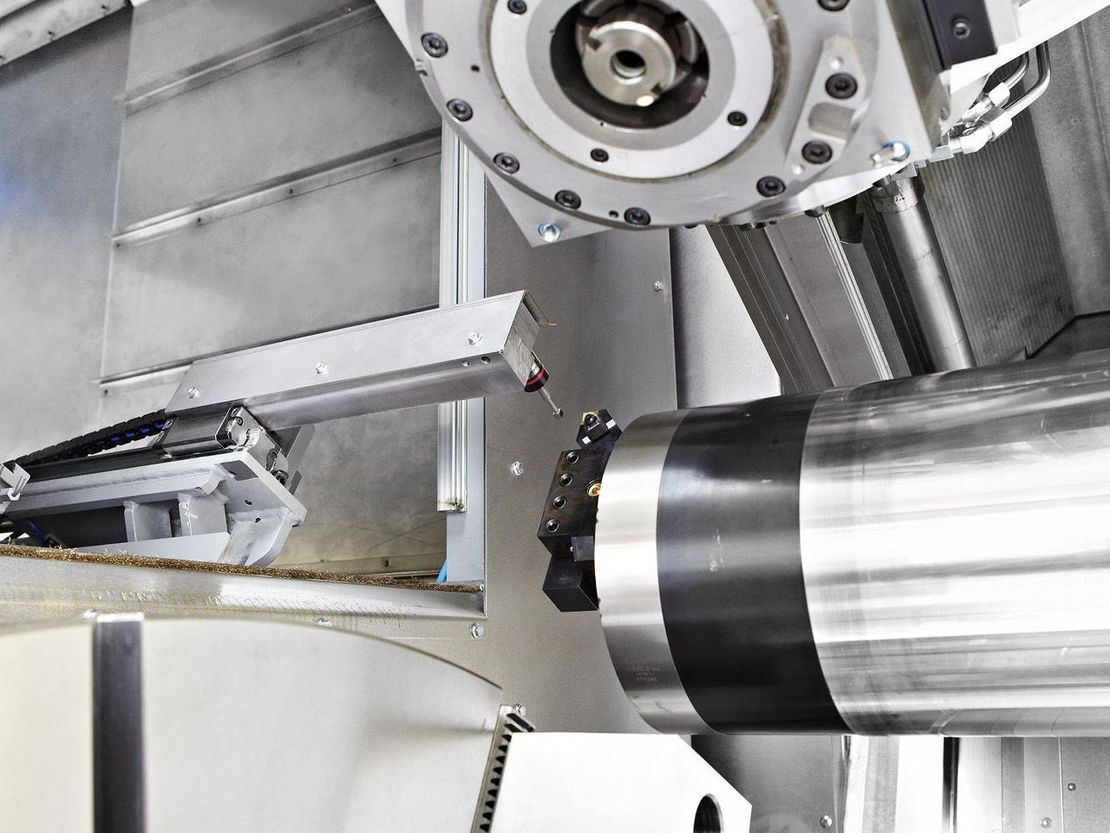
Tool management
All information relating to the existing tools is organised in a uniform manner thanks to the tool management software solutions. This makes it possible to achieve a considerable reduction in the set-up time and minimise tool costs, as the tools are always used until the end of their life.
