Mecanizado completo de piezas para cajas de cambios de vehículos
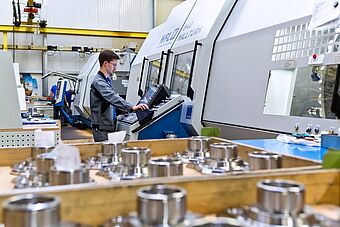
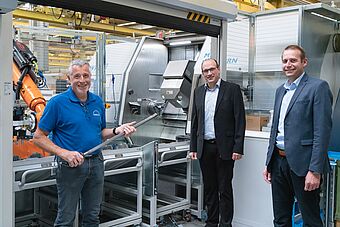
Se necesitan grandes fuerzas de accionamiento para poner en movimiento los vehículos blindados. En este caso, los reductores de Renk GmbH, con sede en Augsburgo, proporcionan la propulsión correspondiente. Al fin y al cabo, Renk está considerado el especialista en transmisiones totalmente automáticas para vehículos militares pesados de oruga. Y cuando se requiere el máximo rendimiento, las soluciones de fabricación de WFL no están lejos. Pero vayamos paso a paso...
A diferencia de lo que ocurre en el sector de la automoción, un vehículo pesado sobre orugas se conduce, dirige e incluso frena con la transmisión. En el caso de los vehículos equipados por Renk, esto último se consigue gracias a la interacción de dos sistemas de frenado diferentes para velocidades bajas y altas, mediante un freno mecánico en la gama de velocidades más baja y un freno hidrodinámico de corrientes de Foucault incorporado, el llamado ralentizador. La transmisión, con sus funciones de cambio, dirección y frenado, es el centro de la movilidad de estos vehículos y, por tanto, desempeña un papel vital en su supervivencia. Y esto es así en el caso de los colosos que pesan hasta 70 toneladas, se desplazan a una velocidad máxima de 72 km/h y, al mismo tiempo, tienen que tener una gran movilidad en carretera o en terreno abierto. Habiendo suministrado a más de 40 ejércitos en todo el mundo, Renk puede reclamar el título de líder del mercado mundial en el equipamiento de vehículos militares de oruga de 40 toneladas o más con caja de cambios. Cada caja de cambios se diseña para un tipo de vehículo específico y se adapta a su respectivo equipamiento y motorización. Es decir, partiendo del correspondiente tipo de caja de cambios básica, se produce la adaptación individual a la aplicación individual en el vehículo. La dirección del vehículo se realiza influyendo en las velocidades de salida a través del engranaje de reducción lateral, y luego directamente en el tambor de la rueda dentada de la cadena. Por lo tanto, sólo se puede influir en el sentido de la marcha variando las velocidades en las cadenas. Si la velocidad cambia en la misma dirección, el vehículo frena o acelera. Si la velocidad varía, se produce un movimiento de dirección y si la salida es en sentido contrario, el resultado es una rotación del vehículo alrededor de su propio eje vertical. La caja de cambios tiene que hacer frente a todo esto y soportar las enormes fuerzas, incluso en todas las condiciones imaginables, a largo plazo. No es de extrañar que esto implique un gran número de piezas de fabricación complejas con altos requisitos de calidad.
Los componentes necesarios para las cajas de cambios se dividen en tres segmentos de producción: Se trata de piezas de la carcasa, pequeñas piezas cúbicas (piezas de absorción de potencia, bloques de válvulas, piezas del freno y componentes fluídicos) y piezas rotativas con engranajes para la transmisión de la velocidad. Estas últimas son las piezas típicas que se instalan en el tren de potencia de la transmisión y también son las piezas que se adaptan especialmente bien al mecanizado completo en las máquinas Millturn de WFL. En realidad, no hay ninguna pieza en este segmento que sólo tenga un mecanizado de torneado puro. Además del torneado, suele haber geometrías complejas y fresadas, así como un gran número de perforaciones. Los materiales utilizados son principalmente aceros de alta resistencia con una fuerza de 1200-1300 N/mm2 como barra y piezas forjadas. "Todo lo que es redondo y tiene dientes va en una máquina WFL", es el credo general. "Normalmente, la producción se realiza en lotes pequeños con tamaños de lote de 1 a 300 piezas, siendo el tamaño medio del lote de unas 50 piezas", explica el jefe de producción, Martin Wimmer. Pero tampoco son infrecuentes las piezas para prototipos de cajas de cambios en lotes de 1 a 5 piezas. Gracias a la flexibilidad de WFL, no es necesario producir un prototipo por separado con procesos de fabricación diferentes. Incluso los lotes más pequeños pueden funcionar de forma muy económica con la maquinaria existente. Además, esto elimina la necesidad de costosos dispositivos de sujeción especiales, ya que la pieza de trabajo se sujeta mediante mordazas estándar y algunas especiales en un mandril de tres mordazas.
Un factor decisivo para la productividad de las máquinas es la programación. Esto se hace exclusivamente a través del sistema CAD-CAM de Siemens NX. "En los cuatro primeros WFL, también tuvimos diferentes postprocesadores debido a los distintos modelos de máquinas. Mientras tanto, los PP se han normalizado para que todas las máquinas funcionen a través de un único PP. La ventaja es que la planificación de la producción puede realizarse inicialmente de forma independiente a la máquina. Esto significa que se crea un programa sin saber en qué máquina se producirá finalmente. Sólo cuando se ha iniciado el pedido, la logística de producción decide en qué máquina se fabricarán las respectivas piezas", explica Wimmer. La simulación completa de la producción se realiza en CAD-CAM. Aquí, la coherencia de los datos desde el diseño de los componentes hasta la producción en la máquina desempeña un papel importante. En el propio CAM se almacena un modelo de la máquina, los mandriles, las mordazas, las piezas brutas y acabadas, así como las herramientas. Esto significa que la simulación reproduce muy bien la realidad y que los programas probados de este modo también funcionan sin problemas en la práctica. "Nos llevamos muy bien con él. Gracias a la simulación continua, prácticamente no tenemos más colisiones", resume Wimmer. Las marchas son una cierta excepción a la simulación. El tallado de engranajes se realiza en las fresadoras hasta el módulo 4. Aquí se utilizan principalmente los ciclos WFL especiales para el tallado de engranajes, ya que pueden aplicarse de forma muy sencilla y rápida introduciendo los parámetros de tallado.
