Más eficiencia en Orbit
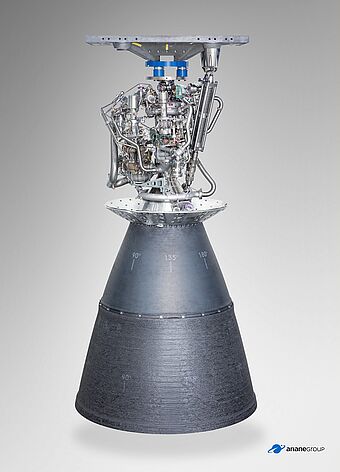
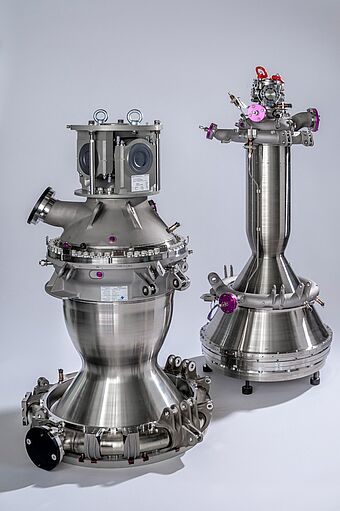
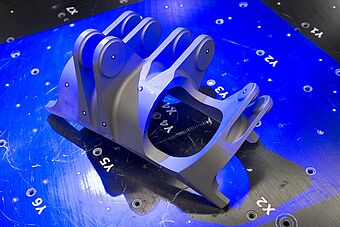
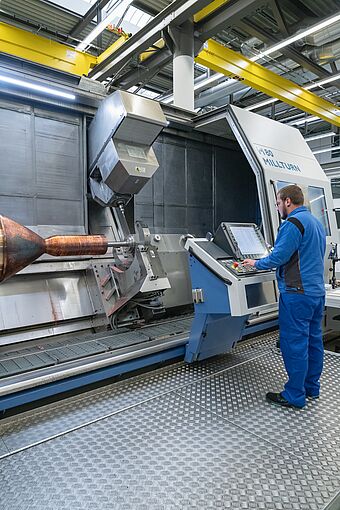
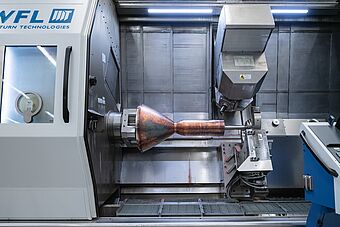
ArianeGroup es un líder mundial en el transporte espacial que sirve tanto a clientes institucionales como comerciales, garantizando la independencia estratégica de Europa en el espacio.
Como contratista principal de las lanzaderas europeas Ariane 5 y Ariane 6, ArianeGroup es responsable de toda la cadena de producción de las lanzaderas, desde el diseño y la fabricación completa hasta la comercialización y las operaciones a través de su filial Arianespace. ArianeGroup emplea a unas 7.000 personas altamente cualificadas en Francia y Alemania y es una empresa conjunta propiedad de Airbus y Safran a partes iguales. La empresa es también el principal contratista de las lanzaderas balísticas de la Marina francesa. ArianeGroup y sus filiales son especialistas mundialmente reconocidos en equipos y propulsión espacial, servicios y vigilancia espacial. Su experiencia también se aplica en otras industrias e infraestructuras críticas.
-
7.000 Trabajadores en Alemania y Francia
-
11 Filiales y participaciones mayoritarias
-
50/50 Empresa formada por Airbus y Safran
-
3,1 Millones de € de volumen de negocio en 2021
Uno de los lugares más importantes de ArianeGroup es Ottobrunn, cerca de Múnich. Aquí se encuentra un centro de competencia de ArianeGroup para la propulsión líquida, donde se desarrollan y producen componentes para los motores de los vehículos de lanzamiento europeos Ariane. Actualmente, la atención se centra en las cámaras de empuje para el motor de la etapa principal de Ariane 6, Vulcain 2.1, así como para el nuevo motor de la etapa superior reencendido Vinci.
Un vistazo al mundo de los viajes espaciales
Stefan Winter, director de producción en Ottobrunn, ofrece información durante una visita a la producción: "En Ottobrunn somos algo menos de 300 empleados. De ellos, unos 100 empleados trabajan en la producción. Como tenemos todos los procesos de fabricación de nuestros componentes en la empresa, nuestro plazo de entrega es muy corto. La mayoría de los procesos se combinan en nuestro centro de producción, desde el mecanizado y la soldadura (EB y WIG) hasta la integración y las pruebas de calidad. En los edificios vecinos se encuentran los departamentos de galvanización y limpieza de componentes. Las distancias cortas son una gran ventaja para nosotros".