- Tool management
- Tool identification system
- Virtual magazine
- Tool data archive
- Tool master database
- Tool requirement management
- Tool messenger
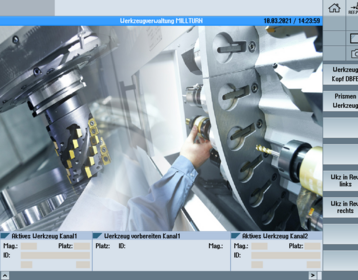
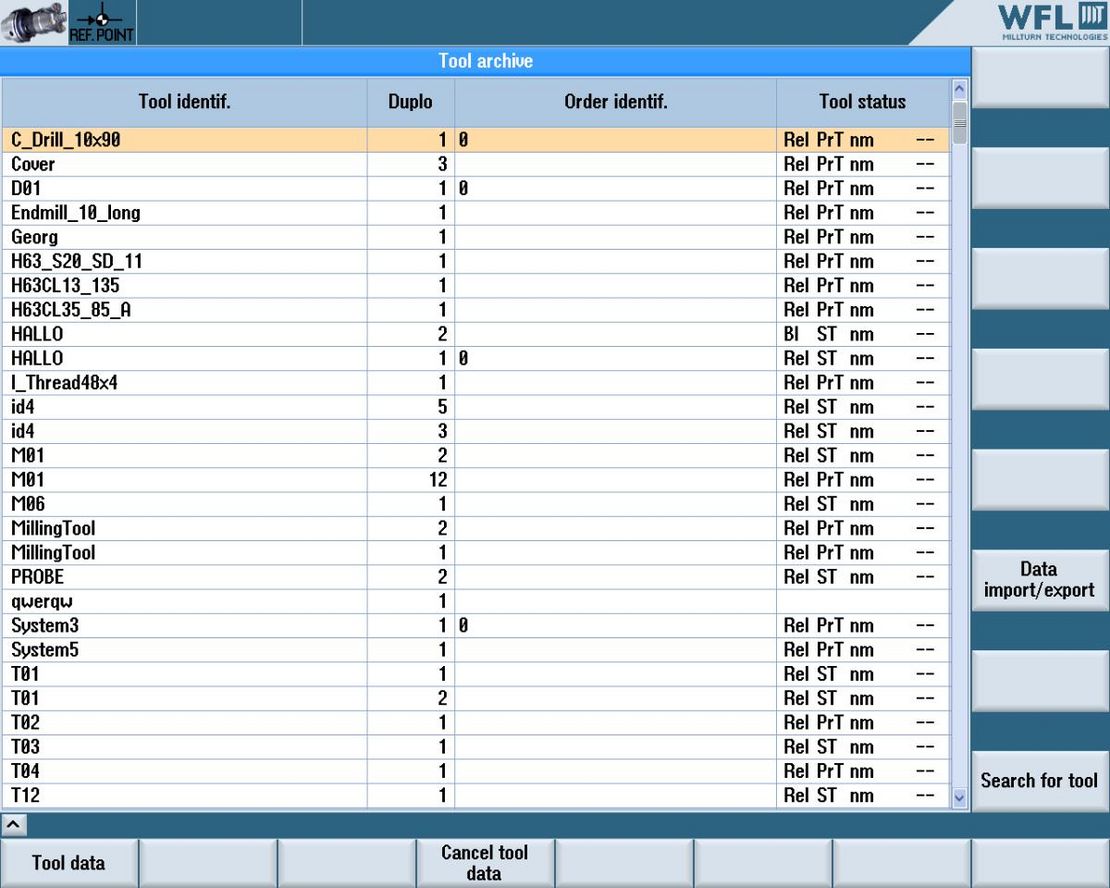
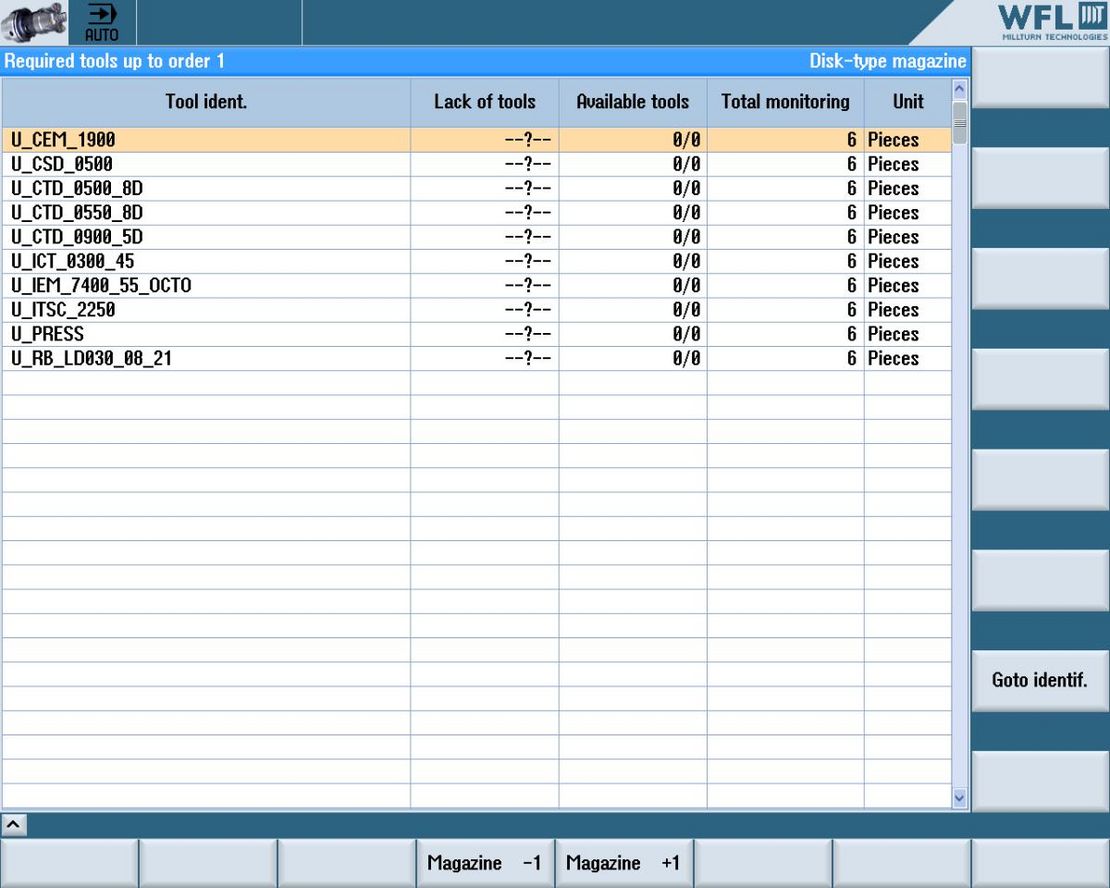
