Klares Wasser mit Hiller Zentrifugen
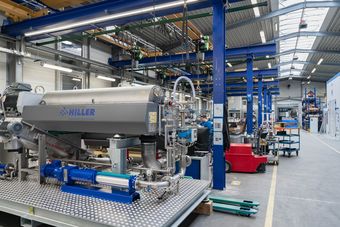
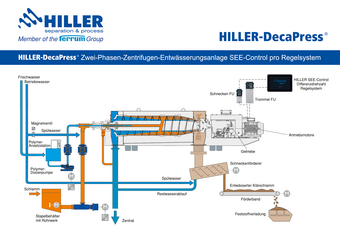
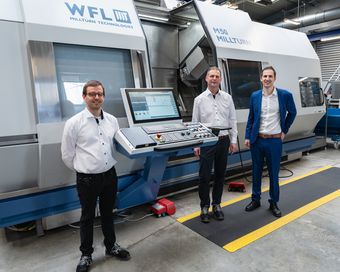
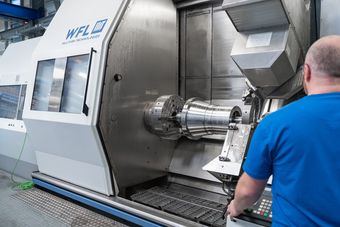
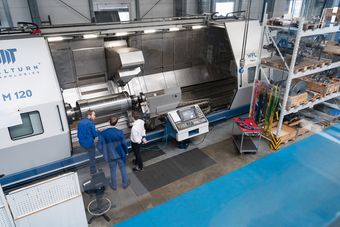
Die Dekanter-Technologie ist ein Verfahren zur Trennung von Flüssigkeiten und Feststoffen. Sie wird häufig in der Industrie eingesetzt, um feste Partikel aus Flüssigkeiten zu entfernen oder um verschiedene Flüssigkeiten voneinander zu trennen. Die Firma Hiller GmbH fokussiert sich seit mehr als 50 Jahren auf die Entwicklung und Produktion von Dekantierzentrifugen und löst Trennaufgaben in den verschiedensten Branchen.
Denkt man an Obst- und Gemüsesäfte, Olivenöl, Fischverarbeitung, Milchprodukte, Küchenabfälle, Klärschlammbehandlung, Algenernte, Ölaufbereitung oder gar an die Gewinnung von Pflanzenextrakten, wüsste man auf den ersten Blick nicht, was diese Bereiche verbindet. Aber genau hier ist Hiller aktiv. Hiller Dekanter sorgen beispielsweise in der Lebensmittelindustrie für die Trennung von Milch und Rahm oder werden zur Gewinnung von Olivenöl eingesetzt. Man kann beispielsweise davon ausgehen, dass 80-90% des spanischen Olivenöls über einen Hiller Dekanter läuft. Eine weitere interessante Anwendung ergibt sich in der Chemieindustrie, in welcher mit Dekantern Lösungsmittel getrennt oder zur Aufbereitung von Abwasser eingesetzt werden. Den wohl wichtigsten und nachhaltigsten Bereich finden wir in der Abwasseraufbereitung wieder. Dekanter werden hier zur Trennung von Feststoffen und Flüssigkeiten in Kläranlagen genutzt. Das anfallende Abwasser wird mithilfe von Dekantern gereinigt, um es dann wieder in die Gewässer zurückleiten zu können. Ein Thema, welches uns kaum bewusst ist, von dem wir jedoch alle betroffen sind.
Fest-Flüssig Trennung im Fokus
Wie sieht nun die Beschaffenheit eines Dekanters aus und was steckt hinter dieser phänomenalen Technologie? Ein Dekanter besteht aus einem zylindrischen Gehäuse mit einer sich drehenden Trommel im Inneren. Die Trommel ist durch eine Trennwand in zwei Abschnitte unterteilt. In den einen Abschnitt wird die zu trennende Flüssigkeit eingespeist, während in den anderen Abschnitt das Endprodukt und der Feststoff aus der Trennung abgeführt werden. Wenn die Trommel rotiert, entsteht eine Zentrifugalkraft, die die Feststoffe nach außen drückt. Gleichzeitig sinken die schwereren Flüssigkeiten wie z.B. Wasser, in Richtung der Außenwand der Trommel und werden dort abgeführt. Leichtere Flüssigkeiten wie z.B. Öl, schwimmen auf der Oberfläche der schwereren Flüssigkeit und werden ebenfalls getrennt.
