iControl
Process monitoring from WFL
WFL iControl protects your MILLTURN, even during autonomous production throughout the night.
Depending on the machine’s equipment, up to 16 freely configurable process signals are continuously monitored. The new design contains more complex and more intelligent monitoring options, offering comprehensive safety during production.
Multi-stage monitoring logics are used, which respond if the collision limit or adaptive process limit is exceeded, or if there are significant, rapid changes in force.
iControl Basic+ | iControl Advanced+ |
|
x | x | Emergency stop if collision limit is exceeded |
x | x | Display of the current axis loads and time sequence as well as automatic stop in the event of machine overload |
x | x | Two temperature sensors for recording the ambient temperature (machine bed) and the temperature in the milling spindle housing (in the area of the front spindle bearing) |
x | x | Black box: if the collision limit is exceeded, the black box creates a detailed log of the machine processes (target position, current drive torque, process signal) one second before and one second after the collision alarm |
x | Teach-in and monitoring modes with display of process limits | |
x | Milling spindle vibration sensor (incl. roller bearing parameter gSE) | |
x | Tool wear detection function and automatic stop if tool breakage is detected | |
| x | Function for detecting significant, rapid changes in force (dynamic monitoring) |
x | Tolerance band monitoring of the time sequence of the process signals (adaptive limits) | |
x | Integration of external sensors in process monitoring permitted, e.g. monitoring and recording of performance data from Silent Tools Plus or coolant pumps | |
x | Connection for Silent Tools Plus power supply |
Data recording
-
iControl Data Recording can be used to generate long-term process data logs. This option is particularly beneficial when manufacturing safety-relevant components.
- Greater process reliability thanks to continuous monitoring of machining operations
- Protects the machine against damage
- Increased productivity and workpiece quality
