Effizienter in den Orbit
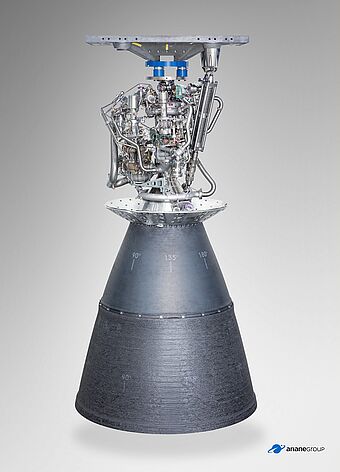
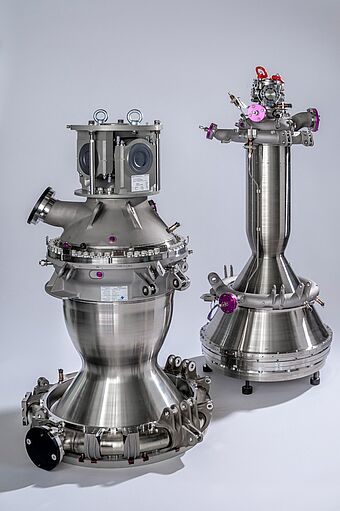
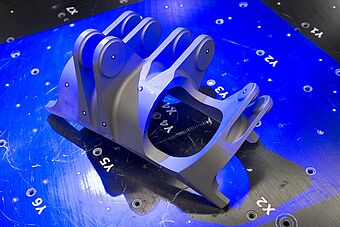
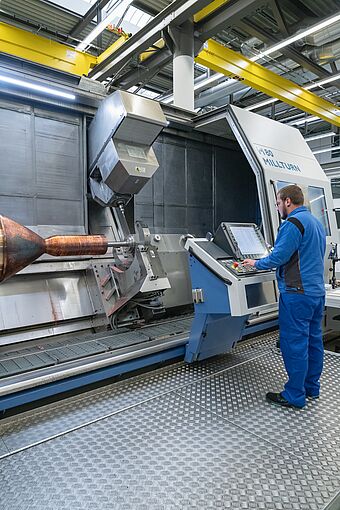
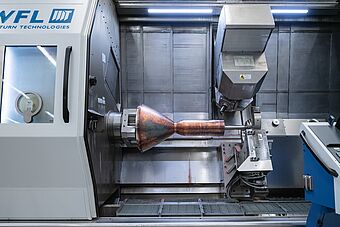
Die ArianeGroup ist ein weltweit führendes Unternehmen auf dem Gebiet des Raumtransports im Dienste institutioneller wie kommerzieller Kunden und gewährleistet dabei Europas strategische Unabhängigkeit im All.
Als Hauptauftragnehmer der europäischen Trägerraketen Ariane 5 und Ariane 6 ist die ArianeGroup für die gesamte Produktionskette der Träger verantwortlich – vom Entwurf über die vollständige Fertigung bis hin zur Vermarktung und Betrieb über ihr Tochterunternehmen Arianespace. ArianeGroup beschäftigt ca. 7000 hochqualifizierte Mitarbeiter in Frankreich und Deutschland und ist ein zu gleichen Teilen von Airbus und Safran gehaltenes Joint Venture. Das Unternehmen ist zudem Hauptauftragnehmer für die ballistischen Trägerraketen der französischen Marine. ArianeGroup und die Tochterunternehmen sind weltweit anerkannte Spezialisten für Raumfahrtausrüstungen und -antriebe, Services und Weltraumüberwachung. Ihr Know-how findet auch in anderen Industriezweigen und in der kritischen Infrastruktur Anwendung.
-
7.000 Mitarbeiter in Deutschland und Frankreich
-
11 Tochterunternehmen und Mehrheitsbeteiligungen
-
50/50 Joint-Venture von Airbus und Safran
-
EUR 3,1 Mrd. erzielte der Konzern 2021 an Umsatz
Zu den wichtigsten Standorten der ArianeGroup zählt Ottobrunn bei München. Hier befindet sich ein ArianeGroup-Kompetenzzentrum für Flüssigkeitsantriebe, in welchem Komponenten für Triebwerke der europäischen Ariane-Trägerraketen entwickelt und produziert werden. Zurzeit liegt der Schwerpunkt auf den Schubkammern für das Hauptstufentriebwerk der Ariane 6, Vulcain 2.1 sowie für das neue wiederzündbare Oberstufentriebwerk Vinci.
