Hoch hinaus mit Alp Aviation
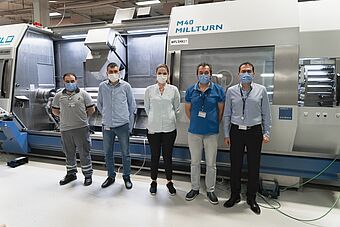
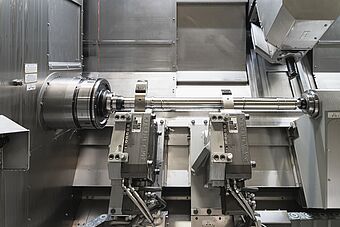
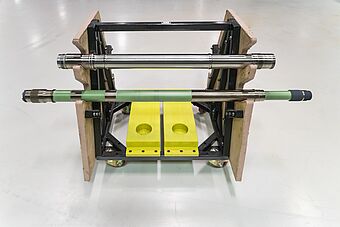
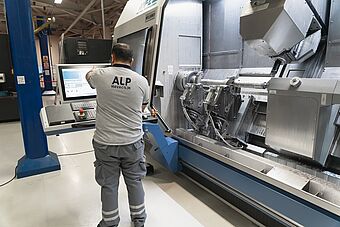
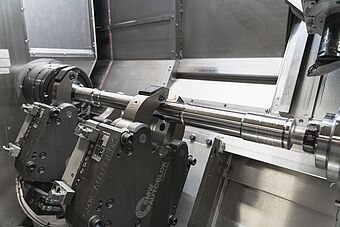
Das Redaktionsteam von WFL reiste nach Eskişehir, um sich mit Serkan Erten, Business Unit Director der Engine Business Unit bei Alp Aviation, über die Geschäftsbereiche von Alp Aviation und die Verbindung zwischen WFL und Alp zu unterhalten.
Herr Erten, geben Sie uns doch bitte einen kurzen Überblick über Alp Aviation. Was sind die Kernkompetenzen des Unternehmens und in welchen Geschäftsbereichen sind Sie tätig?
Alp Aviation ist ein Joint Venture mit Sikorsky Aircraft, einem 1998 gegründeten Lockheed Martin-Unternehmen. Unsere Kernkompetenz liegt auf jeden Fall in der Zerspanung und Bearbeitung von Titan, Superlegierungen, Aluminium, Stahl, rostfreiem Stahl, Magnesium- und Kupferlegierungen. In diesen Bereichen können wir auf einen umfangreichen Erfahrungsschatz zurückgreifen. Alp Aviation hat vier Werke in Eskişehir mit einer Gesamtproduktionsfläche von 50.000 m2. Zu unseren Kunden zählen weltweit führende Unternehmen der Luft- und Raumfahrttechnik, wie beispielsweise Pratt & Whitney, Sikorsky, Collins Aerospace, Honeywell, Pratt & Whitney Canada, Lockheed Martin und Boeing.
Wir unterhalten Geschäftsbeziehungen vor allem nach Nordamerika und Kanada, liefern aber nicht nur an US-Unternehmen, sondern auch nach Europa, z. B. nach Polen, Frankreich und Tschechien. Der Exportanteil beträgt ca. 98 %, wobei 90 % nach Nordamerika gehen. Gefertigt wird ausschließlich in unserem Werk in Eskişehir, wo fünf Business Units angesiedelt sind. In der Aerostructure Business Unit dreht sich alles um die Fertigung von Flugzeugbauteilen. Kunden sind hier Unternehmen wie Boeing, Lockheed Martin, Sikorsky und Collins Aerospace. Die Engine Business Unit, die ich leite, konzentriert sich auf die Herstellung von Triebwerkskomponenten. Wir fertigen dynamische Triebwerksbauteile, vor allem für Pratt & Whitney und Honeywell. Im Militärbereich arbeiten wir am F-135-Triebwerk und im kommerziellen Bereich an Getriebeantriebwerken (GTF). Honeywell ist auch ein wichtiger Kunde für Triebwerkskomponenten. Wir haben angefangen, Triebwerkswellen für kommerzielle Triebwerke von Honeywell zu produzieren. Zu diesem Zweck haben wir in eine Komplettbearbeitungsmaschine von WFL investiert, genauer gesagt in die M40 MILLTURN mit 3000 mm Spitzenweite. Im Fokus der Rotary Wing Business Unit steht die Fertigung von Komponenten für Drehflügler. Dieser Geschäftsbereich ist für dynamische Helikopterbauteile, Fahrwerke, Getriebe und andere dynamische Komponenten zuständig. Special Processes ist der vierte Geschäftsbereich von ALP. In diesem Bereich verfügen wir intern über umfangreiche Kapazitäten und können die chemischen und mechanischen Prozesse selbst durchführen. Mit der Landing Gears Business Unit gibt es bei ALP auch noch einen fünften Bereich, der sich mit der Herstellung von Landebeinen beschäftigt. Hier arbeiten wir mit Collins Aerospace und Heroux Devtek am F-35-Programm und an anderen kommerziellen Programmen für Boeing und Airbus.
