Peak Technology – l’esprit d’innovation mène au sommet
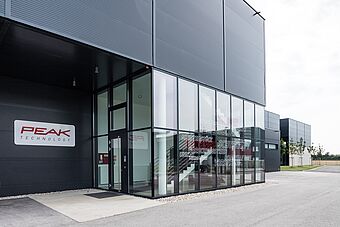
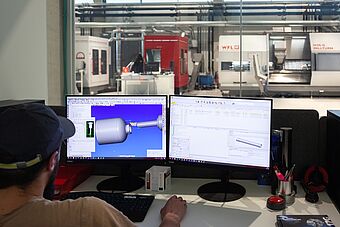
Parc d‘activité Holzhausen, c’est écrit sur une pancarte entre les champs et une petite route communale. Rien ici ne laisse présumer du potentiel en haute technologie qui nous attend dans le petit village proche de l’aéroport de Linz. Créée en 2007 par Dieter Grebner, la société Peak Technology fournit aux clients des secteurs de la Formule 1 ou de l’aéronautique des structures complexes et ultra-légères en composite et fibre de carbone.
Des sujets futuristes tels que l’avion électrique ou le vol autonome sont ici omniprésents. Les 120 employés de Peak fabriquent déjà les composants pour les avions du futur. Matthias Lechner, Directeur Technique, explique les projets visionnaires. Aujourd’hui, Peak Technology se penche sur ce à quoi ressemblera la mobilité aérienne dans 10 ou 20 ans. Mais Peak va encore bien plus loin : pour l’industrie spatiale l’entreprise produit des accumulateurs à haute pression, des boîtiers d'allumage et des composants structurels enveloppés de fibre de carbone. Les accumulateurs à haute pression ultra légers, pouvant supporter des pressions allant jusqu’à 700 bars font quasiment déjà partie du catalogue standard. Parmi tous ces projets futuristes, les composants périphériques des moteurs de Formule1, qui également figurent au Portfolio de Peak, feraient presque penser à des pièces pour une machine à vapeur. Malgré toutes les exigences de la haute technologie, on se considère comme une manufacture, car de nombreux procédés de la technologie des composites en fibres sont réalisés minutieusement à la main. Donc un artisanat traditionnel associé à une fabrication de haute technologie. Dans son atelier CN, Peak Technology mise depuis 2019 sur une M35-G MILLTURN de WFL.
Au cours des 3 dernières années, le souhait d’amélioration de l’atelier CN a été pris en compte. Avec l’acquisition d’une M35-G MILLTURN, le parc de machines ultra-moderne a récemment été complété afin de répondre aux exigences futures. Auparavant, on travaillait les pièces séparément sur des machines de tournage, puis de fraisage. „Nous voulions limiter les changements de posages au strict minimum et simplifier la planification de production. De plus, les niveaux de tolérance requis par nos clients étant très élevés, ils ne peuvent pour ainsi dire être atteints que par un usinage complet en un minimum de serrage“, reprend Matthias Lechner, Directeur Technique de Peak, pour résumer ces exigences. Au final, des surfaces de forme libre avec des tolérances de l'ordre de 0,005 mm doivent être maintenues de manière fiable. La climatisation de l’ensemble de l’atelier de production ainsi qu’une technique de mesure au plus haut niveau constituent la condition de base pour répondre à ces exigences. La taille des lots de chaque commande varie entre 10 et 30 pièces. Cependant, même pour une „série“ de 10, on fabrique d’abord une pièce unique, puis une autre la semaine suivante, car nos clients ne souhaitent pas recevoir toutes les pièces en même temps, mais chacune d’entre elle „just-in-time“, explique Lechner. Actuellement, nous fabriquons 10 à 15 pièces différentes sur la MILLTURN WFL. Et pratiquement chaque jour davantage. „Les matériaux à usiner sont à la fois des métaux tel que le titane, les aciers à haute résistance et l’aluminium, ou des composants en fibre de carbone, explique Christian Brunner, responsable d’équipe usinage. Lui-même aurait déclaré un jour face à une pièce compliquée : „Si nous avions une MILLTURN, ce serait tellement plus simple“.
Pour la société en pleine expansion, le moment s’est présenté en 2018. „Nous avons étudié tous les acteurs du marché dans les différentes usines. Ce que nous avons particulièrement apprécié dans la MILLTURN de WFL, c’est la conception du banc incliné sur une base solide en fonte. Donc une machine très rigide. Enfin, la proximité avec le fabriquant était pour nous également un facteur important. De nombreuses sociétés internationales travaillent par l’intermédiaire de distributeurs. Cela n’était pas envisageable pour nous“ se souvient Matthias Lechner.
