A machine that impresses on every level
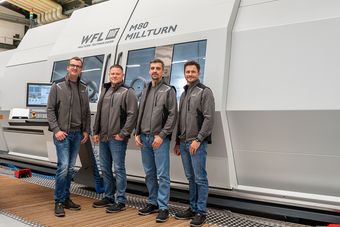
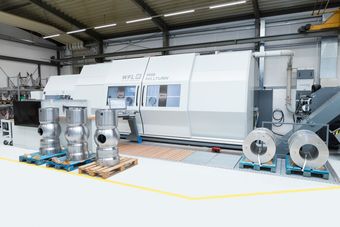
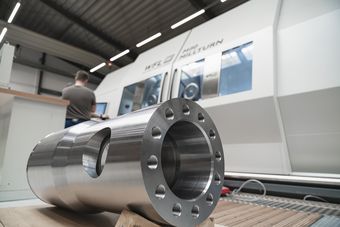
With its investment in a M80 MILLTURN / 3000mm, HORA Holter Regelarmaturen GmbH & Co. KG are setting new standards in the machining of valve parts weighing up to six tonnes. WFL was chosen following an intensive selection process. Several machine manufacturers were in the running, but ultimately WFL impressed this German family company in every regard. WFL's service and availability were the crucial factors. Read on to find out what other criteria were important to HORA and how WFL was able to meet every requirement.
HORA is a medium-sized family company employing around 300 people based in Schloß Holte-Stukenbrock, North Rhine-Westphalia. Engineering and production take place at its German headquarters, supported by a sales office in Shanghai and diverse sales partners around the world. Since the company was founded in 1967 by Georg Dresselhaus, it has focused on the development, design and manufacture of innovative control valves and actuators. By concentrating on the business areas of Power Generation, Gas Applications, and Process and Building Technology, HORA fulfils highly-specific customer requirements. HORA supplies customised control technology to ensure their customers' plants run smoothly and efficiently over the long term.
In 2023, annual turnover totalled 50 million euros. All the company's profits are reinvested, leaving a factory packed with state of the art equipment. In the last five years, over 10 million euros has been invested in production. The company's investment in a WFL turning-boring-milling centre is the biggest single investment in a machine since the company was founded. Managing Partner Professor Dieter Dresselhaus focuses heavily on process innovation, thereby ensuring the long-term success of the company over decades.
The challenge
Since 2009, HORA has been concentrating on its production strategy for complete machining, which was limited by the size and weight of the components. In recent years, there has been an increase in the number of parts that could not be manufactured using complete machining methods for this very reason. The market is also moving towards materials that are difficult to machine, which pose an increasing challenge. As a result, a machine with the corresponding chip space and cutting performance was needed.
Since 2015, HORA has focused on the digital transformation of the entire order handling process, from the customer's enquiry to delivery and beyond. During this time, tools such as an ERP system with integrated APS, a PDM system, a product configurator and a digital dispatch management system were introduced. All systems are networked.
In addition to easing the challenges in heavy machining, investing in a turning-boring-milling centre was to be the last piece of the puzzle in creating a fully digitalised state-of-the-art process along the production line.
"We wanted to bring our vision of full digital networking to HORA, by implementing and digitally connecting what we currently regard as the best machine for our requirements," says member of the Management Board Eduard Schmidt. He adds: "We needed someone who could support us technologically and as a partner in setting a new standard in the digital process and help us bring our vision to life. From our perspective, WFL was absolutely the right decision, as both HORA and WFL value delivering the optimum solution for the customer. This common understanding paved the way for setting a new standard together," emphasises Schmidt.
The decision in favour of WFL
There were several crucial factors that tipped the balance in favour of MILLTURN. From the initial consultation to the end of the project and beyond, HORA felt they were in good hands with WFL. In an interview with WFL, HORA praised the entire project team and emphasised that every promise had been met or even exceeded. "We visited WFL in Linz several times and were impressed by their outstanding expertise. Workpieces stored on site with similar material, i.e. difficult to machine, and above all, geometrically challenging, had already been produced. WFL's practical references spoke for themselves. WFL focuses on the technology and process integration," says Andreas Petker, Production Team Leader at HORA.
HORA were also impressed by WFL's guaranteed service and spare parts availability. With WFL, HORA has a partner that is quickly available thanks to their geographical proximity, minimising the risk of production downtimes.
We must also not overlook the turning-boring-milling unit itself, which is the heart of the machine. The fact that this is manufactured entirely in house at WFL was also a decisive factor and one of WFL's unique selling points, which impressed HORA.
Another decisive USP was the WFL system boring bar, which offers HORA added value in terms of flexibility and costs due to the geometry of the components being produced.
HORA has been heavily expanding its multiple machine operation in single part production for many years and therefore tends to opt for machines that work with a Siemens controller. This is easier for the employees as it means that every machine is operated in a similar way.