- Tool cost savings and better utilisation of the tool life due to wear monitoring
- Better utilisation of the machine as process signals are shown on the display
- Integration of sensored tools
- Maximum sensitivity thanks to teach-in technology
- Option to perform monitoring without teach-in cut
- Optimum monitoring of machining processes with different cutting depths thanks to adaptive limits
- Option for early detection of machine wear
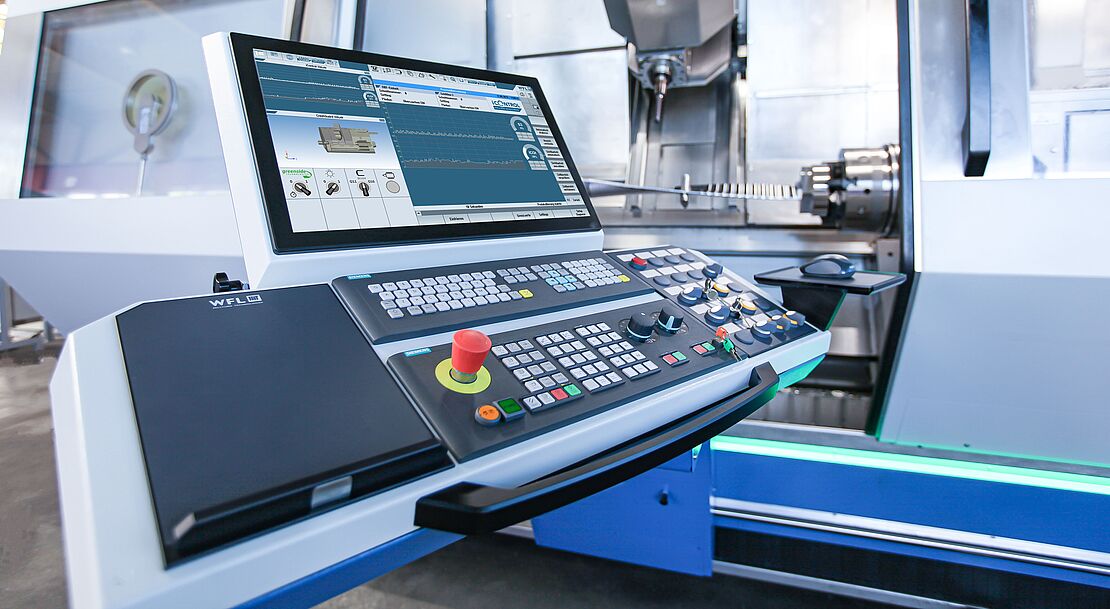
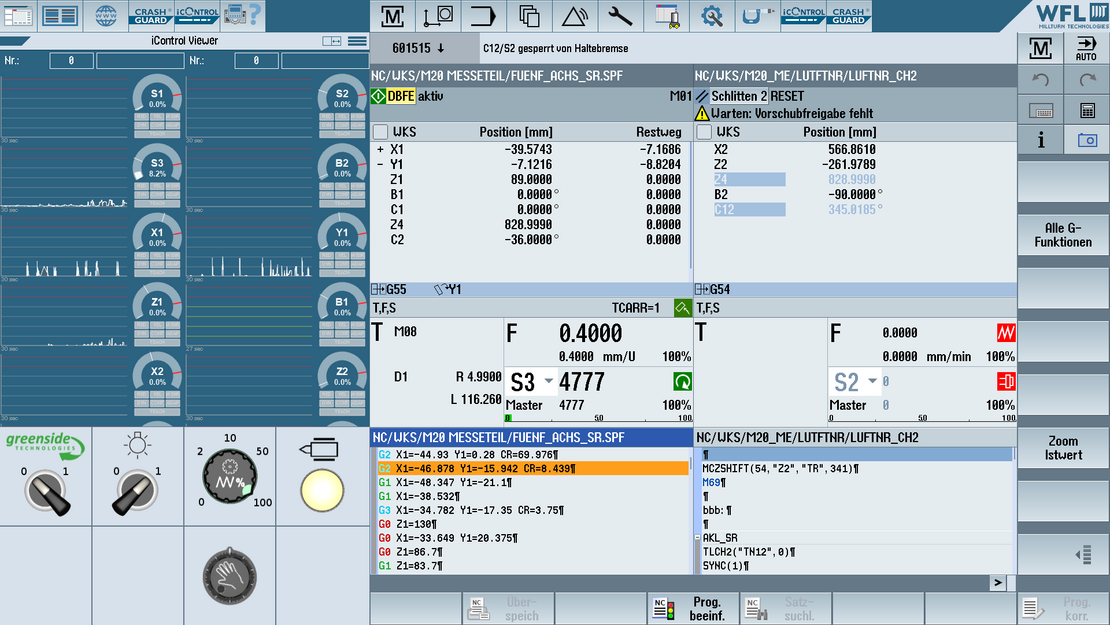
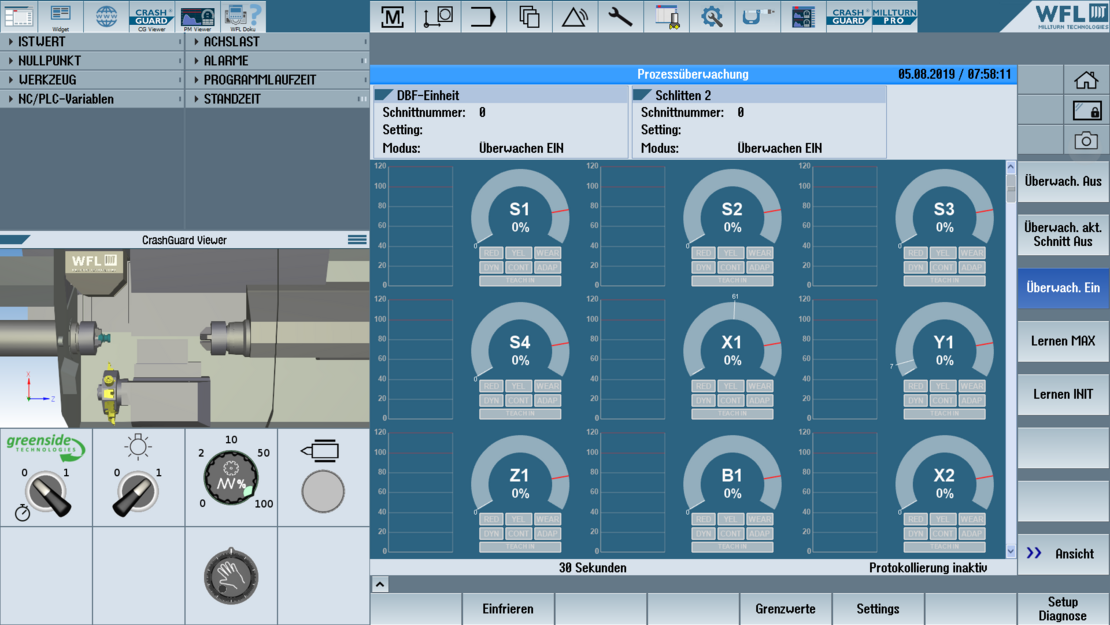
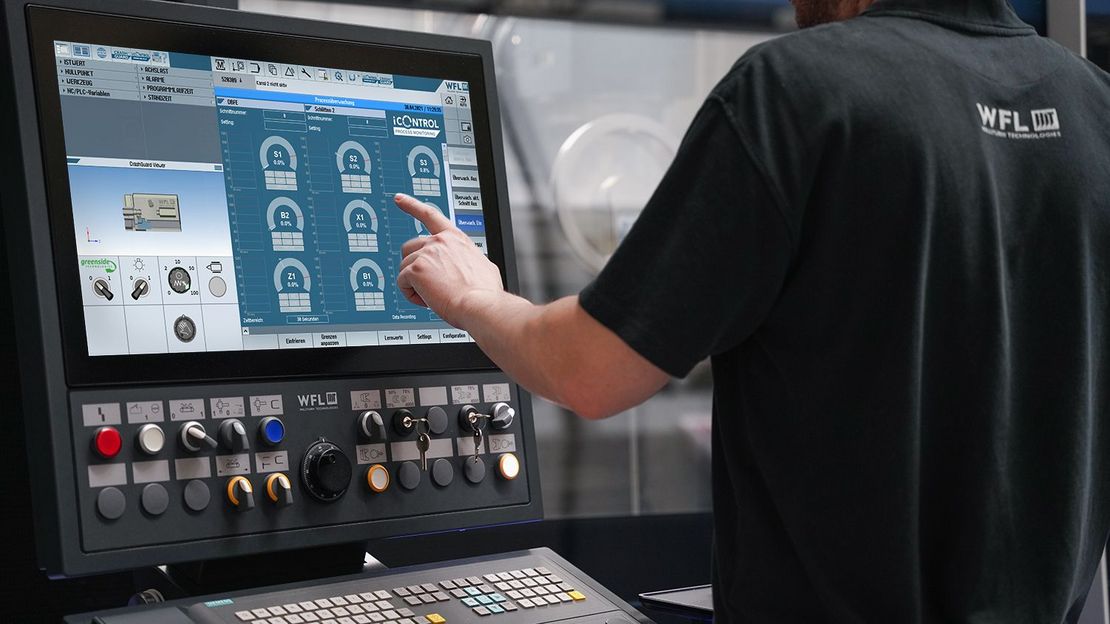
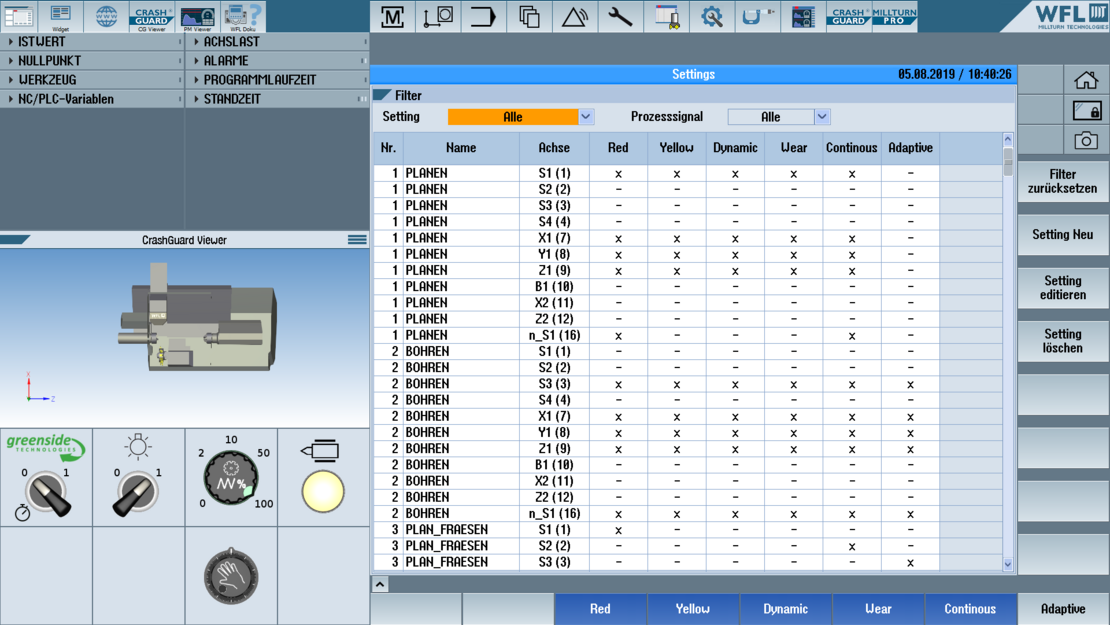
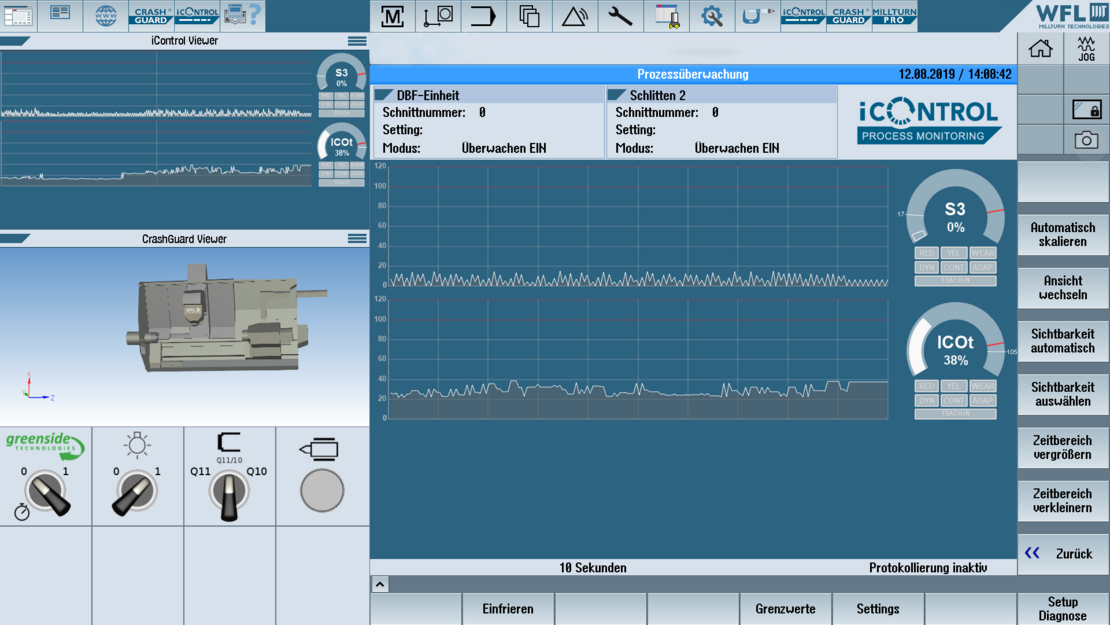