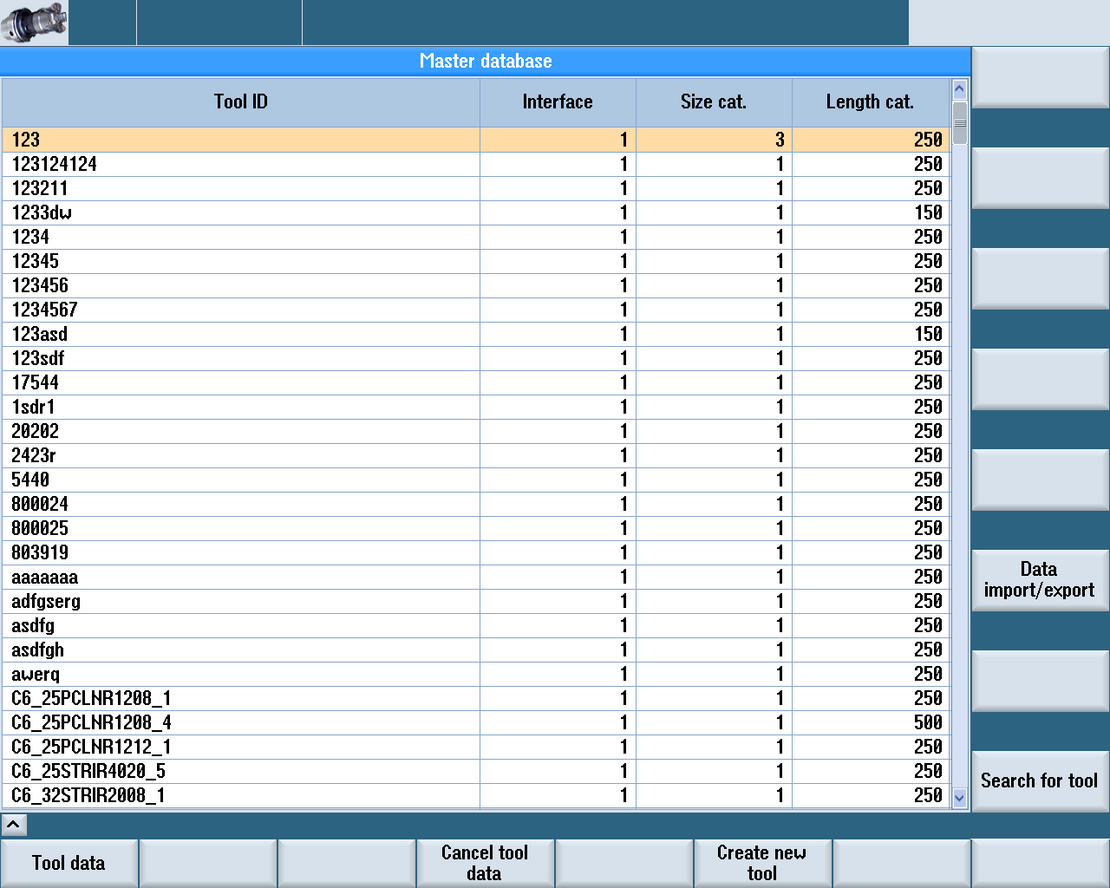
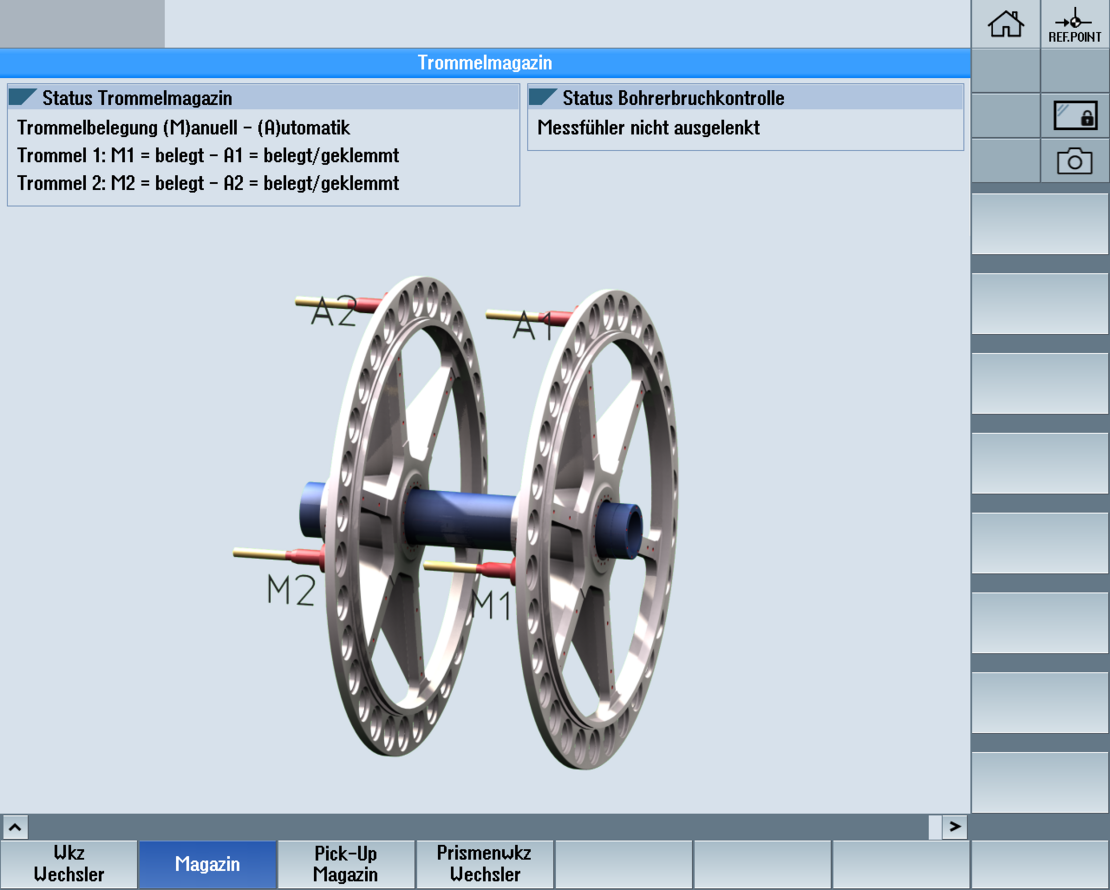
Process optimisation
Intelligent software solutions for increasing efficiency ensure a reliable blank machining process with variable stock without overloading machines and tools and without user interventions.