Ein Blick in die Welt der Raumfahrt
Stefan Winter, Fertigungsleiter in Ottobrunn, gibt beim Rundgang durch die Produktion informative Einblicke: „In Ottobrunn sind wir knapp 300 Mitarbeiter. Davon sind etwa 100 Mitarbeiter in der Produktion tätig. Dadurch, dass wir alle Prozesse für die Herstellung unserer Komponenten im Haus haben, ist unsere Durchlaufzeit sehr kurz. In unserem Produktionszentrum sind die meisten Prozesse vereint, von spanabhebender Fertigung und Schweißen (EB und WIG) über die Integration bis zur Qualitätsprüfung. In benachbarten Gebäuden finden Sie die Galvanik und die Bauteile-Reinigung. Die kurzen Wege sind ein großer Vorteil für uns.“
Um die Erde und ihre Anziehung hinter sich zu lassen, braucht eine Rakete viel Energie. Das erledigen bei der Ariane-Trägerrakete zunächst die Feststoffbooster mit einem Schub von etwa 13.000 Kilo Newton, die in den ersten beiden Minuten nach dem Start die rund 800 Tonnen schwere Rakete vom Boden abheben lassen. Die Hauptstufe mit dem Vulcain 2-Motor, der nach Ablauf des Countdowns als erstes gestartet wird, liefert weiter Schub bis die Rakete rund neun Minuten nach dem Start eine Höhe von etwa 160 Kilometer erreicht hat. Im Weltall übernimmt die Oberstufe, die bei der Ariane 5 mit dem HM7B-Triebwerk und bei der Ariane 6 mit Vinci angetrieben wird. Je nach Mission ist dieses Triebwerk rund 15 Minuten in Betrieb, um die Oberstufe mit den Satelliten im Weltraum in der richtigen Umlaufbahn abzusetzen.
Für das Vinci-Triebwerk der Ariane 6 wird in Ottobrunn die Schubkammer entwickelt und hergestellt. Die Schubkammer gilt als das „Herzstück“ des Triebwerks.
Vinci arbeitet mit tiefkaltem, sogenannten kryogenem Wasserstoff und Sauerstoff als Expander Cycle: „Zuerst umströmt der Wasserstoff die Brennkammer, kühlt sie herunter und verdampft dabei. Die entstehenden Gase werden als Antriebsmedium für die Treibstoffpumpen genutzt und anschließend zusammen mit dem Sauerstoff über den Einspritzkopf in die Brennkammer geleitet und verbrannt“, schildert Fertigungsleiter Stefan Winter. „Dieses sogenannte Expander Cycle Triebwerk gibt es auf der ganzen Welt nur einmal in dieser Performance. Während bei herkömmlichen kryogenen Triebwerken fast immer ein Gas-Generator für den Antrieb der Turbo-Pumpen nötig ist, funktioniert dieser Prozess bei der Vinci-Brennkammer anders. Beim Expander Cycle Triebwerk lassen wir zwar auch den Wasserstoff durch die Kühlkanäle, um die Kammer zu kühlen, jedoch durch das ausgeklügelte Design bleibt dieser sehr lange in der Kammer, damit er möglichst warm wird. Das expandierende Gas nehmen wir dann als Antrieb für die Turbopumpen. Das ist der große Vorteil vom Vinci Triebwerk.“
M80 Millturn fertigt Vinci-Triebwerk
Die meisten Triebwerksteile aus Ottobrunn werden auf einer WFL Maschine des Typs M80 gefertigt. Zu diesen Teilen zählt auch der Brennkammer-Grundkörper des Triebwerks. Im ersten Schritt wird der Grundkörper zum Drehen der Innenkontur vorbereitet. Anschließend erfolgt das Drehen und Fräsen der Außenkontur. Diese beiden Vorgänge wurden früher auf zwei Maschinen durchgeführt.
Mit der M80 Millturn werden nun beide Prozesse – Drehen und Fräsen - vereint und eine stabile Aufspannung garantiert. Das ist besonders bei Teilen mit langer und schlanker Bauart wie der Vinci-Brennkammer ein großer Vorteil. Zusätzlich sorgt das Nullpunktspannsystem für maximale Flexibilität in der Fertigung. „Das ist eine tolle Sache“, betont Winter.
Als Material verwendet man beim Grundkörper des Vinci-Triebwerks eine Speziallegierung. Die patentierte Kupfer-Silber-Zirkon-Legierung zeichnet sich durch hohe Festigkeit sowie einen guten Wärme-Übergangswert bei sehr bei guter Zerspanbarkeit aus. Speziell bei der Vinci-Kammer ist das von großer Relevanz. Durch die bereits erwähnte lange schlanke Bauart sind hier die Materialeigenschaften sehr wichtig. Das Material wird erst in Blöcken abgegossen und dann in die gewünschte Form geschmiedet. Die Qualität wird mittels Ultraschall garantiert und danach für die Fertigung freigegeben.
