Lavorazione completa dei componenti delle trasmissioni per i veicoli
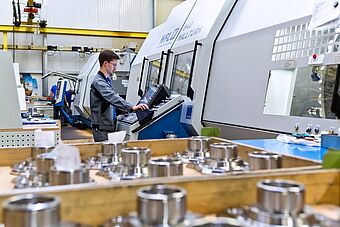
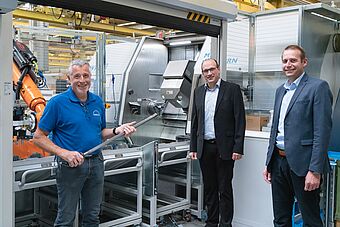
Per movimentare i veicoli corazzati sono necessarie forze motrici potenti. La spinta propulsiva corrispondente è garantita delle trasmissioni della Renk GmbH con sede principale ad Augusta. Non per niente Renk è conosciuta come lo specialista delle trasmissioni completamente automatiche per veicoli cingolati militari pesanti. E quando sono richieste performance di massimo livello, le soluzioni di produzione di WFL sono pronte a intervenire. Ma andiamo con ordine...
A differenza di quanto avviene nel settore automobilistico, nei veicoli cingolati pesanti è la trasmissione a occuparsi di tutte le operazioni di trazione, manovra e persino frenata. Tutto questo, nei veicoli equipaggiati da Renk, avviene grazie alla cooperazione di due diversi sistemi frenanti per velocità ridotte ed elevate, mediante un freno meccanico nel campo delle velocità ridotte e un freno idrodinamico a correnti parassite integrato chiamato Retarder. La trasmissione, con il comando delle funzioni di cambio, guida e frenata, rappresenta la centralina della mobilità di questi veicoli e riveste quindi un ruolo fondamentale in termini di sopravvivenza. Il tutto su veri e propri colossi che possono pesare anche 70 tonnellate, non superano la velocità d 72 km/h e devono potersi muovere agevolmente tanto su strada quanto fuori strada. In qualità di fornitore di oltre 40 eserciti in tutto il mondo, Renk può vantare il titolo di leader sul mercato mondiale degli equipaggiamenti a trasmissione per veicoli cingolati militari a partire dalle 40 tonnellate. Ogni trasmissione è concepita per uno specifico tipo di veicoli e adattata di conseguenza al singolo equipaggiamento e alla singola tipologia di motorizzazione. Questo significa che a partire dalla trasmissione di base selezionata, avviene poi un adattamento personalizzato su misura per le esigenze di applicazione del singolo veicolo. La manovra del veicolo si realizza attraverso l’influenza della velocità dell’attuatore sul rinvio laterale e quindi sul tamburo delle ruote dentate direttamente sulla catena. La direzione di marcia può variare quindi soltanto in concomitanza con la variazione della velocità sulle catene. In presenza di una pari variazione della velocità, il veicolo frena o accelera. Se la velocità, invece, è differente ne risulta un movimento di manovra, e in presenza di una forza discensionale contraria il veicolo ruota sul suo stesso asse. Tutte queste operazioni sono a carico della trasmissione che deve far fronte anche alle straordinarie forze, anche nelle condizioni più impensate e a lungo. Non sorprende affatto che tutto questo richieda una grande quantità di pezzi di produzione complessi che rispettino requisiti di qualità elevatissimi.
