Mit Innovationsgeist zur Spitze
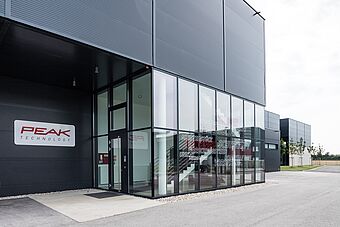
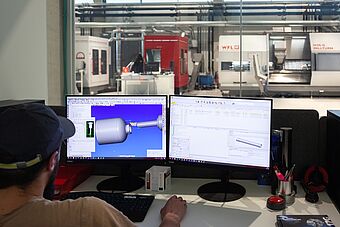
„Gewerbepark Holzhausen“ steht auf einem Schild zwischen Feldern und einer kleinen Gemeindestraße. Nichts lässt hier vermuten, welches High-Tech-Potenzial uns in der kleinen Ortschaft nahe dem Flughafen Linz erwartet. 2007 von Dieter Grebner gegründet, versorgt die Firma Peak Technology die Formel-1-Branche sowie diverse Luft- und Raumfahrtunternehmen mit komplexen und ultraleichten Kohlefaser-Verbundstrukturen.
Zukunftsthemen wie die Elektrifizierung der Luftfahrt und autonomes Fliegen sind hier allgegenwärtig. Die 120 Mitarbeiter von Peak fertigen Komponenten für Fluggeräte der Zukunft. Matthias Lechner, Technischer Geschäftsführer, erklärt die visionären Projekte. Peak Technology beschäftigt sich bereits heute damit, wie die Mobilität der Lüfte in 10 oder 20 Jahren aussehen wird. Doch es geht bei Peak noch wesentlich höher hinaus: Für Raumfahrtprojekte werden mit Kohlefaser umwickelte Hochdruckspeicher, Zündergehäuse und Strukturkomponenten produziert. Die ultraleichten Hochdruckspeicher, die einem Druck von bis zu 700 bar standhalten, gehören schon fast zum Standardrepertoire. Die Komponenten für die Motorenperipherie der Formel-1-Boliden, die ebenfalls zum Portfolio von Peak gehören, klingen bei all den Science-Fiction-Projekten beinahe als wäre von ein paar Teilen einer Dampfmaschine die Rede. Ungeachtet der High-Tech-Anforderungen sieht man sich selbst als Manufaktur, da viele Prozesse in der Faserverbund-Technologie in aufwändiger Handarbeit ablaufen. Also traditionelle Handwerkskunst vereint mit High-Tech-Fertigung. In der CNC-Fertigung setzt Peak Technology seit 2019 auf eine M35-G MILLTURN von WFL.
Dem Wunsch nach Verbesserungen in der CNC Fertigung wurde in den letzten drei Jahren Rechnung getragen. Mit der Anschaffung einer M35-G MILLTURN wurde kürzlich der topmoderne Maschinenpark für die Zukunftsanforderungen komplettiert. Früher wurden die Teile auf Dreh- und Fräsmaschinen getrennt bearbeitet. „Wir wollten das Umrüsten auf ein absolutes Minimum reduzieren und die Fertigungsplanung vereinfachen. Außerdem sind die Toleranzanforderungen der Kunden sehr hoch und praktisch nur durch Komplettbearbeitung und möglichst wenig Aufspannungen erreichbar“, fasst Matthias Lechner, Technischer Geschäftsführer von Peak, die Anforderungen zusammen. Schließlich müssen Freiformflächen mit Toleranzen im Bereich von 0,005mm prozesssicher eingehalten werden. Eine Klimatisierung der gesamten Fertigung sowie Messtechnik auf höchstem Niveau stellen bei diesen Anforderungen eine Grundvoraussetzung dar. Die Losgrößen der einzelnen Aufträge bewegen sich zwischen 10 und 30 Teilen. „Doch selbst bei „Serien“ von 10 Stück wird immer nur ein Teil gefertigt und dann eine Woche später wieder eines, denn unsere Kunden wollen nicht die ganze Lieferung auf einmal, sondern alles „just-in-time“, erklärt Lechner. „Aktuell fertigen wir 10 bis 15 verschiedene Teile auf der MILLTURN von WFL. Aber es werden praktisch täglich mehr. Bei den zu bearbeitenden Materialien handelt es sich sowohl um metallische Werkstoffe wie Titan, hochfeste Stähle und Aluminium als auch um Kohlefaserbauteile“, erklärt Christian Brunner, Teamleiter der zerspanenden Fertigung. „Wenn wir jetzt eine MILLTURN hätten, dann wäre das sooo viel einfacher“, soll er früher bei schwierigen Bauteilen gesagt haben.