Was war der Hauptgrund für die Investition in eine MILLTURN-Komplettbearbeitungsmaschine von WFL?
Dazu muss ich zunächst kurz erläutern, wie unser Unternehmen arbeitet. Derzeit haben wir mehr als 250 Werkzeugmaschinen und produzieren unterschiedlichste Bauteile für die Luft- und Raumfahrtindustrie. Zur Herstellung dieser Bauteile kommen vor allem 5-Achsen- Fräsmaschinen und Komplettbearbeitungsmaschinen zum Einsatz. Auf der neuen M40 MILLTURN von WFL fertigen wir ausschließlich Wellen. Der Hauptgrund für die Investition war, uns bei Triebwerksherstellern den Ruf eines Kompetenzzentrums für die Fertigung von Wellen zu erarbeiten. Durch die MILLTURN von WFL sind wir für unsere Kunden zum Triebwerkswellenhersteller avanciert. Als Verbindung zwischen Turbine und Kompressor sind Triebwerkswellen ganz wichtige Antriebsbauteile.
Bei Alp Aviation werden Triebwerkswellen in Längen von 1.000 mm bis 2.000 mm gefertigt. Die dafür eingesetzten Werkstoffe sind vor allem Inconel und Maraging-Stahl. Die Fertigung mit Inconel ist für uns nicht neu, da wir bereits seit 2008 Antriebskomponenten aus Titan und Inconel herstellen. Daher können wir aufreichlich Erfahrung mit diesen Werkstoffen zurückgreifen. Unsere Wellen werden weiterhin aus Inconel-Werkstoffen und hochfestem Stahl gefertigt.
Welche Voraussetzungen müssen für die Investition in eine Komplettbearbeitungsmaschine gegeben sein?
Für die Fertigung dynamischer Antriebskomponenten benötigen wir produktive und prozesssichere Hightech-Maschinen und wir müssen uns auf hervorragende technologische Performance verlassen können. Im Allgemeinen werden bei der Fertigung von Triebwerkskomponenten Nickellegierungen verwendet. Diese Nickelsonderlegierungen sind hochwarmfest. Das heißt, diese Werkstoffe weisen eine hohe Festigkeit auf, sind schwer zu bearbeiten und erfordern zur Erfüllung der hohen Qualitätsstandards der Branche sehr hohe Fachkompetenz.
Welche Chargengrößen sind in Ihrer Branche und Business Unit gängig?
In der kommerziellen Luftfahrtindustrie ist der Produktionsumfang je nach Plattform unterschiedlich. In manchen Fällen produzieren wir je nach Größe der kommerziellen Plattform ca. 600 Werkstücke pro Jahr. Das mittlere Fertigungsvolumen reicht von 200 bis 300 Stück pro Jahr. Aber das ist die Grenze. Unsere Branche ist nicht gerade bekannt für einen hohen Grad an Automatisierung oder große Serien. Wir bewegen uns nicht im Bereich von 10.000 Werkstücken pro Jahr. Im Luft- und Raumfahrtgeschäft liegt die maximale Stückzahl bei ca. 1.000 pro Jahr.
Welche Maschinen oder Prozesse wurden mit dem Kauf der M40 MILLTURN ersetzt?