Para dejar atrás la Tierra y su atracción gravitatoria, un cohete necesita mucha energía. En el caso de la lanzadera Ariane, esto lo hacen primero los propulsores sólidos con un empuje de unos 13.000 kilo Newton, que levantan el cohete de aproximadamente 800 toneladas del suelo en los dos primeros minutos después del lanzamiento. La etapa principal con el motor Vulcain 2, que es la primera que se lanza tras la cuenta atrás, sigue proporcionando empuje hasta que el cohete ha alcanzado una altitud de unos 160 kilómetros unos nueve minutos después del lanzamiento. En el espacio, la etapa superior toma el relevo, impulsada por el motor HM7B en Ariane 5 y Vinci en Ariane 6. Dependiendo de la misión, este motor está en funcionamiento durante unos 15 minutos para colocar la etapa superior con los satélites en el espacio en la órbita correcta.
La cámara de empuje del motor Vinci del Ariane 6 se desarrolla y fabrica en Ottobrunn. La cámara de empuje se considera el "corazón" del motor.
Vinci trabaja con hidrógeno criogénico y oxígeno como ciclo expansivo: "Primero, el hidrógeno fluye alrededor de la cámara de combustión, la enfría y se evapora. Los gases resultantes se utilizan como medio de impulsión para las bombas de combustible y, a continuación, se introducen en la cámara de combustión junto con el oxígeno a través del cabezal de inyección y se queman", explica el director de producción Stefan Winter. "Este motor, llamado de ciclo expansivo, es el único de su clase en el mundo con este rendimiento. Mientras que los motores criogénicos convencionales requieren casi siempre un generador de gas para accionar las turbobombas, este proceso funciona de forma diferente en la cámara de combustión de Vinci. En el motor de ciclo expansivo, también dejamos pasar el hidrógeno por los canales de refrigeración para enfriar la cámara, pero el ingenioso diseño lo mantiene en la cámara durante mucho tiempo para que se caliente lo máximo posible. A continuación, utilizamos el gas en expansión para impulsar las turbobombas. Esa es la gran ventaja del motor Vinci".
M80 Millturn fabrica el motor Vinci
La mayoría de las piezas del motor de Ottobrunn se fabrican en una máquina WFL M80. Estas piezas también incluyen el cuerpo base de la cámara de combustión del motor. En el primer paso, se prepara el cuerpo básico para girar el contorno interior. A continuación, se realiza el torneado y el fresado del contorno exterior. Estas dos operaciones solían realizarse en dos máquinas.
Con la M80 Millturn, ahora se combinan ambos procesos -torneado y fresado- y se garantiza una sujeción estable. Esto es una gran ventaja, especialmente para las piezas con un diseño largo y delgado, como la cámara de combustión Vinci. Además, el sistema de sujeción de punto cero garantiza la máxima flexibilidad en la producción. "Eso es algo estupendo", subraya Winter.
Una aleación especial se utiliza como material para el cuerpo base del motor Vinci. La aleación patentada de cobre-plata-circonio se caracteriza por su alta resistencia y su buen valor de transferencia de calor con muy buena maquinabilidad. Esto es especialmente relevante para la cámara Vinci. Debido al ya mencionado diseño largo y delgado, las propiedades del material son muy importantes aquí. El material se funde primero en bloques y luego se forja en la forma deseada. La calidad se garantiza mediante ultrasonidos y, a continuación, se libera para la producción.
Tras la entrega de la pieza en bruto, las principales etapas de la producción de una cámara de combustión Vinci son el torneado, el fresado, la galvanización, la soldadura y, por último, el acabado. El 80% de la carga de trabajo se realiza con el M80.
Además, también se están realizando pruebas de corte para el futuro en la M80. La construcción estable y la buena cinemática dan más posibilidades aquí de lo que se pensaba. Ya se han realizado las primeras pruebas con materiales de corte cerámicos en la M80 Millturn. A medio plazo, este proceso se calificará en la máquina WFL para el Inconel y el níquel. "Estoy seguro de que podemos conseguirlo con la máquina WFL", afirma Winter.
Espíritu innovador en tecnología y personal
Sin embargo, no son sólo los componentes de Vinci los que se fabrican actualmente en el Millturn. El equipo de producción también utiliza la máquina para la producción de piezas satélite, en desarrollo y para la construcción de accesorios. "Así, la máquina se aprovecha perfectamente de la mezcla", añade Stefan Winter. "También soy partidario de los temas de desarrollo, porque sin duda es la carga de trabajo del mañana y siempre tenemos que afrontar nuevos retos. En este momento, por ejemplo, estamos trabajando en componentes para los accionamientos del futuro: Prometheus, por ejemplo".
Las diferentes versiones de los motores Prometheus funcionarán con hidrógeno líquido y oxígeno líquido, y con oxígeno líquido y metano. Serán los primeros motores europeos con control de combustión, pudiendo el motor adaptarse a las condiciones de vuelo del vehículo de lanzamiento durante las diferentes fases de la misión. Un sistema digital proporcionará un control en un rango del 30 al 100% del empuje máximo. Además, Prometheus estará dotado, en particular, de inteligencia artificial y de un sistema de supervisión que permitirá diagnosticar el funcionamiento del motor en cualquier momento.
La familia de demostradores Prometheus también se beneficia en gran medida de las últimas tecnologías de impresión 3D. Los componentes fabricados con esta tecnología representan el 70% del peso total del motor.