- Adaptive control (for feed and spindle speed)
- Torque and speed restriction of the milling spindle
- Automatic geometric check
- Process time recording
- Coolant unit control with pressure control and flow monitoring
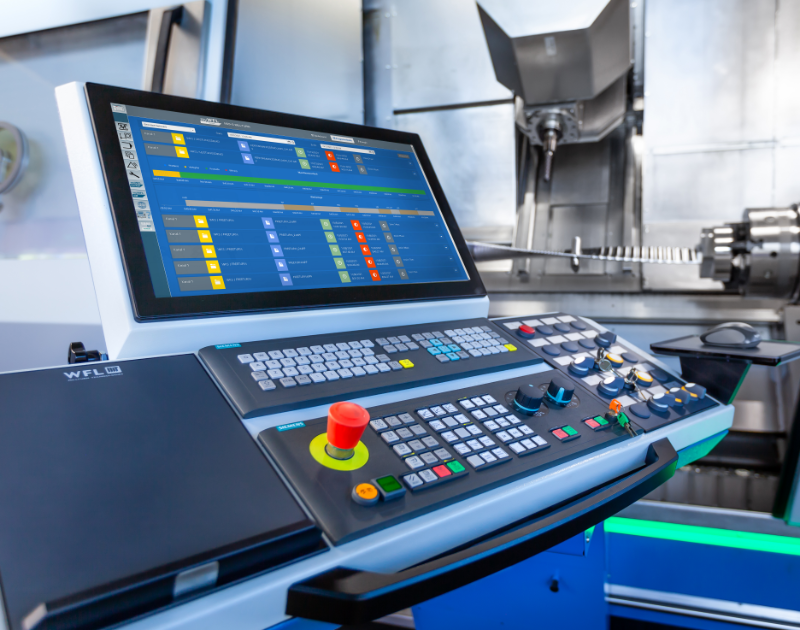
