M65 MILLTURN
The multifunctional miracle
Anyone who wishes to stay ahead in the market must react quickly and in a flexible manner to their customers’ requirements. The components that customers require are becoming increasingly complex and therefore more demanding to manufacture. By combining all of the manufacturing steps in a multifunctional MILLTURN turning-boring-milling centre, the requirements of both current and future manufacturing jobs can be fulfilled with the highest level of precision. The possibility of freely interpolating the NC axes B, C, X, Y and Z offers the user an incomparable range of technologies. Complete machining without manual intervention, by means of turning, drilling, milling, deep hole drilling, internal and external gear cutting, turn-milling, circular milling and automatic workpiece measurement to enable compliance with the tightest of tolerances. Compensation of thermal influences is also provided for. Any geometric profile can be efficiently machined with the maximum level of precision. There are absolutely no limits when it comes to workpiece complexity.
Its multifunctionality is simply ingenious.
Highlights at a glance
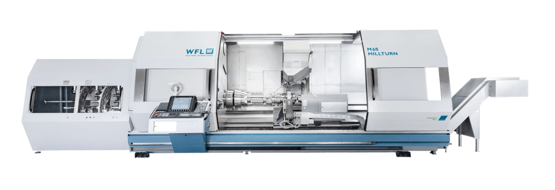
- Compact design of the bottom slides (favourable for short parts)
- Individual clamping solutions
- Automatic coolant docking
- Turning-boring-milling unit with integrated measuring probe
- Workpiece transfer
- Tool change in a position of your choice
M65 | ||
---|---|---|
Nominal center distancea | mm | 1000/2000/3000/4500 |
Swing - ø over Top slide | mm | 830 |
Max. Turning- ø between centers | mm | 830(760) |
Max. power, Turning spindle 100% duty cycle | kW | 40/60 |
Max. torque, Turning spindle 100% duty cycle | Nm | 2318/2748 |
Max. spindle speed, Turning spindle | min-1 | 2600/2600 |
Max. power, Miling spindle 100% duty cycle | kW | 30 |
Max. torque, Milling spindle 100% duty cycle | Nm | 315 |
Max. spindle speed, Milling spindle | min-1 | 6000 |
Swiveling angle B - axis | degree | -110...+90 |
Travel Y - axis | mm | 600(-200...+400) |
Travel Y - axis (option) | mm | - |
Travel X - axis | mm | 720(-20...+700) |
Tailstock | type | Mechatronic |
Tool magazine | number | 40/80/120 |
Control SIEMENS | type | SINUMERIK ONE |
The prismatic tool system
The interface for large tools
The prismatic tool interface enables the use of tools that exceed the maximum dimensions of standard tools. Thanks to the use of robust prismatic tool holders, boring bars, solid drills, angular heads and facing heads can be attached to the milling unit in a highly stable manner. If the WFL system boring bar is being used, the cutting heads can also be changed automatically. Two types of magazine are available to provide automatic handling of heavy internal machining tools.
Prismatic tool magazine
By expanding the disc magazine to include the appropriate tool holders, prismatic tools can also be stored alongside standard tools. In this case, the automatic handling of these tools is ensured by an additional tool changer.
Pick-up magazine
Prismatic tools can be stored in this additional magazine, which is positioned above the headstock. A further design variant of the pick-up magazine enables long tools to be stored using the standard tool interface.