« Comme nous travaillons beaucoup avec de très petits outils, la vitesse de rotation à 16.000 tr/min pour la broche de fraisage était très importante. L‘option standard de 12.000 tr/min n’aurait pas été suffisante. C'était une bonne chose que WFL ait depuis un certain temps déjà une variante de cette broche mécanique à 16.000 tr/min en cours de test et qu’elle fonctionne déjà avec succès chez un client. En fait, le volume et la performance ne sont pas notre priorité. Il nous faut plutôt une grande vitesse de rotation combinée à une stabilité et une précision élevées », s’accordent à dire Brunner et Lechner. Spécialement pour des composants à très faibles rayons, on utilise des fraises sphériques minuscules. Les pièces sont serrées par un mandrin de serrage 3 mors avec changement rapide, même si nous utilisons actuellement pour des essais un système de serrage Hainbuch. Parfois les pièces sont également serrées de l‘intérieur par la contre-pointe. Lorsque les pièces sont serrées dans le mandrin, les pressions de serrage sont librement programmables et peuvent être modifiées par petits paliers en une seule opération de serrage sous contrôle CN. La modification de la force de serrage, commandée par programme, est également possible sans ouvrir le mandrin. Ceci est nécessaire pour les pièces à paroi fines. « Nous apprenons chaque jour un peu plus, et bien que nous ayons plutôt une bonne maîtrise du fraisage 5 axes, la MILLTURN nous fait régulièrement découvrir de nouvelles possibilités, avec lesquelles nous devons peu à peu nous familiariser. Il s’agit simplement d’une autre dimension de complexité. Le fraisage 5 axes est utilisé en permanence sur la MILLTURN. Cela fonctionne parfaitement et on obtient des résultats précis. Nous en sommes très satisfaits. En complément du tournage, du fraisage et du perçage, le taillage d’engrenages sera bientôt également réalisé avec la WFL », indique le directeur technique pour résumer les expériences sur la nouvelle machine.
Au préalable, WFL a dû résoudre une problématique technique de logiciel : Avec Form-Inspect de M&H, le réglage entre le point zéro dans le Système FAO et celui de la position réelle dans la machine devait s’effectuer automatiquement. La pièce brute à usiner est mesurée dans l’espace à l’aide de palpeurs. Grâce à cette information, le point zéro de l'usinage peut être corrigé à la position réelle de la pièce brute directement sur la commande à l'aide d'une solution logicielle spéciale. Si par exemple, la position ou la forme de la pièce brute ne correspond pas parfaitement à la CAO, la position idéale est déterminée au moyen d'un calcul « best-fit », le système de coordonnées du programme CN est décalé ou réorienté dans la position idéale et une surépaisseur constante sur toute la pièce brute est assurée. Cela permet de garantir que des surépaisseurs et des conditions de coupe constantes soient maintenues tout au long du processus d‘usinage. Le système a été étudié en étroite coopération entre WFL et M&H et testé en profondeur chez WFL. Il était pleinement fonctionnel immédiatement après la livraison de la machine.
Pour le système d’attachement porte-outils sur la M35-G MILLTURN, Peak a opté pour le Capto C6. Là encore le facteur stabilité était déterminant. « Nous avons discuté avec différents spécialistes du secteur et en avons conclu que Capto répondait parfaitement à nos exigences », déclare Mathias Lechner pour relater les analyses faites avant l’investissement. Les outils sont réglés sur un appareil de préréglage et les données de l’outil transcrites sur une puce directement sur l’outil. Au chargement de l’outil, ses données sont automatiquement envoyées dans la commande numérique et stockées dans le logiciel de gestion d’outils. Avec une capacité de 120 places, le magasin dispose d’un espace de stockage suffisant. Peak souhaite à long terme maintenir l’ensemble des outils dans la machine pour servir toutes les commandes. Avec sa capacité actuelle, le magasin de la M35-G MILLTURN, dispose de suffisamment de réserves pour des outils frères.
Lorsqu’on parle de précision, Peak n'accepte aucun compromis. La machine dispose de règles optiques sur tous les axes linéaires. Précision avant tout. Même si la machine remplissait déjà à la réception tous les critères de tolérance, Peak souhaitait encore plus de précision. Durant cette réception, les spécialistes de WFL se sont donc encore penchés sur la machine pour en extraire les tout derniers µ.
Pour l’usinage de la fibre de carbone, la machine a été équipée d‘un système d’aspiration spécifique. Celui-ci est muni d’un commutateur qui permet de choisir entre aspiration de brouillard d‘huile et poussière de carbone.
Peak est également à la pointe en matière de connectivité. Toutes les machines de la production ont été mises en réseau avec le système ERP (PGI – Progiciel de gestion intégré, en français) et transfèrent en temps réel les temps de fonctionnement et les temps d'arrêt des machines. De plus Peak, utilise également le système MindSphere IoT de Siemens (IdO - Internet des objets, en français). Celui-ci permet à WFL, sur demande de Peak, d’analyser les données des capteurs, comme la température de l’unité de fraisage et, le cas échéant, d’anticiper les futures demandes de service.
La programmation s’effectue par système CAO/FAO Hypermill. Les directives claires de Peak indiquent que toutes les machines CN doivent être programmables par système FAO. Des pièces complexes demandent un travail de programmation de deux à trois jours. Les pièces plus élémentaires peuvent être réalisées en quelques heures seulement. Pour la simulation en amont du processus d'usinage, on utilise également la solution logicielle CrashGuard Studio de WFL qui permet de simuler plus particulièrement le transfert de la pièce à la contre-broche, ce qui n'est pas encore possible sur le système CAO/FAO.
Afin de protéger la machine, les précieuses pièces ainsi que les outils, Peak utilise le logiciel WFL anti-collisions CrashGuard. « C’est tout simplement nécessaire pour répondre à nos exigences », indiquent unanimes les experts de la production chez Peak. « Si nous parvenons à éviter une collision, l’investissement sera amorti ».