Flanx – The WFL gearing solutions
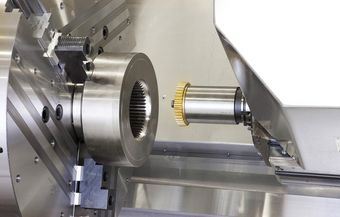
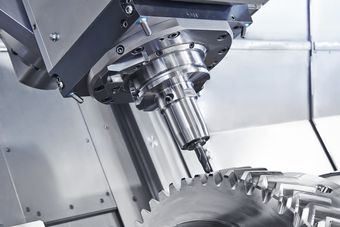
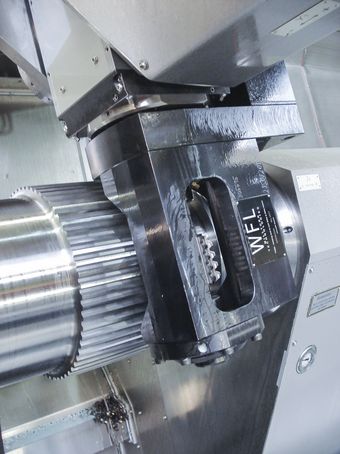
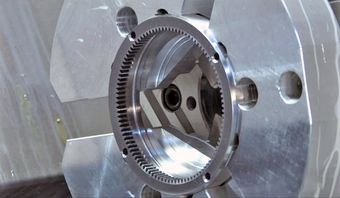
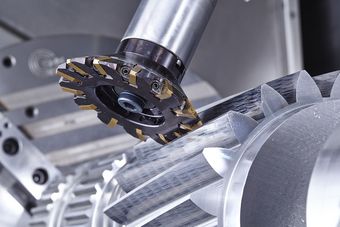
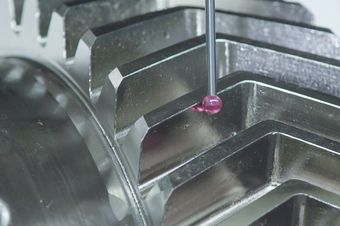
Flanx-Measure under the microscope
From filigree internal gears with high accuracy requirements to large external gears that
require high roughing efficiency. Thanks to the extensive experience and development assets
it has gained over many years, WFL offers the right technological solution for every type
of gear cutting. Are you already making the most of our expertise in gearing solutions to generate
more added value in your company? The critical features when manufacturing gearing are high
quality standards, profile accuracy and machining solutions that offer both reliability and flexibility.
Flanx combines the development of software as well as hardware solutions for integrating
complete gearing solutions into a WFL machine.
The various WFL Flanx hardware solutions
The turning-boring-milling unit has a few additional functions that are essential for milling work. The tool spindle can be released from the spindle bearings and the spindle can be hydraulically clamped so that the bearings are not compromised during machining. This is a major advantage in terms of the durability of the bearings. The machine also features a cooled ball screw on the Z-axis, which prevents localised overheating.
The B-axis is also decisive when it comes to the manufacture of gearing solutions. The machine can index or clamp the B-axis and reaches an extremely high holding force. The MILLTURN therefore provides an extremely stable and efficient way of producing gearing with the B-axis. A further technological feature is the WFL prismatic clamp holder for gear hobbing tools. This prismatic clamp holder is hydraulically clamped to the underside of the turning-boring-milling unit by means of a special interface. This gear hobbing device can be used to securely and precisely clamp hobs with a diameter of 160 mm and a length of 254 mm, i.e. relatively large hobs. The hobs are clamped in the spindle of this device without backlash, which enables a faster changeover if the tool needs to be replaced due to wear.
As a pioneer in complete machining, WFL offers the following advantages when it comes to gearing tasks:
- Comprehensive gearing expertise
- Flexible and user-friendly gearing software solutions
- Advanced, reliable and automatically exchangeable tool solutions
- Closed-loop measurement solutions, including for gearing
- Greater flexibility thanks to various machining options
- Reduction in special tools
- Reduced lead times
- Better machine utilisation (special machines are often poorly utilised)
- Higher productivity, minimally manned or unmanned shifts