El primer Millturn de WFL se entregó en 2010 y, desde entonces, Renk se ha dedicado intensamente al mecanizado completo. "En aquel momento, analizamos toda nuestra gama de piezas, desde las muy pequeñas hasta las de aproximadamente 600 mm de diámetro, y perseguimos el objetivo de estandarizar el parque de máquinas existente, muy poco homogéneo. Queríamos un concepto de máquina para toda la gama de piezas que tuviera una construcción idéntica en los diferentes tamaños. WFL, desde el M35 hasta el M50, era simplemente la mejor opción. Además del torneado, el taladrado y el fresado en una sola máquina, el tallado de engranajes, especialmente desde el módulo 3 hasta la calidad 8 con una fresa en voladizo, era importante para nosotros. Varios fabricantes lo prometieron, pero al final sólo WFL lo demostró. En particular, la indexación extremadamente estable del eje B con el gran dentado Hirth tiene un efecto positivo. El diseño típico de WFL de la unidad de torneado-fresado, en el que el husillo de fresado está diseñado como un husillo de engranaje de alto par, garantiza un rendimiento de corte extremadamente alto en todos los rangos de velocidad. El bastidor de la máquina, extremadamente estable, no sólo vale la pena en términos de productividad, sino que, en última instancia, permite mantener permanentemente las tolerancias geométricas más estrictas y lograr calidades de superficie óptimas", dice Wimmer, resumiendo los diversos antecedentes técnicos y explicando vívidamente las demás ventajas: "Las máquinas están equipadas con un sistema de refrigerante de alta presión de 80 bares, por lo que también es posible cambiar al aire. Además del sistema de herramientas estándar Capto C6, todas las máquinas están equipadas con un portaherramientas adicional especialmente estable en la unidad de taladrado-fresado rotativo. Las barras de mandrinar pesadas o las herramientas especiales pesadas pueden recogerse de forma extremadamente estable mediante un dispositivo de cola de milano de accionamiento hidráulico. Además del almacén estándar, en las máquinas con una anchura central de 3.000 mm se ha integrado un almacén de recogida para el uso automático de barras de perforación largas. "Ya no queremos depender de otras máquinas o de proveedores externos para trabajos especiales individuales", explica Wimmer. "Esto da lugar a una reducción especialmente elevada del tiempo de producción, pero también a una reducción significativa del número de operaciones. Los horarios de trabajo individuales se han reducido a la mitad gracias al mecanizado completo. Sin embargo, el mecanizado combinado también supone un ahorro en el tiempo de funcionamiento. La capacidad liberada por un uso más eficiente se utiliza para trabajos adicionales en la máquina. Por ejemplo, cuando se produce una gran rebaba durante el mecanizado, el desbarbado se realiza inmediatamente en la máquina. Esto no sólo mejora la productividad, sino también la seguridad laboral y minimiza el riesgo de lesiones. La formación de usuarios de WFL fue especialmente útil en este contexto. Además de la programación, se ilustró intensamente la planificación conceptual de toda la secuencia de mecanizado, así como la selección de los dispositivos de sujeción. Ahora operamos nueve tornos WFL en tres tamaños y dos longitudes de torneado diferentes en el área de productos de transmisión de vehículos".
Para mejorar aún más la eficiencia y aumentar el grado de utilización, la última M35 entregada (2017) se equipó con una solución de automatización de FRAI Robotic Solutions. Se utiliza para aumentar la eficacia de las ruedas planetarias, por ejemplo. Mientras tanto, también se ha automatizado una M40. "Conseguimos que se adapte perfectamente a nuestras necesidades y a nuestra situación de aplicación y espacio. Tenemos exactamente lo que queríamos. Para el segundo sistema, queremos integrar otra estación para que los empleados puedan concentrarse en el trabajo exigente", dice Wimmer, satisfecho con el resultado de la inversión.
En lo que respecta al servicio, Renk está especialmente bien posicionado con su propio equipo de mantenimiento y lleva a cabo reparaciones pequeñas y medianas en la propia empresa. "Sólo al principio tuvimos que aprender que un cambio de herramienta puede tener lugar en cualquier posición longitudinal y que a veces una pieza se interpone. Pero eso ya no es un problema desde hace mucho tiempo", bromea Wimmer sobre sus experiencias iniciales.
En la actualidad, el tema de la adquisición de datos de las máquinas también está cobrando cada vez más protagonismo en Renk. Para ello ya se utiliza un sistema en el que se muestra el estado respectivo de la máquina a través de una cabina. Dado que el objetivo es un uso coherente en varias plantas, la empresa confía en una solución independiente del fabricante de la máquina. Y al igual que con el CAD-CAM, existe una estrecha colaboración con Siemens. Renk ya tiene una excelente experiencia y sus propias soluciones para el mantenimiento predictivo y la supervisión de la condición: La monitorización de Renk, que también ha sido probada en los reductores de Renk, ya ha sido adaptada a las máquinas herramienta y constituye la base de este importante tema de futuro.