Die hauptsächlichen Schritte in der Produktion einer Vinci-Brennkammer sind nach der Lieferung des Rohteils Drehen, Fräsen, Galvanisieren, Schweißen und schließlich die Endbearbeitung. 80% der Workload werden dabei mit der M80 realisiert.
Ferner werden auch Schnittversuche für die Zukunft an der M80 durchgeführt. Die stabile Bauweise und die gute Kinematik geben hier mehr Möglichkeiten als gedacht. Mit Keramik-Schneidstoffen wurden bereits die ersten Versuche auf der M80 Millturn durchgeführt. Mittelfristig soll dieser Prozess auf der WFL Maschine für Inconel und Nickel qualifiziert werden. „Ich bin sehr zuversichtlich, dass wir dies auf der WFL Maschine realisieren können“ sagt Winter.
Innovationsgeist bei Technik und Personal
Auf der Millturn werden aktuell allerdings nicht nur Vinci-Bauteile gefertigt. Das Produktionsteam setzt die Maschine auch für die Produktion von Satellitenteilen, in der Entwicklung sowie für den Bau von Vorrichtungen ein. „Somit ist die Maschine durch den Mix perfekt ausgelastet“, ergänzt Stefan Winter. „Ich bin außerdem ein Fan von Entwicklungsthemen, weil das zweifellos die Workload von morgen ist und wir uns immer wieder neuen Herausforderungen stellen müssen. Momentan arbeiten wir beispielsweise an Komponenten für die Antriebe der Zukunft – Prometheus zum Beispiel.“
Die unterschiedlichen Versionen der Prometheus-Triebwerke sollen mit Flüssigwasserstoff und Flüssigsauerstoff sowie mit Flüssigsauerstoff und Methan betrieben werden. Es werden die ersten europäischen Triebwerke mit Verbrennungssteuerung sein, wobei sich der Motor an die Flugbedingungen der Trägerrakete in den unterschiedlichen Missionsphasen anpassen kann. Ein digitales System wird die Steuerung in einem Bereich von 30 bis 100 Prozent des Maximalschubs sicherstellen. Zudem wird Prometheus insbesondere mit künstlicher Intelligenz und einem Health-Monitoring-System ausgestattet, das jederzeit eine Diagnose der Triebwerksfunktion ermöglicht.
Die Familie der Prometheus-Demonstratoren profitiert zudem stark von den neuesten Technologien des 3D‑Druckverfahrens. Die mit dieser Technik produzierten Komponenten machen 70 Prozent des Gesamtgewichts des Triebwerks aus.
„Für all diese spannenden Zukunftsprojekte können wir die WFL sehr gut einsetzen“, sagt Stefan Winter. Um dies alles verwirklichen zu können, braucht es ein motiviertes Team an Ingenieuren und Facharbeitern. Vor allem sind an so komplexen Maschinen wie der WFL gute und gewissenhafte Mitarbeiter notwendig. Wenn eine Endbearbeitung mit einem Wert von mehr als einer halben Million auf der Maschine läuft, ist die Anspannung den Mitarbeitern anzusehen. Es ist schwierig, gutes Personal zu finden, daher sind wir immer auf der Suche nach guten Facharbeitern“, bekräftigt Winter.
„Für mich als Fertigungsleiter ist es besonders wichtig, den Arbeitsplatz für die Mitarbeiter interessant zu gestalten. Mittlerweile sind in der Fertigung in Ottobrunn überwiegend Meister und Techniker beschäftigt. Gute Facharbeiter sind wissbegierig und müssen dementsprechend gefordert und gefördert werden. Daher versuchen wir, die Stellen so interessant wie möglich zu gestalten. Aus diesem Grund erweitern wir die Programmierung um ein zusätzliches Programmiersystem. Unser mittelfristiges Ziel wird sein, dass ein Pool an Fachpersonal einer Maschine zugeordnet ist und diese auch vom Programmieren bis zur Fertigung des Bauteils eigenständig umsetzt. Diese Job-Rotation werden wir dann auf weitere Maschinen realisieren. In den nächsten 5 Jahren möchte ich die Fertigung dahingehend umstellen. Dafür brauchen wir engagiertes und qualifiziertes Personal,“ ist Winter überzeugt.
