Usinage intégral de pièces pour des transmissions automobiles
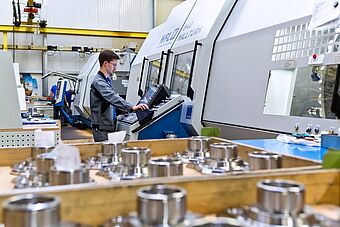
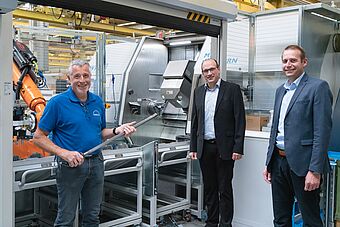
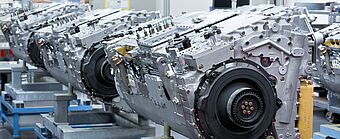
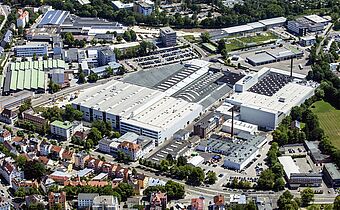
Pour mettre en mouvement des véhicules blindés, des forces motrices élevées sont nécessaires. Pour cela, les transmissions de l’entreprise Renk GmbH, sise à Augsbourg, apportent la propulsion nécessaire. En effet, l’entreprise Renk est considérée comme la spécialiste des transmissions entièrement automatiques pour les véhicules militaires lourds à chenilles. Et quand une performance optimale est demandée, les solutions de production de WFL ne sont pas loin. Mais chaque chose en son temps...
Contrairement aux automobiles, un véhicule lourd à chenilles est propulsé, dirigé et même freiné par la transmission. Cette dernière action, dans le cas des véhicules équipés par Renk, s’effectue grâce à l’action combinée de deux systèmes de freinage différents pour vitesses faibles et élevées à l’aide d’un frein mécanique (lorsque la vitesse est faible) et d’un frein hydrodynamique intégré à courants de Foucault, qu’on appelle un ralentisseur. En raison de ses fonctions de passage de vitesses, de direction et de freinage, la transmission constitue la centrale de mobilité de ces véhicules et joue donc un rôle essentiel. Elle est installée sur des colosses qui pèsent jusqu’à 70 tonnes, roulent au maximum à 72 km/h et qui doivent être mobiles aussi bien sur route que hors-piste. En fournissant plus de 40 armées dans le monde entier, Renk peut se targuer d’être le leader du marché mondial pour l’équipement de transmissions de véhicules militaires à chenilles d’un poids supérieur à 40 tonnes. Chaque transmission est conçue pour un type spécifique de véhicules et adaptée à l’équipement et à la motorisation correspondants. En fonction du type de transmission de base, il y a donc une adaptation individuelle à l’utilisation spécifique du véhicule. La direction du véhicule s’effectue au niveau de la transmission intermédiaire latérale en influant sur les vitesses de sortie, puis directement au niveau du barbotin de la chenille. Le sens de conduite peut donc seulement être modifié en créant un différentiel de vitesse de rotation entre les chenilles. En cas de modification identique de la vitesse de rotation de chaque chenille, le véhicule freine ou accélère. En cas de vitesse de rotation différente des chenilles, un mouvement de direction a lieu et en cas d’entraînement des chenilles en sens inverse l’une de l’autre, cela entraîne une rotation du véhicule autour de son propre axe. La transmission doit pouvoir effectuer tout cela et résister sur la durée à des forces impressionnantes, et ce sous toutes les conditions imaginables. Il n’est pas surprenant que cela implique une multitude de pièces de fabrication complexes avec des exigences de qualité élevées.