Alles in allem bietet die Dekantertechnologie den Vorteil, dass sie eine sehr effektive Trennung von Flüssigkeiten und Feststoffen ermöglicht und dabei sehr wenig Energie verbraucht. Zur Herstellung der Dekanter setzt Hiller auf Inhouse-Produktion und fertigt den Großteil der Dekanter-Komponenten am Standort in Vilsbiburg.
Einzug der Komplettbearbeitung
Die Hiller GmbH zerspant verschiedenste Komponenten der Dekantierzentrifugen in MILLTURN Dreh-Fräszentren des Herstellers WFL. Das Herz des Dekanters ist der Rotor, welcher zur Gänze, bestehend aus einer Schnecke, Trommel und der Antriebseinheit, auf den Multitalenten von WFL gefertigt wird. Mit der neuen M50 MILLTURN mit 2000mm Spitzenweite werden neuerdings zusätzliche Teile hergestellt, welche bisher zugekauft wurden. Die Insourcing Strategie steht für die Hiller GmbH an oberster Stelle. Vor dem Gesichtspunkt der Lieferengpässe, welche in der letzten Zeit immer wieder ein Thema waren, setzt man bei Hiller auf die Unabhängigkeits-Strategie. Die Fertigungstiefe wird außerdem wieder mehr nach innen gerückt, um eine höhere Wertschöpfung zu erzielen.
Stefan Brauner, Leiter der Produktion, gibt Einblicke in die Fertigung: „Mit der neuen WFL wird versucht, größere Lose zu produzieren bzw. diese optimal auszulasten. Vor Einsatz der Komplettbearbeitung war der Maschinenpark um ein Vielfaches größer. Mit Dreh-Fräszentren konnten wir uns effektiv schmälern. Mehrere Bearbeitungszentren wurden ausgetauscht und durch die neue WFL ersetzt. Der große Vorteil liegt in der Vereinfachung des Fertigungsverfahrens. Früher war der Prozess ein längerer: auf einer Maschine wurde gedreht, danach gefräst, manchmal wieder gedreht. Je nach Notwendigkeit waren die verschiedenen Fertigungsschritte auf unterschiedliche Bearbeitungszentren verteilt. Jetzt funktioniert alles in einem, man braucht nicht mal mehr umzuspannen.“
Auch die Mitarbeiter aus der Produktion sind Fans der Maschinen. Mit dem Trio M50, M80 und M120 hat man eine sehr gute Fertigungsausstattung, welche verschiedene Teilegrößen bewältigen kann. So sind auf den größeren WFLs die gleichen Futter im Einsatz und es werden vorwiegend Teile, wie Trommel konisch, Trommel zylindrisch, Schneckenkörper und Stirnwände etc. produziert. Auf der M50 hingegen werden aktuell Getriebeteile hergestellt.
Auf den großen Maschinen, M80 und M120, werden kleinere Losgrößen zwischen fünf und zehn Stück gefahren. An der neuen M50 fertigt man hingegen 20 bis 50 Stück im 2-Schicht Betrieb. Die Vorteile der Komplettbearbeitung liegen auf der Hand: der Fertigungsprozess eines Werkstücks passiert auf einer Maschine – Qualitätsprüfung inklusive. Die Möglichkeit, eine Vielzahl an Werkzeugen in der Maschine zu integrieren, spricht für sich. Alles in allem machen die reduzierten Rüstzeiten und generell geringen Durchlaufzeiten die Komplettbearbeitung aus.
Andreas Lehner, WFL Sales Manager, ergänzt: „Zu den USPs unserer Maschinen zählt die sehr hohe Stabilität aufgrund des Schrägbettkonzepts. Die Maschinen weisen kurze Wirkabstände zwischen Zerspanungspunkt und den Führungen auf. Maximale Effizienz bei der Zerspanung als auch höchste Genauigkeit bei der Fertigbearbeitung werden damit garantiert.“
Qualitativ hochwertig und zuverlässig
Die wichtigsten Kriterien bei der Anschaffung der Komplettbearbeitungszentren waren die Prozesssicherheit, Serviceverfügbarkeit und vor allem die hohe Qualität der Maschinen. Da bereits eine M80 und M120 seit längerer Zeit im Einsatz sind, wusste man, dass der Service einwandfrei läuft. Dies war auch ein ausschlaggebender Punkt, eine weitere Millturn zu kaufen.