Er betont zudem: „Wir arbeiten hier mit extrem teuren Materialien nach höchsten industriellen Standards mit höchstem Qualitätsanspruch. Beim Raketenstart gibt es keinen zweiten Versuch, deshalb dürfen wir uns keine Fehler erlauben. Qualitätsbewusstes Personal ist hier zwingend erforderlich und das haben wir.“
Die Millturn-Frage
„In Punkto Bearbeitungszeiten konnte der Invest der WFL M80 Millturn / 3000 mm einen enormen Mehrwert leisten“, erläutert Stefan Winter. Die WFL ersetzte eine 3-Achs-Drehbank und eine 3-Achs Fräsmaschine. Auf der M80 implementierte man ein Nullpunktspannsystem, sodass das Rüsten nur noch einen Bruchteil ausmacht. Die Durchlaufzeiten und Liegezeiten wurden somit um mindestens 30% reduziert. „Ein großer Vorteil der WFL Maschine ist auch das große Werkzeugmagazin. Durch die Inconel-Bearbeitung haben wir immer zwischen vier und sechs Schwesterwerkzeuge in Verwendung, was ausreichend Werkzeugplätze erfordert. Durch das modulare Konzept des Magazins ist diese Voraussetzung gegeben. Sollte man doch noch mehr Werkzeuge brauchen, kauft man eben noch eine Werkzeugscheibe dazu. Das ist eine tolle Sache! So waren in der Vergangenheit für drei Prozesse drei NC-Programme und mehr nötig. Jetzt haben wir für die gleiche Arbeit nur noch ein NC-Programm zum Freigeben und Pflegen. Auch für das Configuration Management ist es eine deutliche Erleichterung, da hier weniger Daten gemanagt werden müssen. Das war ein riesiger Schritt nach vorne“, erzählt Winter begeistert.
Auf die Frage, wieso die Kaufentscheidung auf eine Millturn bzw. auf das Modell M80 fiel, antwortet Winter folgendermaßen: „Die Kinematik und die Referenzen der Maschine überzeugten schlussendlich zum Kauf. Worauf wir auch Wert legten sind eine schnelle Ersatzteilversorgung, namhafte Hersteller der verbauten Komponenten und auch die Nähe zum Hersteller.“
Die Maschine ist mit einem Pick-Up Magazin und einer WFL Systembohrstange ausgestattet. „In Zusammenarbeit mit WFL und Sandvik haben wir eine Sonderbohrstange von 1,4m Länge beschafft, um in Zukunft auch die Vinci-Innenkontur auf der WFL bearbeiten zu können.“ Winter berichtet darüber hinaus: „Um die Innenkontur auf der WFL ausdrehen zu können, haben wir auch eine neue Vorrichtung entwickelt, die jetzt fertiggestellt wurde.“
Die Anforderungen an die Maschine betrafen außerdem die Zuverlässigkeit und Genauigkeit. „Die Toleranz von etwa 1/100 im geforderten Arbeitsbereich muss die Maschine schaffen. Das ist unsere Anforderung. Temperatureinflüsse spielen hier eine große Rolle. Daher ist unsere Fertigungshalle auch klimatisiert. Von uns wird daher regelmäßig geprüft und kontrolliert und auch die Maschine ist temperaturüberwacht. Da ist WFL mit der Technologie gut dabei“, weiß Fertigungsleiter Winter.
Mit dem Softwarezyklus Utronix - der virtuellen U-Achse – werden bei der ArianeGroup Dichtflächen gefertigt. Denn an bestimmten Werkstücken werden zirkulare Oberflächen benötigt und zwar in jedem Winkel. „Bei etwa 135 Grad müssen wir um eine 20er Bohrung mit einer Bohrstange eine Dichtfläche mit 28 mm zirkular bearbeiten. Diese wird dann immer größer. Daher ist der Utronix-Zyklus bei uns ganz oft im Einsatz und sehr wichtig“, beschreibt Winter die Bearbeitung im Detail.
Der Fertigungsleiter betont außerdem den Vorteil der neuen Maschine am Beispiel der Herstellung eines Düsen-Demonstrators: „Wir waren aufgefordert einen Düsen-Demonstrator zu bauen. Die Herausforderung war, eine komplexe konische Innenkontur mit Kühlkanälen herzustellen. Nur durch die Stabilität der Maschine war der Räumprozess mit einer Länge von knapp 500 mm machbar. Durch die Kombination von Stabilität, Flexibilität und dem nötigen Arbeitsraum in der Maschine, kann man solche Sonderthemen einfach aufgreifen und umsetzen.“