Les pièces nécessaires aux transmissions sont répartis sur trois segments de fabrication : les pièces du boîtier, les petites pièces cubiques (pièces à réception de force, boîtiers à soupapes, pièces du frein et pièces de mécanique des fluides) et les pièces rotatives à dentures pour la transmission de la vitesse de rotation. Ces dernières sont des pièces typiques qui sont montées dans la chaîne de traction de la transmission et il s’agit également de pièces qui sont parfaitement adaptées à un usinage intégral sur les machines Millturn de WFL. Dans ce segment, il n’existe à vrai dire aucune pièce qui ne nécessite qu’un simple tournage. Outre le tournage, on rencontre typiquement des géométries complexes fraisées ainsi qu’un grand nombre de perçages. Les principales matières utilisées sont des aciers à haute résistance de 1 200-1 300 N/mm2 sous forme de barres et pièces forgées. « Tout ce qui est rond et présente une denture peut aller sur une machine de WFL », voici la devise générale. « Généralement, nous fabriquons en petite série des lots de 1-300 pièces, et la taille moyenne d’un lot est d’environ 50 pièces », explique Martin Wimmer, le responsable de la fabrication. Mais il n’est pas rare non plus d’avoir des pièces pour des transmissions prototypes en lots de 1 à 5 pièces. Grâce à la flexibilité des multitalents WFL, aucune fabrication de prototype avec des processus de fabrication différents n’est nécessaire. Les plus petits lots peuvent tout à fait être fabriqués de manière économique via le parc de machines existant. En outre, cela évite de recourir à des dispositifs de serrage spécifiques et coûteux, car la Millturn effectue l’usinage des pièces via des mâchoires standard et quelques mâchoires spécifiques dans le mandrin à trois mâchoires.
La programmation représente un facteur décisif pour la productivité des machines. Celle-ci a lieu uniquement via le système de programmation CFAO Siemens NX. « Pour les quatre premières machines WFL, nous avions différents post-processeurs en raison des différents modèles de machines. Désormais, les PP sont tellement standardisés, que toutes les machines fonctionnent via un seul PP. L’avantage est que la planification de la fabrication peut, dans un premier temps, avoir lieu indépendamment de la machine. Cela signifie qu’un programme est créé sans savoir sur quelle machine il sera finalement utilisé pour la fabrication. Ce n’est que lorsque la commande est lancée que le département de logistique de production décide sur quelle machine les différentes pièces sont fabriquées », explique M. Wimmer. L’intégralité de la simulation de la fabrication s’effectue par CFAO. Ici, la continuité des données, de la construction des pièces jusqu’à la fabrication sur la machine, joue un rôle important. Un modèle de la machine, des mandrins de serrage, des mâchoires de serrage, des pièces brutes et finies ainsi que des outils sont enregistrés dans le système de FAO. La simulation reflète ainsi très bien la réalité et de tels programmes testés fonctionnent aussi sans problème en pratique. « Cela nous convient très bien. Grâce à la simulation en continu, nous n’avons quasiment plus de collisions », explique M. Wimmer. Le taillage de dentures constitue toutefois une exception en matière de simulation. Les Millturn peuvent tailler des dentures jusqu’au module 4. Des cycles WFL spéciaux sont principalement utilisés pour le taillage avec fraise-mère, car ils peuvent être utilisés rapidement et simplement en saisissant les paramètres de denture.