„Die fähigen Männer und Frauen, die bereits am Telefon im Problemfall gut weiterhelfen können als auch die ergänzende Fernwartung sind top Lösungen. Der Anwender kann mittels Pincode eine gesicherte Verbindung zu WFL ermöglichen und im Nu wählt sich ein Servicetechniker von WFL auf die Steuerung ein, um das Problem zu identifizieren bzw. eine Diagnose zu erstellen. Die Nähe zueinander und die schnellen Reaktionszeiten sind einfach top“, schließt Stefan Brauner.
Andreas Lehner ergänzt „Es ist nicht nur wichtig, dass jemand im Servicefall so schnell wie möglich vor Ort ist, um das Problem rasch zu lösen. Besonders relevant für unsere Kunden ist die Dauer bis zum Wiederaufnehmen der Produktion. Jeder unserer Servicemitarbeiter ist auf allen Maschinentypen geschult und kann somit den Kunden bestmöglich vor Ort unterstützen.“
Da Hiller hohen Wert auf die Qualität ihrer Produkte legt, war eine passgenaue Auslegung der Technologie ein entscheidender Faktor. CNC-Programmierer Stefan Geiger erklärt, dass der Bearbeitungsablauf gemeinsam mit WFL im Vorfeld entwickelt wurde, um die gefragten Getriebeteile in den geforderten Genauigkeiten herstellen zu können. „Die Vorabbetrachtung des Teiles wurde von WFL sehr genau abgewickelt, sodass wir uns einer hochgenauen Fertigung sicher sein konnten.“
Technologievielfalt, die zählt
Technologisch betrachtet, lassen die MILLTURNs keine Wünsche offen. Aktuell wird versucht, den Technologieprozess des Stoßens zu integrieren. Angedacht wäre hier, die Innenverzahnungen der Getriebeteile auch mit den Komplettbearbeitungszentren abzuhandeln. Außenverzahnungen wurden mit den WFL-eigenen Technologiezyklen bereits erfolgreich umgesetzt. Die Bearbeitungszeiten der verschiedenen Werkstücke variieren je nach Größe des Bauteils. Bei Trommelteilen ist die Bearbeitungszeit etwas länger, da spricht man von Laufzeiten von 1 ½ bis 3 ½ Stunden. Der Großteil der Werkstücke besteht aus Edelstahl, die Getriebeteile vorwiegend aus Stahl. Materialien, die sehr gut mit der WFL Komplettbearbeitungsmaschine bearbeitet werden können.
Mit iControl Advanced+ wird auf der M50 die Prozesssicherheit gewährleistet, sodass die Maschine vollautomatisch laufen kann. Die Maschine ermöglicht eine kontinuierliche Überwachung der Prozesssignale auf der Steuerung, sodass jede kleinste Unregelmäßigkeit sofort erfasst werden kann. Sollte eine verschleißbedingte Überlast bestehen oder ein Werkzeugbruch erkannt werden, stoppt die Maschine automatisch. Weiters werden durch die Möglichkeit des integrierten Messens Werkzeuge automatisch korrigiert, um den perfekten Bearbeitungsprozess sicherzustellen.
Bei der Programmierung wird mit dem CAD/CAM Programmiersystem TopSolid gearbeitet. Des Weiteren setzt Hiller nun auch verstärkt auf die WFL Simulations- und Programmiersoftware CrashGuard Studio, welche zur finalen Optimierung der Programme genutzt wird.
Nachhaltigkeit großgeschrieben
Bei Hiller werden Produkte hergestellt, die der Umwelt helfen, sich wieder zu regenerieren. Die Dekanter-Technologe trägt dazu bei, verschmutzte Gewässer wieder in Trinkwasserqualität aufzubereiten. In der Lebensmittelbranche können Lebensmittel länger haltbar gemacht werden, was zu geringeren Lebensmittelverlusten und einer verbesserten Ressourceneffizienz beiträgt. Alles in allem bewirkt der Einsatz von Dekantern eine effiziente Trennung von Fest- von Flüssigstoffen, um sie wiederzuverwenden oder zu entsorgen. Dies trägt generell zur Minimierung von Abfall und zur Ressourcenschonung bei. Die hocheffizienten WFL-Maschinen passen da optimal zur nachhaltigen Philosophie von Hiller.