I componenti necessari per le trasmissioni rientrano in tre segmenti di produzione: i componenti dell’alloggiamento, i componenti cubici di piccole dimensioni (elementi che assorbono la forza, blocchi valvole, componenti del freno e componenti basati sulla meccanica dei fluidi) e i componenti rotanti dentati per la trasmissione della velocità. Sono proprio questi ultimi i pezzi tipici montati nel cablaggio elettrico della trasmissione e sono gli stessi che si rivelano particolarmente adatti per la lavorazione completa sulle macchine WFL Millturn. In questo segmento di fatto non esiste nessun pezzo che si distingua solo per la mera elaborazione del numero di giri. Oltre a questa funzione, emergono solitamente geometrie complesse e fresate insieme a un gran numero di fori. Le materie prime di lavorazione sono in prevalenza acciai estremamente robusti con una resistenza di 1200-1300 N/mm2 piuttosto che componenti a barra e di saldatura. “Tutto quello che è rotondo e che presenta una dentatura compare su una macchina WFL” è il motto generale. “Solitamente la produzione si struttura in serie di piccole dimensioni con lotti da 1 a 300 pezzi, laddove i lotti di dimensioni medie si aggirano sui 50 pezzi”, spiega il responsabile della produzione, Martin Wimmer. Ma non mancano i componenti per prototipi di trasmissione in lotti da 1 a 5 pezzi. Grazie alla flessibilità dei multitalenti WFL non è necessaria una produzione propria di prototipi con processi diversi. Anche i lotti di dimensioni più piccole possono essere distribuiti in modo estremamente redditizio per tutto il parco macchine già in essere. Inoltre decadono così le costose attrezzature di serraggio speciali, dato che sulle Millturn il serraggio dei pezzi avviene tramite ganasce standard o determinate ganasce speciali negli autocentranti a tre ganasce.
Un fattore decisivo ai fini della produttività delle macchine è la programmazione che avviene esclusivamente tramite l’apposito sistema Siemens NX CAD-CAM. “Per le prime quattro WFL avevamo puntato su diversi post processori per via dei diversi modelli di macchina. Ora però i post processori sono standardizzati e tutte le macchine funzionano tramite uno di essi. Il vantaggio risiede nel fatto che la pianificazione della produzione può avvenire indipendentemente dalla macchina. Questo significa che viene creato un programma senza sapere a quale macchina esso sarà destinato alla fine. Solo una volta che l’ordine è stato avviato la logistica di produzione decide su quale macchina produrre il singolo pezzo”, spiega Wimmer. L’intera procedura di simulazione della produzione avviene in CAD-CAM. In questa fase la permeabilità dei dati dalla costruzione dei componenti alla produzione sulla macchina gioca un ruolo importante. Su CAM è depositato un modello della macchina, dell’autocentrante, delle ganasce di serraggio, dei pezzi grezzi e pronti e degli utensili. La simulazione consente quindi di riprodurre in modo estremamente fedele la realtà e i programmi testati in questo modo funzionano senza alcun problema anche nella pratica. “Ci troviamo davvero bene con questo sistema. Grazie alla simulazione estesa non abbiamo praticamente più collisioni”, specifica Wimmer. Le dentature rappresentano un’eccezione nella simulazione. Sulle Millturn si eseguono dentature fino al modulo 4. Qui trovano impiego prevalentemente cicli WFL speciali per l’esecuzione di dentature a creatore, dato che possono essere impiegati in modo estremamente facile e veloce con l'inserimento dei parametri di dentatura.
La prima Millturn WFL è stata consegnata già nel 2010 ed è da allora che da Renk ci si concentra sulla lavorazione completa. “Allora abbiamo analizzato il nostro spettro completo di componenti, da quelli più piccoli a quelli dal diametro di circa 600 mm, perseguendo l’obiettivo di uniformare il parco macchine già esistente, ma piuttosto disomogeneo. Per l’intera gamma di componenti volevamo un unico progetto di macchina che potesse essere applicato a tutte le versioni di diverse dimensioni. La WFL partiva da ottime basi, dalla M35 fino alla M50. Oltre alla tornitura, alla foratura e alla fresatura sulla stessa macchina, per noi era molto importante anche l’esecuzione della dentatura, in particolare dal modulo 3 in qualità 8 con una dentatrice a creatore. Un concetto accennato da diversi produttori, ma provato alla fine solamente da WFL. In particolare l’indexaggio sugli assi B, estremamente stabile, offre i migliori risultati con