The machine has been making an impression in daily use since the start of the year. The solid construction and the machining performance are remarkable. "Machining at this scale is not new for us, but the cutting capacity is really remarkable and truly impressive! The cutting capacity was outstanding even during final acceptance of the machine, as the 160 indexable insert drill effortlessly cut the heat-resistant stainless steel (1.7335) with two tonnes of feed force and no vibration on the machine cover. In such moments, I like to grab the door but there were no vibrations to be felt," stresses Michael Beiwinkel, Head of Production and Building Technology. The stability and solid construction were impressive, as is the fact the machine does not need 100% of the drive force. Despite difficult materials and strenuous tools, there are still drive reserves – and all with a high chip volume being removed. The machine was commissioned at HORA in January 2024.
Ergonomic work
As an innovative company, HORA believes in optimum workstation design for its employees. The MILLTURN was sunk into the existing hall floor to allow optimum access to the workpieces during machining. "WFL really impressed us in this regard too. We didn't even need a special solution, as the machine is designed for optimum ergonomic conditions right from the start," says Production Team Leader Sascha Brechmann. Firstly a one-metre deep pit was dug, followed by the necessary construction work. Now the MILLTURN was sunk by 400 mm. The storage area in front of the machine was designed as a steel welded construction so that workpieces of up to six tonnes can be placed down without any problems. The workstation for the MILLTURN, as well as all the other machines in the HORA hall, offer occupational safety and excellent ergonomics. There are wooden floors integrated into the ground for an ergonomically optimal working environment. Likewise, there are no steps and therefore access is at ground level, which considerably reduces the risk of slipping.
The machine is currently working in two-shift operation. Four employees have undertaken the WFL training programme in Linz and worked directly on the machine at HORA with the technician and now operate the WFL machine independently. Just eight weeks after the final acceptance of the machine, the M80 MILLTURN was sometimes working on single parts without a directly assigned operator. In the case of components with a longer machining time, the machine runs without supervision, especially overnight.
The machine is mainly used to manufacture valve bodies, perforated discs, perforated cages and plugs. These manufactured parts can, in turn, be found in any type of control valve for challenging, customer-specific solutions in a wide range of industries.
New standards in digital networking
With the decision to opt for WFL, HORA was able to close a gap in the digital transformation of the order handling process. Now the production process is linked to this digital process which runs from the customer's enquiry through to design engineering. "Everything is now digital, from the enquiry, to the quote and the resulting product – regardless of where we are in the factory," says Schmidt.
The CAM team use the CAD models stored in the PDM system by the Design Engineering department to create the CAM data record, which is stored in ShopFloor following simulation in CrashGuard Studio.
"The combination of the applications in CAM and CrashGuard Studio is really exciting. We often have operations where there's no machine cycle, so it has to go CAM first of all," says Sergej Kunz, CAM Team Leader.
The required tools are now set up and measured using the data stored in ShopFloor. The determined tool data is also stored in ShopFloor. With a datamatrix code generated in ShopFloor, the tool can be identified and booked at any time.
The integrated APS in the ERP system takes on all the production control at HORA. If the APS plans a production order on the WFL, all data (NC program from the CAM and tool data from the measurement) is loaded onto the machine from ShopFloor. During machining, regular measuring cycles are run to guarantee the quality of the component. This creates a digital twin for each component produced.
"The measuring cycles during the process have enabled us to significantly increase the quality of our workpieces," says Sergej Kunz. He adds: "Thanks to the measuring cycles, we have benefited from considerable gains in efficiency, especially for large components. We generally hadn't been able to measure certain contours during the machining process before, and now we can. With the measuring cycles and the cross switch, we can now carry out highly accurate manufacturing and this benefits us enormously in terms of time and quality."
Steps for the future
Managing Partner Professor Dieter Dresselhaus is clearly committed to the Schloß Holte-Stukenbrock site, as 100% of the company's profits have been reinvested for several years now. This enables new standards to be set in process and product innovation.
HORA's products make a significant contribution to advancing the energy revolution, which is why the company expects to see a continued increase in demand for its premium products. As a result, increasing efficiency continues to be a focal point. This includes the efficient use of energy and resources in the company's own activities. "We ensure that our material procurement is sustainable. We avoid air and sea freight as far as possible. Of our entire procurement volume of 17 million euros, only around 1.5 million euros goes towards goods from Asia. This also underlines our largely regional purchasing strategy and our many partnerships in Germany and Europe," emphasises Schmidt.
“As a Partner for Performance, we believe our strengths lie in understanding customers' needs and turning them into products for challenging control tasks. We also realised WFL shared this focus when discussing the machine layout at WFL. This was confirmed as the project progressed," says Schmidt. He continues: "We definitely chose the right partner. The company's values are lived and breathed, both at HORA and WFL."