Nach dem Aufbau der neuen MILLTURN fingen wir an, zum ersten Mal größere Wellen zu produzieren. Wir haben die Maschine also nur angeschafft, um größere Wellen fertigen zu können. Bis dahin hatten wir nur kleinere Wellen von 250 bis 500 mm Länge auf relativ kleinen Maschinen gefertigt. Als wir die ersten Zeichnungen für größere und längere Wellen erhielten, nahmen wir mit WFL Kontakt auf, da wir wussten, dass WFL in der Luft- und Raumfahrtbranche einen guten Ruf hat. Jetzt produzieren wir ca. 200 Wellen pro Jahr.
Welche technologischen Möglichkeiten bietet die M40 MILLTURN?
Mit der M40 MILLTURN erzielen wir eine optimale Zerspanungsleistung, eine hohe Oberflächengüte, hohe statische und dynamische Steifigkeit sowie zuverlässige und reproduzierbare Genauigkeit. Das In- Prozess-Messen ist insbesondere bei der Wellenfertigung eine wichtige Technologie zur Einhaltung der sehr engen Toleranzen. Wir bevorzugen Bearbeitungszentren, da die Werkstücke nicht von Maschine zu Maschine bewegt werden müssen. Ein weiterer ausschlaggebender Faktor für den Kauf dieser Maschine war Zeitersparnis.
Was sind die Hauptvorteile der Komplettbearbeitung?
Bei der Komplettbearbeitung auf einer Werkzeugmaschine kann die Bearbeitungszeit um 30 % reduziert und eine Steigerung der Flexibilität um 60 % erreicht werden. Unsere Kunden müssen sich auf unsere Leistung verlassen können. Wir müssen einfach und effizient arbeiten, um dadurch kurze Durchlaufzeiten erreichen.
Erzählen Sie bitte etwas mehr über die Fertigung von Triebwerkswellen in der MILLTURN. Ein kleiner Einblick in den Fertigungsprozess wäre sehr spannend.
Die Fertigung einer Welle, angefangen mit der Beschaffung des Werkstoffs bis hin zur Schlichtbearbeitung, dauert ungefähr sechs Wochen. Bei dieser Art von Wellen kommen chemische und mechanische Prozesse zum Einsatz, wie z. B. Wärmebehandlung, Kugelstrahlen, Chromplattierung, Silberplattierung, Schleifen oder Wuchten. Die sechs Wochen beziehen sich auf den gesamten Prozess. Die Tatsache, dass der gesamte Prozess im eigenen Unternehmen durchgeführt werden kann, ist die größte Stärke von Alp Aviation und ein überzeugendes Argument gegenüber den Kunden.
Wie sehen die Strategien von Alp Aviation für die Zukunft aus?
Unser Ziel ist es, uns nicht nur als zentrales Kompetenzzentrum für Design und Fertigung von Antrieben und Baugruppen für Starrflügler und Drehflügler zu etablieren, sondern auch als Kompetenzzentrum für die Fertigung von Wellen. Die türkische Regierung hat Alp Aviation als Forschungs- und Entwicklungszentrum anerkannt. Damit ist ein wichtiger Schritt getan, in nationalen und internationalen Programmen eine noch bedeutendere Rolle als Design- und Konstruktionspartner zu spielen. Wir werden so in der Lage sein, für unsere Kunden als globaler Zulieferer im Bereich Design und Fertigung zu agieren.
In vielen Unternehmen ist Industrie 4.0 gerade ein Thema. Welche Maßnahmen haben Sie hinsichtlich Industrie 4.0 ergriffen?
Wir haben von Anfang an, als das Thema aufkam, die technologischen Entwicklungen weltweit verfolgt. Vor zwei Jahren wurde dann eine flexible Fertigungsanlage mit vier Werkzeugmaschinen und einem zentralen Werkzeugwechselsystem aufgebaut. Dank dieser innovativen Lösung konnte die Produktivität um 30 % gesteigert werden. Unser Ziel ist es, Arbeitsstunden zu reduzieren und Verbesserungen im Technologiebereich zu forcieren. Alle unsere Investitionen stehen im Zeichen dieser Strategie. Als wir beschlossen, in eine MILLTURN zu investieren, kamen dieses Thema und die künftige Entwicklung auch auf den Tisch. Sobald die wirtschaftliche Situation sich verbessert und die Zahl der Anfragen wieder steigt, werden wir sicherlich in weitere Maschinen und in die Automatisierung investieren.