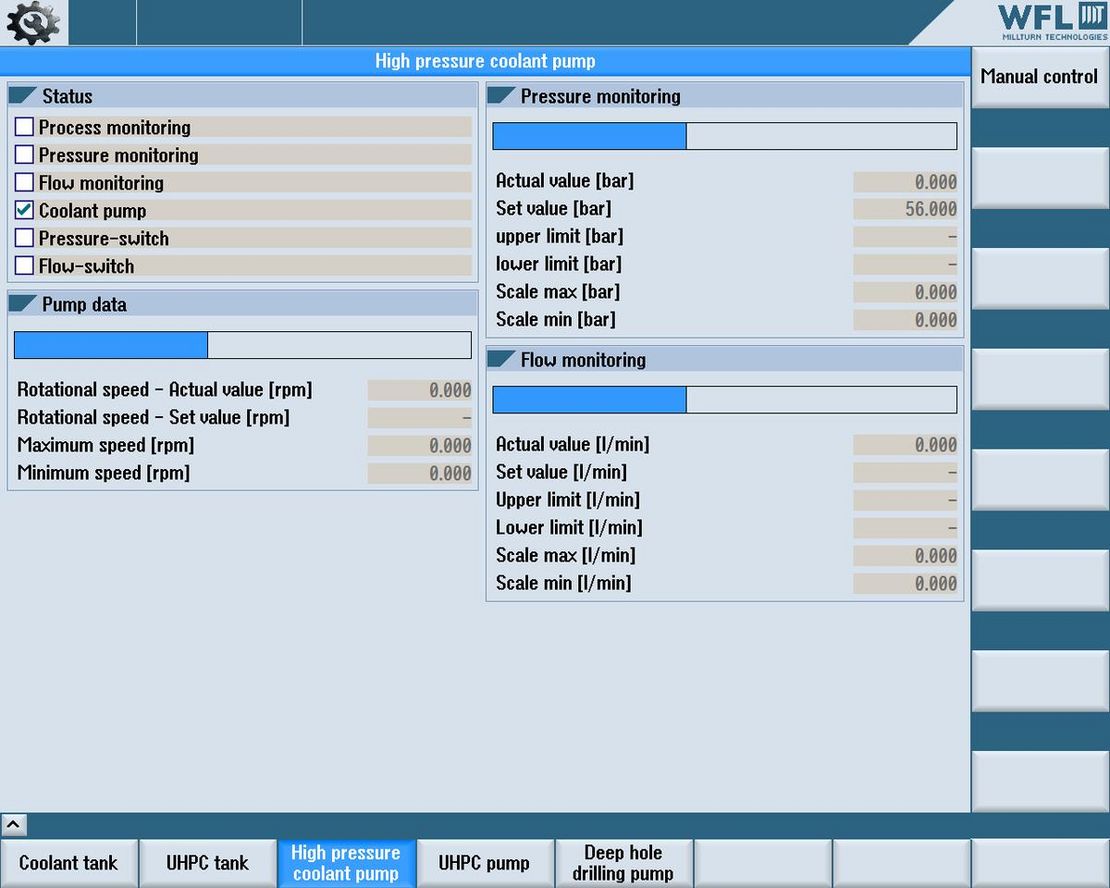
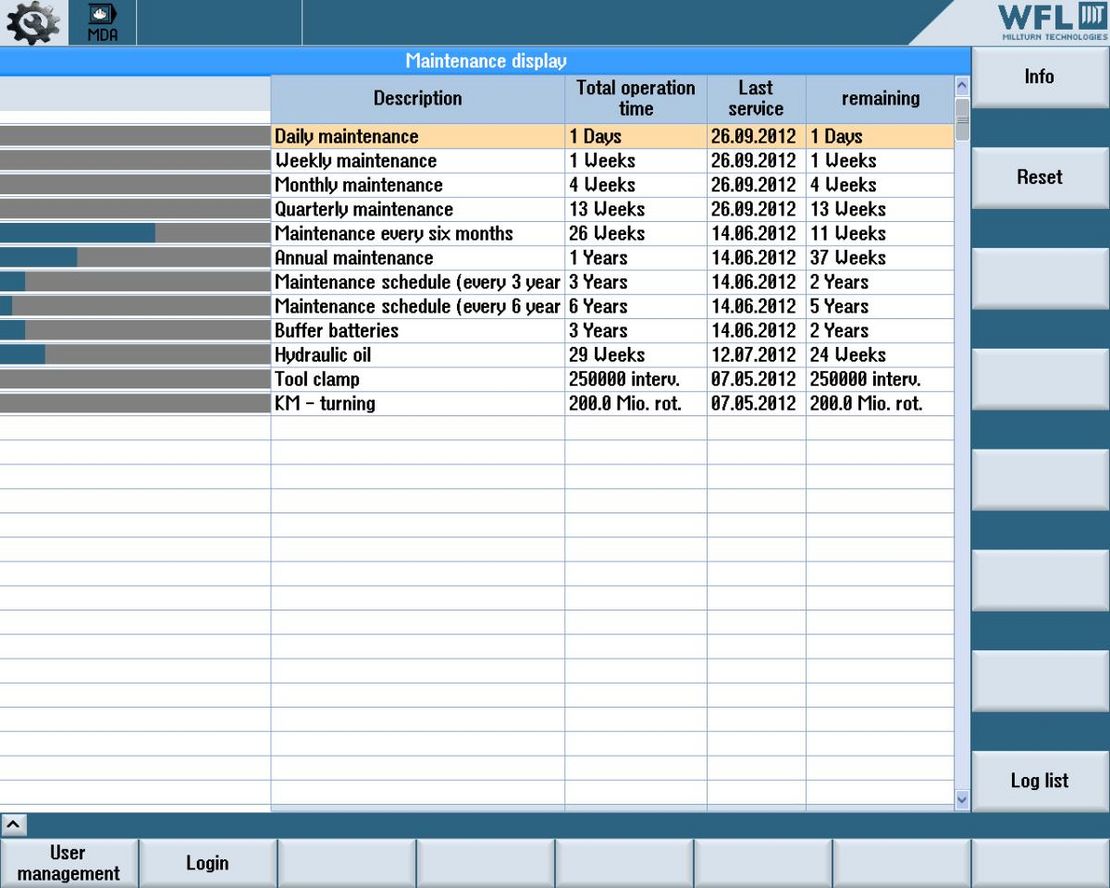
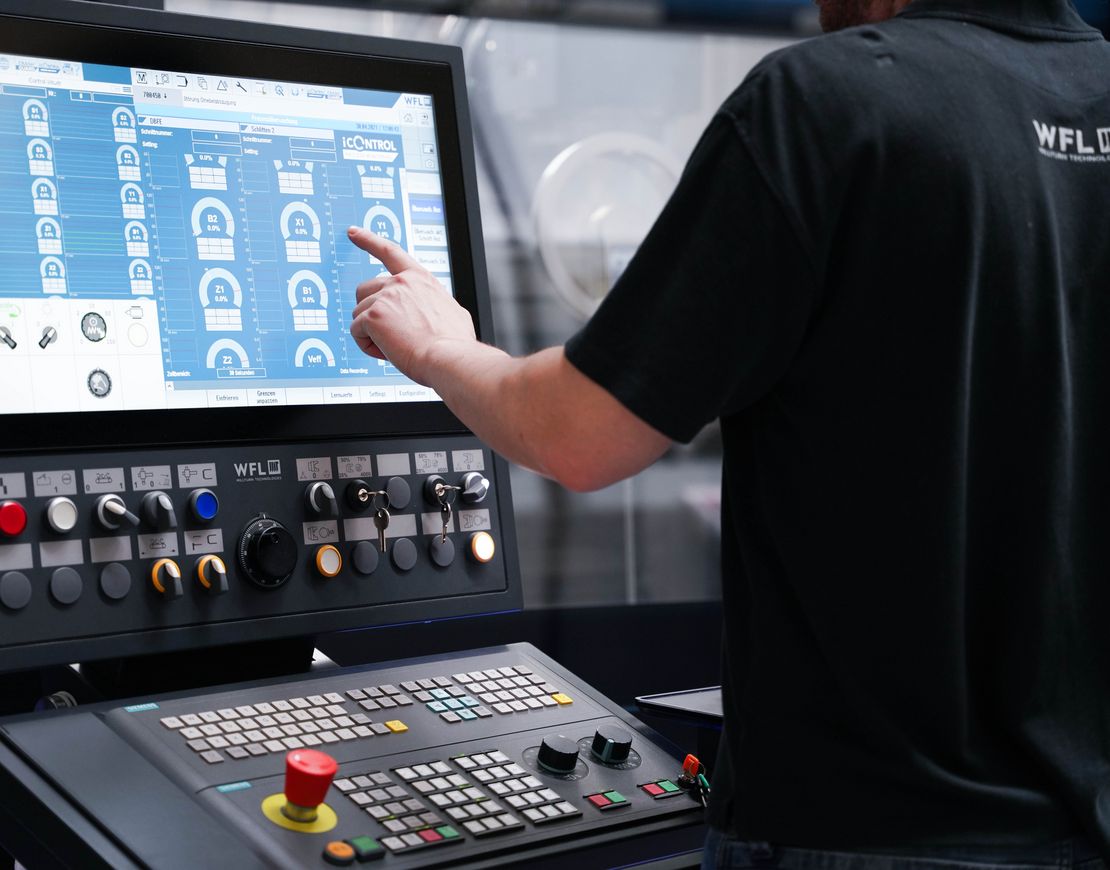
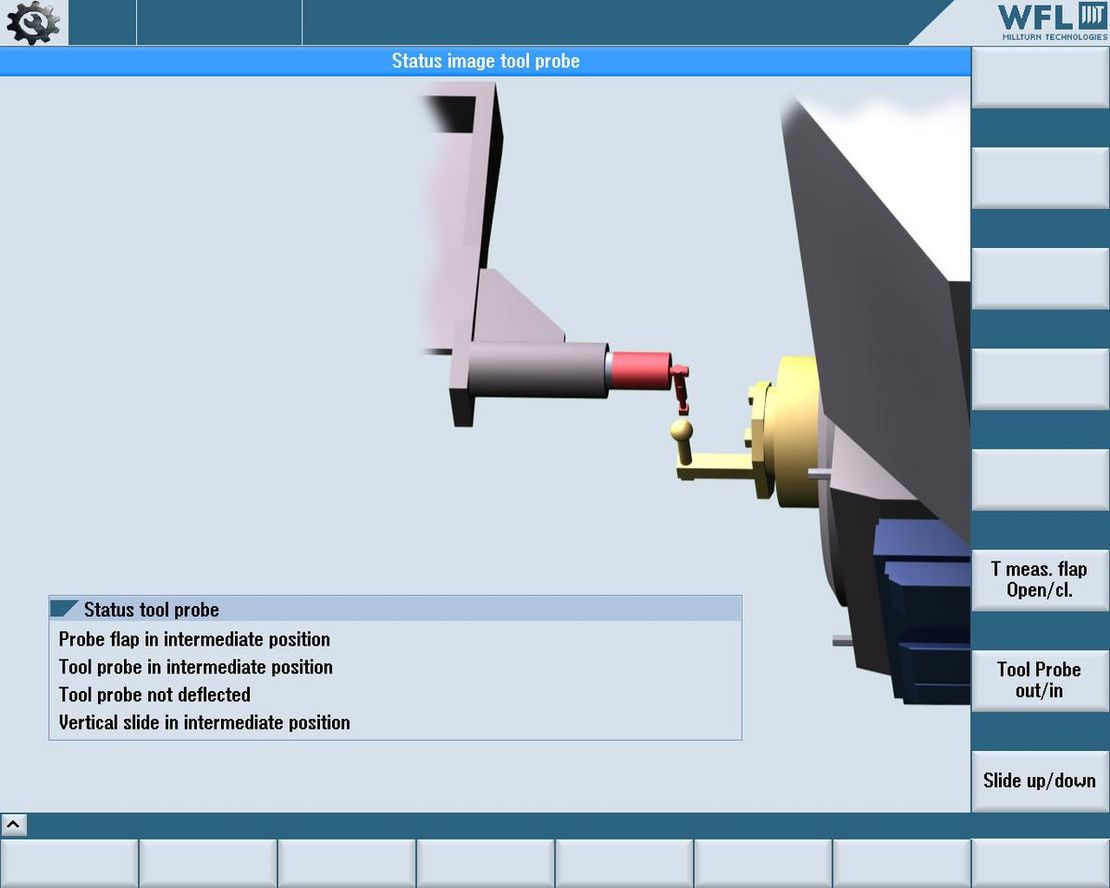
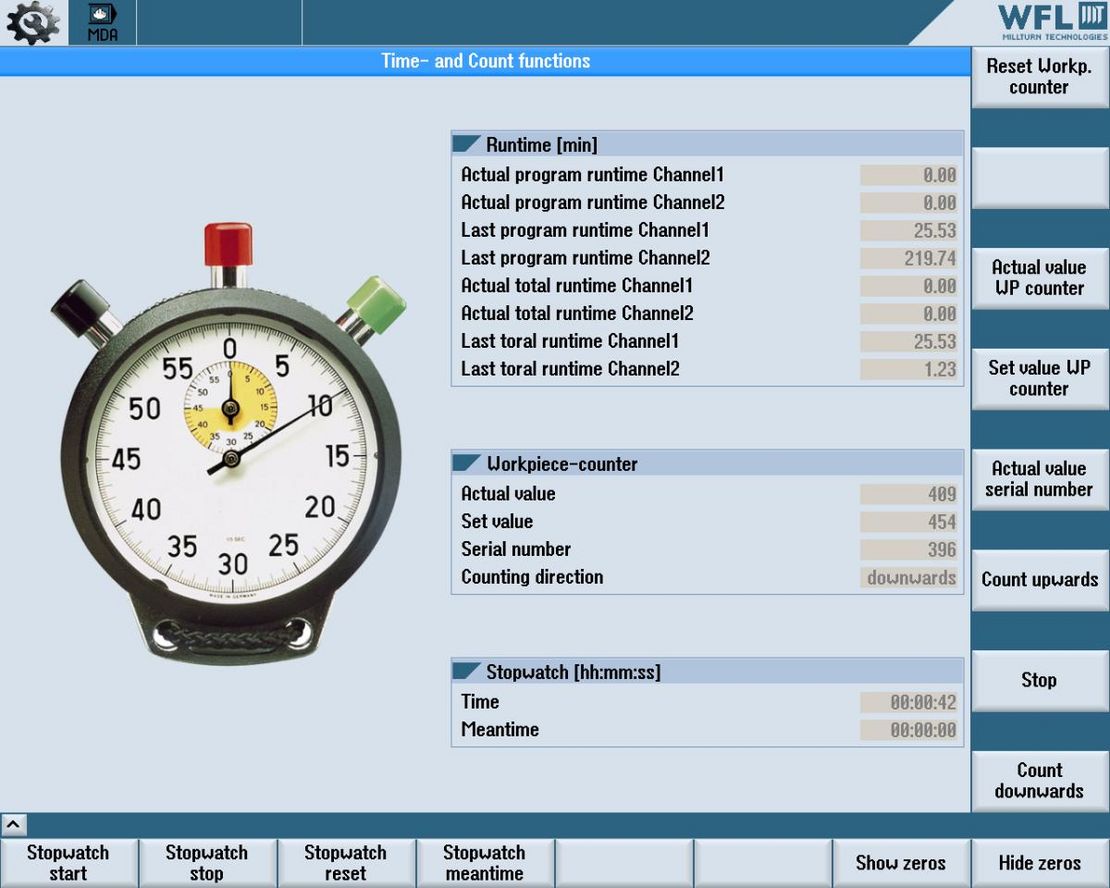
Process safety
The safety of the workpiece, tool and machine is a central objective in every machining process. Separate registration of all cutting force components in process monitoring ensures reliable detection of tool breakage, for example. The emergency retraction routines minimise the risk of rejection in the event of power outage.