Im Zuge der Erweiterung des Unternehmens war es dann 2018 so weit. „Wir haben uns alle Marktbegleiter in den verschiedenen Werken angesehen. Was uns an der MILLTURN von WFL besonders gefallen hat, war die Schrägbett-Konstruktion mit dem massiven Guss-Bett. Also eine sehr steife Maschine. Letztendlich war uns auch die Nähe zum Hersteller wichtig. Viele internationale Firmen arbeiten über Händler. Das wäre für uns nicht in Frage gekommen“, erinnert sich Matthias Lechner.
„Da wir häufig mit sehr kleinen Werkzeugen arbeiten, war die Frässpindel-Drehzahl von 16.000 U/min sehr wichtig. Die Standard-Option von 12.000 U/min reichte da nicht aus. Gut, dass WFL bereits seit einiger Zeit eine Getriebespindel-Variante mit 16.000 U/min im Testbetrieb und auch bei einem Kunden erfolgreich im Laufen hatte. Spanvolumen und Leistung stehen bei uns eigentlich nicht im Vordergrund. Vielmehr brauchen wir die Drehzahl in Kombination mit hoher Stabilität und Präzision“, sind sich Brunner und Lechner einig. Besonders bei Bauteilen mit sehr kleinen Radien kommen winzige Kugelfräser zum Einsatz. Gespannt werden die Teile in einem 3-Backenfutter mit Backenschnellwechsel, wobei zum Testen aktuell ein im Futter aufgenommenes Hainbuch-Spannsystem zum Einsatz kommt. Teilweise werden die Werkstücke auch von innen über einen Spanndorn gespannt. Die Spanndrücke sind bei Spannung der Werkstücke im Futter frei programmierbar und können innerhalb einer Aufspannung NC-gesteuert in kleinen Schritten verändert werden. Die programmgesteuerte Änderung der Spannkraft ist auch ohne Öffnen des Futters möglich. Diese Anforderungen sind für die dünnwandigen Werkstücke notwendig. „Wir lernen jeden Tag neu dazu und obwohl wir beim 5-Achsen- Fräsen gut aufgestellt sind, zeigt uns die MILLTURN immer wieder neue Möglichkeiten, an die wir uns erst nach und nach herantasten müssen. Das ist einfach eine andere Dimension der Komplexität. 5-Achsen-Fräsen ist laufend auf der MILLTURN im Einsatz. Das funktioniert einwandfrei und liefert genaue Ergebnisse. Wir sind hochzufrieden damit. Neben der Dreh-, Bohrund Fräsbearbeitung sollen zukünftig auch Verzahnungen mit der MILLTURN durchgeführt werden“, fasst der technische Leiter die Erfahrungen mit der neuen Maschine zusammen.