"Podemos utilizar la WFL muy bien para todos estos emocionantes proyectos futuros", dice Stefan Winter. Para poder realizar todo esto, se necesita un equipo motivado de ingenieros y trabajadores cualificados. Sobre todo, se necesitan empleados buenos y concienzudos en máquinas tan complejas como la WFL. Cuando una operación de acabado por valor de más de medio millón está funcionando en la máquina, la tensión es evidente para el personal. Es difícil encontrar buen personal, así que siempre buscamos buenos trabajadores cualificados", afirma Winter.
"Para mí, como director de producción, es especialmente importante hacer que el lugar de trabajo sea interesante para los empleados. Mientras tanto, en la producción de Ottobrunn trabajan principalmente maestros y técnicos. Los buenos trabajadores cualificados están deseosos de aprender y deben ser desafiados y promovidos en consecuencia. Por ello, intentamos que los trabajos sean lo más interesantes posible. Por este motivo, estamos ampliando la programación con un sistema de programación adicional. Nuestro objetivo a medio plazo será que un grupo de personal cualificado se asigne a una máquina y la ejecute de forma independiente desde la programación hasta la producción del componente. A continuación, aplicaremos esta rotación de trabajos en otras máquinas. En los próximos 5 años, me gustaría convertir la producción en esto. Para ello, necesitamos personal comprometido y cualificado", Winter está convencido de ello.
Además, subraya: "Aquí trabajamos con materiales extremadamente caros, de acuerdo con las normas industriales más exigentes y con los requisitos de calidad más elevados. No hay un segundo intento de lanzar un cohete, así que no podemos permitirnos ningún error. El personal altamente cualificado es absolutamente esencial aquí, y eso lo tenemos".
La pregunta Millturn
"En términos de tiempos de mecanizado, la inversión de la WFL M80 Millturn / 3000 mm aportó un enorme valor añadido", explica Stefan Winter. La WFL sustituyó a un torno de 3 ejes y a una fresadora de 3 ejes. En la M80 se ha implementado un sistema de amarre de punto cero, por lo que el montaje es sólo una parte del trabajo. De este modo, los tiempos de producción y los tiempos de inactividad se redujeron en al menos un 30%. "Una gran ventaja de la máquina WFL es también el gran almacén de herramientas. Debido al mecanizado de Inconel, siempre tenemos entre cuatro y seis herramientas hermanas en uso, lo que requiere suficientes puestos de herramientas. Gracias al concepto modular del cargador, este requisito se cumple. Si necesitas más herramientas, sólo tienes que comprar otro disco de herramientas. ¡Eso es genial! En el pasado, se necesitaban tres programas NC y más para tres procesos. Ahora sólo tenemos un programa NC que liberar y mantener para el mismo trabajo. También es un alivio importante para la gestión de la configuración, ya que aquí hay que gestionar menos datos. Fue un gran paso adelante", dice Winter con entusiasmo.
A la pregunta de por qué se tomó la decisión de comprar un Millturn o el modelo M80, Winter responde lo siguiente: "La cinemática y las referencias de la máquina acabaron por convencernos de comprarla. También dimos importancia a un rápido suministro de piezas de repuesto, a los fabricantes conocidos de los componentes instalados y a la proximidad al fabricante.
La máquina está equipada con un almacén de recogida y una barra de perforación del sistema WFL. "En colaboración con WFL y Sandvik, hemos adquirido una barra de perforación especial de 1,4 m de longitud para poder mecanizar el contorno interior de Vinci en la WFL en el futuro". Winter informa además: "Para poder voltear el contorno interior en la WFL, también hemos desarrollado un nuevo accesorio, que ya está terminado".
Los requisitos de la máquina también eran la fiabilidad y la precisión. "La máquina tiene que gestionar la tolerancia de aproximadamente 1/100 en el rango de trabajo requerido. Ese es nuestro requisito. La influencia de la temperatura juega un papel importante en este caso. Por eso nuestra sala de producción también está climatizada. Por ello, revisamos e inspeccionamos la máquina con regularidad, y también se controla su temperatura. La tecnología de WFL es muy buena en este sentido", afirma el director de producción Winter.
Con el ciclo de software Utronix -el eje U virtual- se producen superficies de sellado en ArianeGroup. Esto se debe a que las superficies circulares son necesarias en determinadas piezas y en todos los ángulos. "A unos 135 grados, tenemos que mecanizar circularmente una superficie de sellado de 28 mm alrededor de un agujero de 20 con una barra de perforación. Esto se hace cada vez más grande. Por eso, el ciclo Utronix lo utilizamos con bastante frecuencia y es muy importante", describe Winter el mecanizado con detalle.
El jefe de producción también destaca la ventaja de la nueva máquina con el ejemplo de la producción de un demostrador de boquillas: "Nos pidieron que construyéramos un demostrador de boquillas. El reto consistía en producir un complejo contorno interior cónico con canales de refrigeración. Sólo la estabilidad de la máquina hizo posible el proceso de brochado con una longitud de casi 500 mm. La combinación de estabilidad, flexibilidad y el espacio de trabajo necesario en la máquina facilitan la adopción y aplicación de estos temas especiales".