Eine neue Ebene der Wertschöpfung
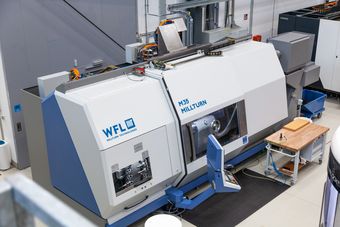
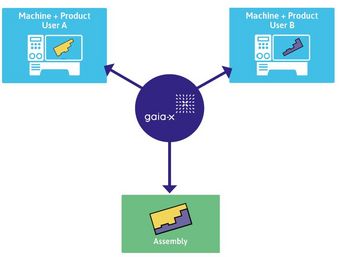
Marktveränderungen und wechselseitige Abhängigkeiten zwischen Wertschöpfungsstufen erfordern sowohl neue technische als auch wirtschaftliche Lösungen. Wie können Unternehmen resilienter gegenüber diesen Herausforderungen werden? Wie kann ein Nutzen aus gesteigerter Wirtschaftlichkeit gezogen werden? Diesen Fragen stellt sich das länderübergreifende Projekt „EuProGigant“. Ziel ist es, eine smarte und souveräne Nutzung von Daten für die Produktion sicherzustellen und diese nach Europa zu holen.
Im Rahmen des Projekts „EuProGigant“ werden produktionsrelevante Daten identifiziert, extrahiert und organisiert. Durch Gaia-X (souveräne Dateninfrastruktur für Europa) werden ein Datensouveränitäts-Reglement aufgestellt, Kommunikationsstrukturen im Sinne einer europäischen Daten-Cloud-Welt überlegt und diese Konzepte in das Themengebiet der Produktion hineingetragen. Ein erster Demonstrator wurde im Mai 2022 auf der Hannover-Messe vorgestellt, an welchem das Daten-Trading, die Datensouveränitäts-Aspekte als auch datenrechtliche Themen umgesetzt wurden. Abgebildet ist dies in der Struktur, den Informationsdaten und technischen Mechanismen. Im nächsten Schritt geht es darum, diese Technologie auf tatsächliche Anwendungsfälle zu projizieren und in die Produktion zu bringen. WFL ist dabei einer der zentralen Umsetzungspartner im Projekt.
Um aussagekräftige Daten zu erhalten, befinden sich Anwender von WFL Maschinen im Konsortium. Plasser & Theurer hat etwa 2022 eine WFL Maschine mit Automatisierung gekauft. Die Maschine soll auch ohne menschlichen Einfluss laufen und mithilfe der Prozessüberwachung Daten von der Maschine in eine Leitebene bringen. Die Betrachtung erfolgt unternehmensintern, aber mit dem Kommunikationsstandard von Gaia-X. Später soll dies über die Grenzen des Unternehmens hinaus passieren, sodass man sich in ein Produktionsnetzwerk einbindet und austauscht - etwa bei den Toleranzwerten. Weitere Maschinenhersteller des Konsortiums sind die Gebr. Heller Maschinenfabrik GmbH und die ARBURG GmbH & Co. KG. Eine WFL Maschine steht bei Heller in der Spindelfertigung und macht dort die wesentliche Drehbearbeitung. Weitere Maschinen stehen bei der Fa. Arburg und machen die wesentliche Dreh-Fräsbearbeitung für die hydraulischen Funktionalitäten beim Zusammenfahren der späteren Spritzgießwerkzeuge. Am IFT (Institut für Fertigungstechnik) in Wien steht eine M35, an der erprobt und evaluiert wird und die Ergebnisse in die Produktionsstätten der Partner übertragen werden sollen.
Ideales Bauteilmatching
Die M35 MILLTURN, welche im IFT der TU Wien steht, wird im Rahmen einer Kooperationslinie in einen Datenverbund integriert. Dazu gibt es einen Anwendungsfall bzw. eine Arbeitsgruppe, die sich „Ideales Bauteilmatching“ nennt. Die Problemstellung dabei lautet: Wie kann sichergestellt werden, dass die Funktion einer Baugruppe nach dem Montageprozess gewährleistet ist? Wie kann dabei Einfluss auf Fertigungsschritte und Montageprozesse genommen werden? Und wie bringen wir einmal gefertigte Bauteile mit entsprechenden Fügepartnern so geschickt zusammen, dass sie die Funktionsanforderungen unmittelbar erfüllen? Denn das spart etwa die Wareneingangsprüfung. Das spart Infrastruktur, weil Testinfrastruktur gemeinsam zwischen Zulieferern und Kunden genutzt wird. Letztendlich beschleunigt das den Montageprozess. Das Suchen von passenden Komponenten oder das Nacharbeiten entfällt, weil von Vornherein in der Funktionserfüllung gedacht und bis an die Fertigungsschritte zurückgegeben wird. Was muss man nun konkret tun, damit zu einem existierenden Bauteil auch das passende Gegenstück gefunden wird? Das ist eine reale Problemstellung, die aktuell mit manuellen Zwischen- oder Lagerarbeitsschritten durchgeführt wird. Man denke beispielsweise an das wiederkehrende Schleifen von Abstandsringen, die hochpräzise im Zehntel bis Hundertstel μ-Bereich gefertigt werden müssen. Hier werden Ansätze durch intelligente Unterstützung in Form eines Bauteil-Matching-Services geliefert. Dieser Service hilft bei der Charge, die vom Kunden A angeliefert wird: Passen diese und jene Bauteile mit exakt der Typennummer zu den Bauteilen vom Zulieferer B zusammen? Diese Information hat man schon, bevor die Teile überhaupt in der Montage eingetroffen sind. Eine beschleunigte Unterstützung durch digitale Prozesse und damit eine gesteigerte Wertschöpfungsgeschwindigkeit sind hier klarer Output. Dahinter muss allerdings eine Dateninfrastruktur stehen, welche diese Art von Service ermöglicht.