grandi dentature Hirth. La classica struttura dell’unità di tornitura - foratura - fresatura WFL, con mandrino portafresa in versione a trasmissione ad alta velocità, garantisce le più alte prestazioni di sgrossatura in tutti gli intervalli di velocità. Il telaio della macchina, grazie alla sua eccezionale stabilità, non convince solo dal punto di vista della produttività, ma consente infine il mantenimento a lungo delle più strette tolleranze geometriche e il raggiungimento di qualità ottimali delle superfici”. Così Wimmer riassume le diverse basi tecniche, spiegando con chiarezza anche gli altri vantaggi: “Le macchine sono dotate di impianto di refrigerazione ad alta pressione pari a 80 bar e commutabile anche ad aria. Tutte le macchine sono dotate, oltre che del sistema utensili standard Capto C6, di un ulteriore contenitore portautensile particolarmente stabile applicato sull’unità di tornitura - foratura - fresatura. Tramite un attacco prismatico azionato idraulicamente è possibile applicare pesanti barre alesatrici o utensili speciali con la massima stabilità. Nelle macchine dai bordi con larghezza massima di 3000 mm, in aggiunta al magazzino standard è previsto un magazzino di raccolta per l’inserimento automatico di barre alesatrici più lunghe. “Non vogliamo più dipendere da altre macchine o da fornitori esterni per i singoli lavori specializzati”, spiega Wimmer. “In questo modo risulta un’elevata riduzione del cicli operativi, ma anche una netta riduzione del numero di lavorazioni. I singoli schemi di lavorazione si sono dimezzati grazie alla lavorazione completa. La lavorazione combinata garantisce anche una riduzione dei tempi di esecuzione. Le capacità in esubero derivanti dall’utilizzo efficiente vengono convogliate in altri lavori sulla macchina. Ad esempio, laddove si generi una grossa bavatura in fase di lavorazione, è possibile intervenire direttamente sulla macchina. In questo modo, non solo migliora la produttività, ma aumenta anche la sicurezza del lavoro con il rischio di lesioni ridotto al minimo. Particolarmente utile in questo contesto è stato il corso di formazione intensiva per utenti WFL in cui, oltre alla programmazione, è stata insegnata anche la pianificazione concettuale dell’intera procedura di lavorazione, nonché la scelta dei dispositivi di serraggio. Attualmente siamo arrivati a gestire nel settore produttivo delle trasmissioni per veicoli nove Millturn WFL di tre diverse dimensioni e due diverse lunghezze di tornitura.”
Per incrementare ulteriormente l’efficenza e aumentare il grado di utilizzo, l’ultima macchina consegnata, la M35 (2017) è stata equipaggiata con una soluzione di automazione di FRAI Robotics Solutions che sarà sfruttata ad esempio per l’ottimizzazione dell’efficienza nell’ambito delle ruote dentate planetarie. Nel frattempo anche una M40 è stata automatizzata. “Abbiamo ottenuto esattamente quello che ci serviva per le nostre esigenze, necessità e condizioni di spazio. Non abbiamo avuto nulla di meno di quello che volevamo. Con il secondo investimento vogliamo integrare anche una stazione di conversione in modo tale che i collaboratori possano concentrarsi sulle impegnative operazioni di lavoro”, dichiara soddisfatto Wimmer in merito al risultato dell’investimento.
Per quanto riguarda il tema dell’assistenza, Renk è ben equipaggiata con il suo team interno di manutenzione e svolge in loco lavori di riparazione di piccola e media entità. “Solo all’inizio abbiamo dovuto prima imparare che il cambio utensile può avvenire in qualsiasi posizione e che talvolta ci sono pezzi in mezzo. Ma sono difficoltà che appartengono al passato”, scherza oggi Wimmer ricordando le prime esperienze.
Attualmente anche da Renk il tema della raccolta dati automatica sta richiamando notevole interesse. A tal proposito è già in uso un sistema nel quale tramite una cabina è possibile visualizzare la rappresentazione dello stato della macchina. Poiché l’utilizzo trasparente lungo diverse fabbriche è al centro della discussione, si punta in questo caso a una soluzione indipendente dai produttori delle macchine. E come per il tema CAD-CAM, è già in atto una stretta collaborazione con Siemens. Sul piano della Predictive Maintenance e del Condition Monitoring Renk conta già ottime esperienze a alcune soluzioni: il Renk Monitoring, provato anche sulle trasmissioni Renk, è già stato adattato per le macchine utensili e costituisce una buona base di partenza per sviluppare il tema in futuro.