Messtechnologien (Teil 2)
Um den heutigen Anforderungen gerecht zu werden, ist das Messen in zukunftsweisenden Fertigungsprozessen ein integraler Bestandteil. Mittels Closed-Loop Ansatz wird versucht, den Kreislauf zwischen Produktionssystem, Maschine, Mensch und Messtechnik so einfach und effizient wie möglich zu gestalten. Einer der wichtigsten Punkte in diesem Kreislauf ist das Messen während des Fertigungsprozesses.
Bevor mit einem Messtaster gemessen werden kann, muss dieser kalibriert werden. Dies erfolgt meist vor einem Bearbeitungsprozess und wird durch den Bediener durchgeführt. Optional kann das Kalibrieren vollautomatisch über das NCProgramm durchgeführt werden.
Ein Messtaster muss nach der Berührung der Oberfläche durch den Taststift noch eine bestimmte Auslenkung erfahren bis das Schaltsignal an die Maschinensteuerung gesendet wird. Dieser Vorlaufweg ist a priori nicht bekannt und abhängig von der Länge des Taststifts, der Antastrichtung etc. – er ist aber genau reproduzierbar.
Für viele Standardmessverfahren ist die Kenntnis der Vorlaufwege nicht erforderlich, wie z. B. bei der Messung der Tiefe einer Frästasche. Wenn der Messtaster die Bezugsfläche und den Taschengrund antastet, ergibt die Differenz der beiden Schaltpunkte exakt die Taschentiefe - auch ohne Kalibrierung, da die beiden Messpunkte mit gleicher Antastrichtung angefahren werden und sich die entsprechenden Vorlaufwege bei der Differenzbildung aufheben.
Wenn aber Merkmale wie z. B. die Breite einer Frästasche oder ein Wellendurchmesser mit der Y-Achse vermessen werden sollen, so müssen einander gegenüberliegende Flächen am Werkstück mit entgegengesetzter Antastrichtung angefahren und die Differenz der Schaltpunkte ermittelt werden. Um hier nun exakte Messwerte erhalten zu können, ist eine Kalibrierung des Messtasters, also die genaue Kenntnis der Vorlaufwege, notwendig.
Ein Kalibrieren ist nur möglich, wenn der erwartete Soll-Wert bekannt ist. Der Kalibriervorgang kann entweder an einer beliebigen Stelle oder mit Hilfe einer Kalibriervorrichtung durchgeführt werden. Der Messtaster kann etwa an einem beliebigen Durchmesser, mit einem Kalibrierring oder einer speziellen Vorrichtung kalibriert werden.
Das Kalibrieren mit einer Vorrichtung vereinfacht den Kalibrierungsprozess, da der Soll-Wert bereits bekannt und in entsprechenden Maschinendaten der Steuerung hinterlegt ist.
Kalibriereinrichtung am Reitstock der M200 MILLTURN inkl. Temperaturkompensation
Die mit temperaturstabilisiertem Wasser aus der Rückkühlanlage durchströmte Kalibriereinrichtung ist in Richtung der Y-Achse am Reitstock montiert und mit einer Abdeckhaube versehen, die das Eindringen von Schmutz in den Messraum verhindert.
In der Mitte der Kalibriereinrichtung befindet sich ein Quader, an dem die Schaltpunkte des Messtasters in X1, Y1 und in Z1- Richtung ermittelt werden können. Zusätzlich sind bis zu 12 Messstellen montiert, an denen unterschiedlich große Distanzen kalibriert werden können. Über zwei Temperatursensoren werden die aktuelle Temperatur der Kalibriereinrichtung und des Maschinenbetts automatisch erfasst. Die Kalibrierung an den 12 Messstellen ermöglicht die präzise Erfassung des aktuellen Wärmeausdehnungszustandes des Messsystems der Maschinenachse Y. Dies ist vor allem bei großen Werkstückdurchmessern von Bedeutung. Die Wärmeausdehnung der Messsysteme in Richtung X und Z wird anhand der gemessenen Maschinenbetttemperatur und der bekannten Ausdehnungskoeffizienten der Messsysteme berücksichtigt.