- Drive-independent emergency retraction routines, level 1
- Drive-independent emergency retraction routines, level 2
- Control-led emergency retraction routines
- iControl Basic+
- iControl Advanced+
- Automatic display of input screens
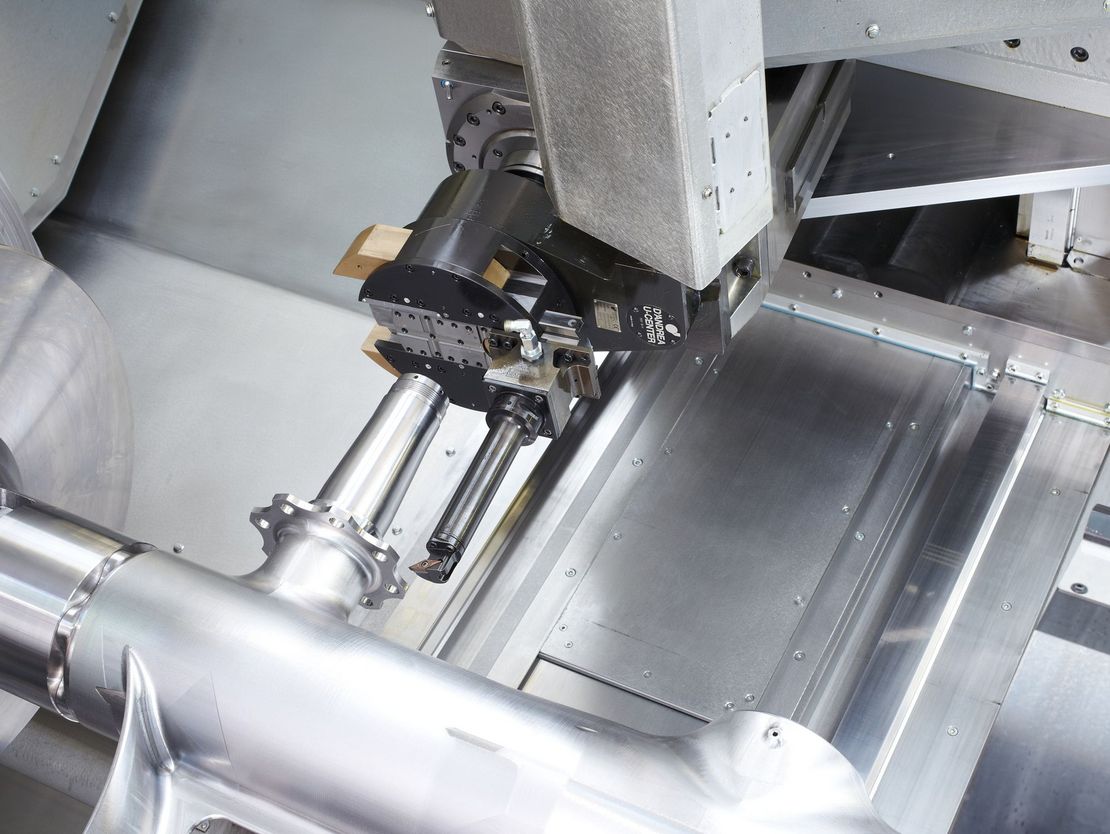
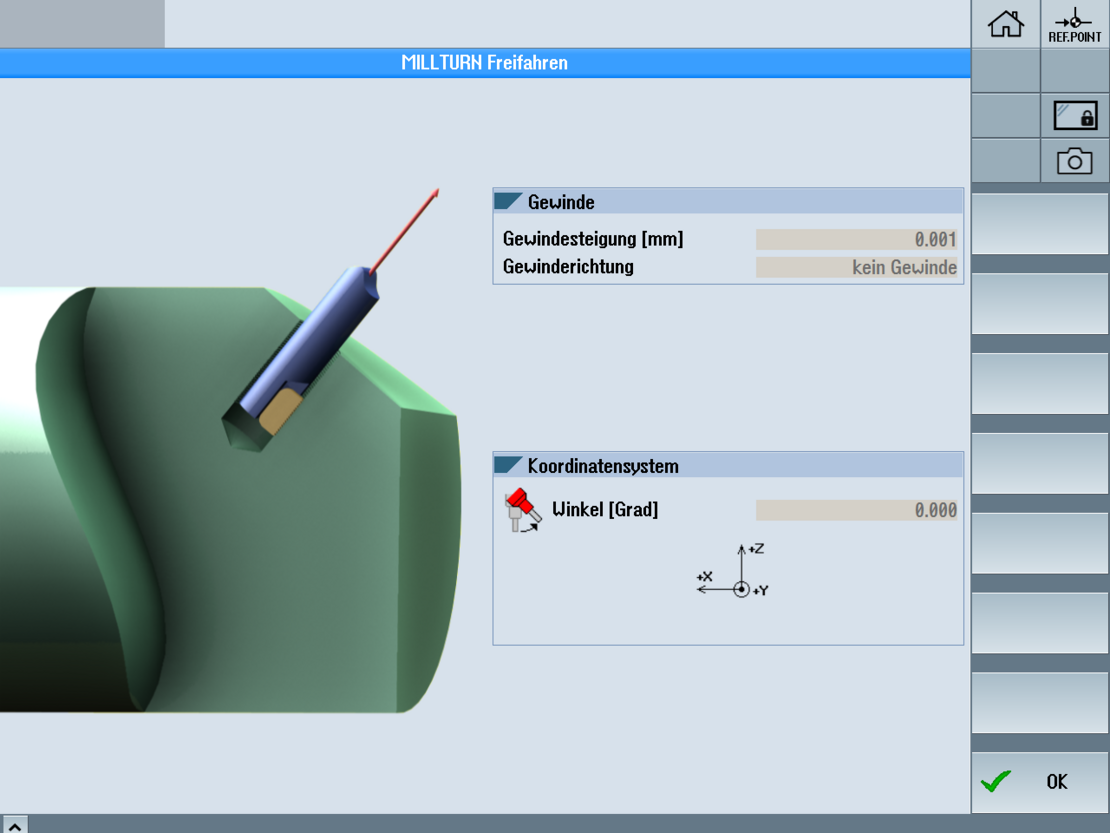
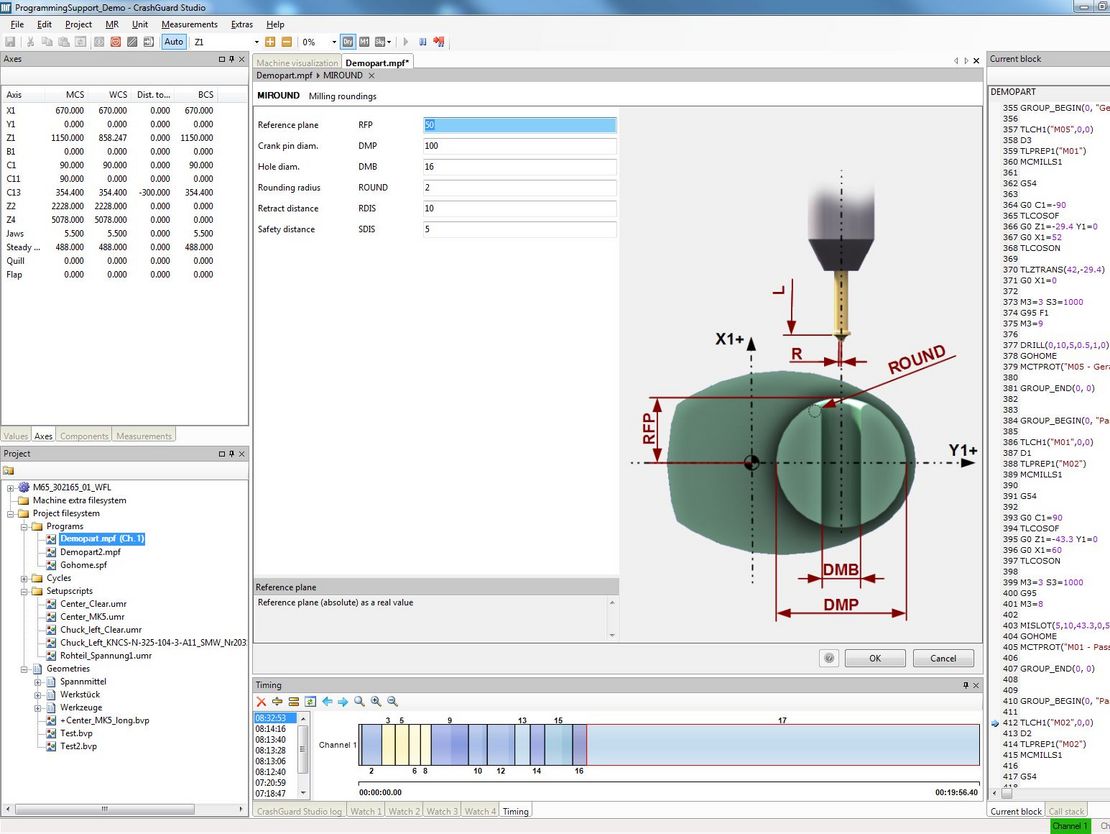
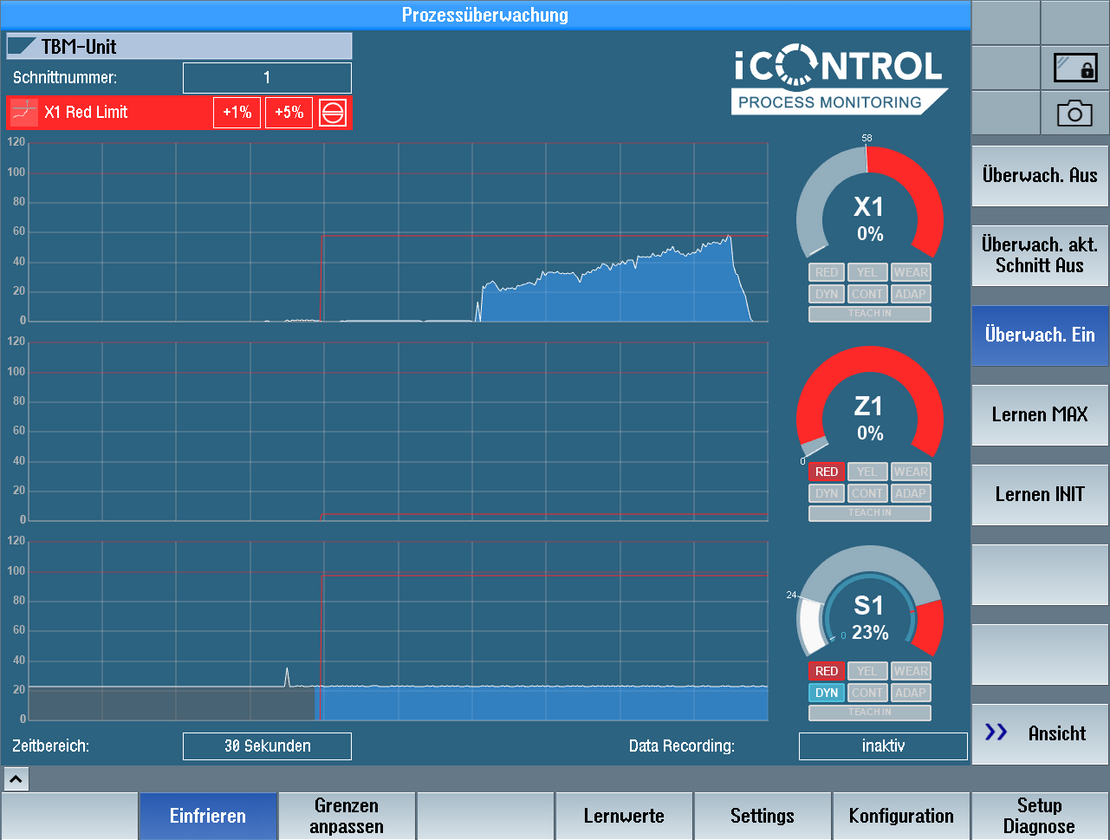