Ein Internet der neuen Generation
Jeder kennt das Internet und jeder nutzt es auf eine Art und Weise, dass es intuitiver gar nicht sein kann. Mit der Vision einer gemeinsamen Dateninfrastruktur wie es im Projekt EuProGigant zum Ziel gesetzt wird, erleben wir – vereinfacht gesprochen - eine neue Generation des Internets. Das meint ein Internet, welches ein Vielfaches mehr an Daten und digitalen Diensten beinhalten wird. Die Such-Funktionalität kann wie eine Art Webbrowser genutzt werden. Beispielsweise kann nach Daten von Maschinenherstellern gesucht werden, etwa über die CO2 Bewertung. Über Schnittstellen erfolgt eine Verbindung von Rechner zu Rechner („peer2peer“).
Die Daten sind für jeden Ökosystem-Teilnehmer verfügbar. Die Suche funktioniert wie bei Google: Ich gebe meinen Suchbegriff ein, kann entsprechende Filter nutzen usw. Das Besondere an diesem System ist die Souveränität. Diese bedeutet bei EuProGigant, dass man stets selbst kontrollieren kann, was man bei einer Interaktion preisgibt. Hier müssen Fragen gestellt werden wie: Zu welchem Zweck darfst du mit mir interagieren und für wie lange? Welche Durchsetzungsmöglichkeiten habe ich und welche Kontrollmechanismen werden dabei aktiv? Durch eine gemeinsame Vertrauensinstanz wird diese Souveränität sichergestellt.
Gesteigerte Wertschöpfungsgeschwindigkeit
In der fertigenden Industrie zählen etwa das Abheben eines Spans von einem Werkstück oder ein gefertigtes Werkstück als wertschöpfende Prozesse. Also immer dann, wenn Energie eingesetzt wird, um Dinge umzuformen, in Form und Lage zu verändern und dann einen neuen Nutzwert zu haben. Die vor- und nachgelagerten Prozesse rund um Logistik, Warenhaltung und Produktionsplanung. Diese Hilfsprozesse ermöglichen die Wertschöpfung. Wie können diese Prozesse vereinfacht und beschleunigt werden. Digitale Tools sind ein wesentlicher Baustein und die Digitalisierung ist dabei die Grundvoraussetzung, um unternehmensübergreifende Standards fortzuführen. Wie lässt sich ein gedachter, standardisierter Prozess mit digitalen Tools digitalisieren und anschließend automatisieren?
Beim Thema Werkzeug-, Prozess- oder Maschinenüberwachung wird dies bereits umgesetzt. Zu jedem Zeitpunkt ist der Zustand der Maschine oder des Prozesses bekannt. Man kann schnell auf Veränderungen reagieren. Diese werden unmittelbar angezeigt und damit lässt sich die Verfügbarkeit der Maschine zusichern. Die Qualität des Werkstücks wird kontrolliert und zugesichert. Und wenn das schon in der Fertigung möglich ist, kann diese Information auch unmittelbar mit dem Kunden geteilt werden, der dann z.B. die Wareneingangsprüfung nur noch stichprobenartig durchführen muss. An diesen Stellen wird beschleunigt und das kreiert unglaublichen Gewinn.
Von der Erprobung in die Umsetzungsphase
Der dritte Meilenstein wurde im Oktober 2022 abgeschlossen. Aufgezeigt wurde dabei, dass die erste Durchlaufphase der forschungsnahen Erprobung einen Abschluss gefunden hat. Die nächste Phase betrifft die Umsetzung. Zusammen sollen hier konkrete Erfolge in der Umsetzung gezeigt werden können; etwa bei der Weiterentwicklung der Demonstratoren im Bereich „Ideales Bauteilmatching“. Die Zielstellungen sind beispielsweise, sensorisch-fühlend in der Werkzeugmaschine aktiv zu sein und damit Endtoleranzen von Bauteilen schließen zu können. Eine entsprechende parametrische Anpassung der Maschine an die Toleranzlage lässt sich damit vornehmen. Mit der Gaia-X Entwicklung soll Schritt gehalten und die wichtigen Erfahrungen sukzessive in die anderen thematischen Arbeitsgruppen integriert werden. Das aus dem Demonstrator gezogene Wissen wird somit vollständig in die Unternehmen getragen.