Eine softwaretechnische Nuss gab es im Vorfeld für WFL zu knacken: Mittels Form-Inspect von M&H sollte der Abgleich zwischen Nullpunkt im CAM-System und der tatsächlichen Position in der Maschine automatisch erfolgen. Mittels Messtaster wird das gespannte Rohteil im Raum vermessen. Mit dieser Information kann der Nullpunkt der Bearbeitung zur tatsächlichen Lage des Rohteils mittels einer speziellen Softwarelösung direkt auf der Steuerung korrigiert werden. Wenn beispielsweise die Position oder die Form des Rohteils nicht exakt dem CAD entspricht, wird die ideale Position über eine best-fit Berechnung ermittelt, das Koordinatensystem des CNC-Programmes in die Idealposition verschoben bzw. gedreht und ein gleichbleibendes Aufmaß am gesamten Rohteil sichergestellt. Dadurch wird gewährleistet, dass im gesamten Bearbeitungsprozess möglichst konstante Aufmaße und kontinuierliche Schnittbedingungen herrschen. Das System wurde in enger Kooperation zwischen WFL und M&H angepasst und bei WFL ausführlich getestet. Unmittelbar nach Lieferung der Maschine war das System voll funktionsfähig.
Beim Werkzeugsystem setzt Peak auf Capto C6. Hier war ebenfalls die Stabilität ausschlaggebend. „Wir haben mit verschiedenen Spezialisten aus der Branche gesprochen und das Ergebnis war, dass Capto unsere Anforderungen perfekt erfüllt“, erläutert Matthias Lechner die genauen Analysen im Vorfeld der Investition. Werkzeuge werden über ein Voreinstellgerät eingestellt und die Werkzeugdaten auf einem Chip direkt am Werkzeug gespeichert. Beim Aufrüsten des Werkzeuges werden die Daten automatisch in die Steuerung übertragen und in der Werkzeugverwaltung hinterlegt. Peak verfolgt das Ziel, sämtliche Werkzeuge für alle Aufträge in der Maschine zu belassen. Bei der aktuellen Kapazität des Magazins der M35-G MILLTURN von 120 Plätzen sind auch für Schwesterwerkzeuge ausreichend Reserven vorhanden.
Wenn es um Präzision geht, erlaubt Peak keine Kompromisse. Die Maschine besitzt in allen Linearachsen Glasmaßstäbe. Obwohl die Maschine bei der Abnahme innerhalb aller Toleranzgrenzen lag, hat Peak um noch mehr Genauigkeit gebeten. Und so kitzelten die WFL-Spezialisten auch noch die allerletzten μ heraus. Bei allem nur das Präziseste, lautet die Devise.
Zum Bearbeiten der Kohlefaser-Komponenten wurde die Maschine mit einer speziellen Absauganlage ausgestattet. So kann zwischen der Absaugung von Ölnebel und dem bei der Kohlefaserbearbeitung entstehenden Staub umgeschaltet werden. Auch beim Thema Konnektivität bewegt sich Peak auf höchstem Niveau. Alle Maschinen in der Fertigung wurden mit dem ERP-System vernetzt und übertragen Laufzeiten und Maschinenstillstände in Echtzeit. Außerdem nutzt Peak auch die IoT-Lösung MindSphere von Siemens. Dadurch kann WFL auf Wunsch von Peak Sensordaten, wie die Temperatur der Fräseinheit, analysieren und gegebenenfalls auf zukünftige Serviceanforderungen
frühzeitig reagieren.
Alle CNC-Maschinen müssen mit einem CAM-System programmierbar sein, lautet die klare Anforderung von Peak. Die Programmierung erfolgt mithilfe der CAD/CAM Software hyper-Mill. Komplexe Teile erfordern einen Programmieraufwand von zwei bis drei Tagen, wohingegen einfachere Teile bereits innerhalb weniger Stunden gefertigt werden können. Zur Simulation im Vorfeld der Bearbeitung wird auch die Softwarelösung CrashGuard Studio von WFL genutzt, wobei damit speziell die Übergabe des Werkstückes auf die Gegenspindel simuliert wird, da dies am CAD-CAM System noch nicht möglich ist.
Zum Schutz der Maschine, der wertvollen Bauteile und der Werkzeuge, nutzt Peak das Anti-Kollisionssystem CrashGuard von WFL. „Das ist bei unseren Anforderungen einfach notwendig“, erklären die Fertigungsexperten von Peak einstimmig. „Wenn wir damit einen Crash vermeiden, hat sich die Investition schon gerechnet“.