La première Millturn de WFL a déjà été livrée en 2010, et depuis chez Renk, on s’intéresse fortement à l’usinage intégral. « À l’époque, nous avons analysé toute notre gamme de pièces, des très petites pièces jusqu’à celles d’un diamètre d’env. 600 mm, et avions l’objectif d’harmoniser le parc de machines existant très hétérogène. Pour toute la gamme de pièces, nous voulions un concept de machines structuré de la même manière pour plusieurs tailles. Pour cela, la WFL était structurée de manière optimale de la M35 à la M50. Outre le tournage, perçage et fraisage sur une machine, le taillage de dentures, en particulier du module 3 en qualité 8 avec une fraise-mère serrée de façon flottante, revêtait pour nous une grande importance. Plusieurs fabricants avaient confirmé pouvoir le faire, mais seule WFL l’a finalement prouvé. L’indexage d’axe B extrêmement stable, avec son grand taillage de dentures Hirth, fait en particulier bonne impression. La structure caractéristique de la tête de tournage-perçage-fraisage WFL, où la broche de fraisage est conçue comme broche de transmission à couple élevé, garantit des performances d’usinage très élevées dans toutes les plages de vitesse de rotation. Le châssis de machine extrêmement stable a non seulement fait ses preuves en matière de productivité, mais permet en outre le respect continu de tolérances géométriques très précises et l’obtention de qualités de surface optimales », résume M. Wimmer en évoquant les multiples aspects techniques. Il explique avec précision les autres avantages : « Les machines sont équipées d’une installation de liquide d’arrosage haute pression de 80 bar, et une commutation vers l’air est également possible. Outre le système d’outils Capto C6 standard, toutes les machines sont équipées d’un logement d’outil particulièrement stable au niveau de la tête de tournage-perçage-fraisage. Un attachement prismatique actionné de manière hydraulique permet de loger de manière particulièrement stable des barres d’alésage lourdes ou des outils spéciaux lourds. Pour les machines d’un entre-pointes de 3000 mm, outre le magasin standard, un magasin Pick-Up pour l’utilisation automatique de barres d’alésage longues a été intégré. « Pour les travaux spéciaux individuels, nous ne voulons plus avoir à utiliser d’autres machines ou des fournisseurs externes », explique M. Wimmer. « Cela réduit fortement le temps d’exécution, mais aussi le nombre de phases de travail. Grâce à l’usinage intégral, certains plans de travail ont été réduits de moitié. L’usinage combiné nous permet également de réduire le temps d’usinage. La capacité libérée grâce à une utilisation plus efficace est utilisée pour des travaux supplémentaires sur la machine. Par exemple, si une bavure apparaît lors de l’usinage, l’ébavurage est directement effectué sur la machine. Cela améliore non seulement la productivité mais aussi la sécurité au travail et minimise le risque de blessures. La formation pour les utilisateurs de WFL a été particulièrement utile dans ce contexte. Elle a permis de former le personnel de manière intensive à la programmation, mais également à la planification conceptuelle de tout l’usinage ainsi qu’à la sélection des moyens de serrage. Depuis, dans tout le département des transmissions automobiles, nous utilisons neuf Milliturn de WFL dans trois tailles différentes et deux longueurs de tournage différentes. »
Pour accroître encore l’efficacité et augmenter le degré d’utilisation, la dernière M35 livrée (2017) a été équipée d’une solution d’automatisation de FRAI Robotic. Celle-ci est par exemple utilisée pour augmenter l’efficacité des pignons planétaires. Entre temps, une M40 a également été automatisée. « Nous arrivons à l’adapter de manière optimale à nos exigences ainsi qu’à notre application et notre situation spatiale. Nous avons obtenu exactement ce que nous voulions. Sur la deuxième installation, nous souhaitons également intégrer une station de retournement, afin que les employés puissent se concentrer sur les tâches exigeantes », se réjouit M. Wimmer à propos du résultat de l’investissement.
En matière de service après-vente, l’entreprise Renk est particulièrement bien préparée, avec sa propre équipe de maintenance, et effectue les réparations de petite à moyenne ampleur sur place. « Au tout départ, nous avons dû apprendre qu’un changement d’outil peut se faire dans toute position longitudinale, et qu’une pièce à usiner peut donc parfois bloquer le chemin. Mais tout ça, c’est du passé », plaisante M. Wimmer en évoquant leurs premières expériences.
Actuellement, le sujet de l’enregistrement des données machine prend de plus en plus d’importance chez Renk. Pour cela, un système Cockpit est déjà utilisé et affiche l’état actuel de la machine : comme l’utilisation en continu est cruciale pour plusieurs pièces, une solution indépendante du fabricant de machines est utilisée ici. Et, à l’instar de la CFAO, une étroite collaboration a ici lieu avec Siemens. Pour la Predictive Maintenance et le Condition Monitoring, Renk dispose déjà d’expériences optimales et de propres solutions : le monitoring Renk, déjà éprouvé pour les transmissions Renk, a été adapté aux machines-outils et constitue la base de ce thème d’avenir important.