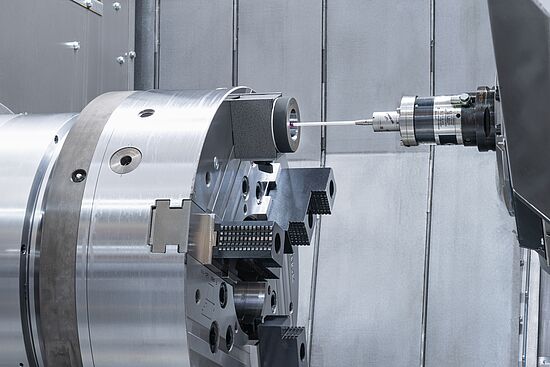
Kalibrieren des Messtasters am Kalibrierring.
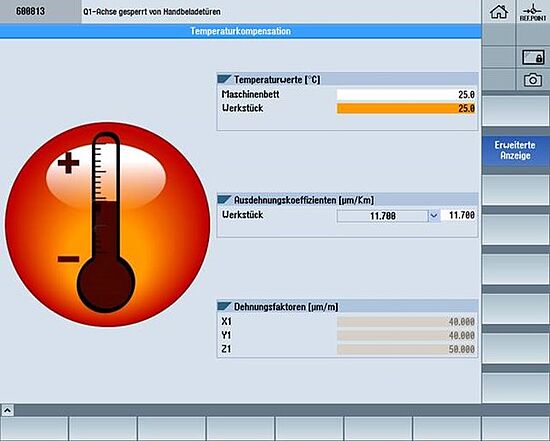
Die WFL Mess- und Korrekturzyklen sorgen dafür, dass die Messergebnisse aus der Maschine nunmehr den Ist-Abmessungen des Werkstücks bei einer Normtemperatur von 20° entsprechen. Werden Werkzeuge oder Positionen korrigiert, ist die Temperaturkompensation bzw. das Zurückrechnen auf die Normtemperatur von 20 °C vorteilhaft für die erzielbare Genauigkeit.
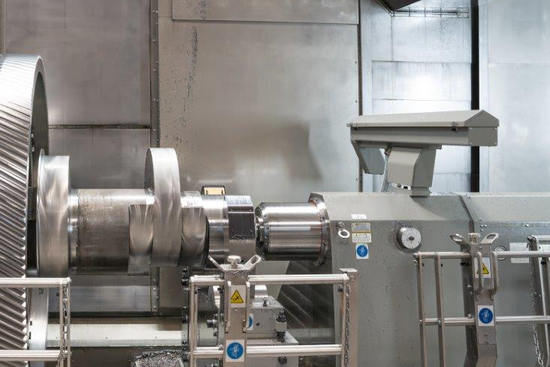
Zur Erfassung der Werkstücktemperatur wird ein Handmessgerät mitgeliefert. Über ein NC-Unterprogramm kann z. B. unmittelbar vor der finalen Bearbeitung einer engen Passung automatisch ein Menübild eingeblendet werden, welches den Bediener auffordert, die aktuelle Werkstücktemperatur zu messen und ins Menübild einzugeben.
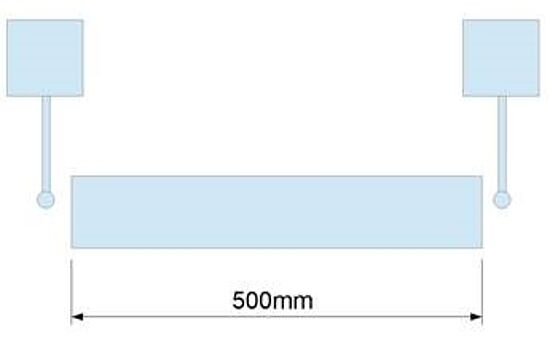
Beispiel:
Die 500 mm lange Welle mit einer Temperatur von 26 °C wird in der Maschine vermessen. Die Maschinentemperatur beträgt 20 °C. Da hier das Werkstück eine Übertemperatur hat, dehnt es sich aus und wird ein zu großes Maß gemessen. Ohne Temperaturkompensation kommt man zu einer Istlänge von 500,033 mm.
Temperaturausdehnungskoeffizient Werkstück = 11 μm/Km
Temperaturausdehnungskoeffizient Messlineal = 8 μm/Km