Lead time reduced by 50%
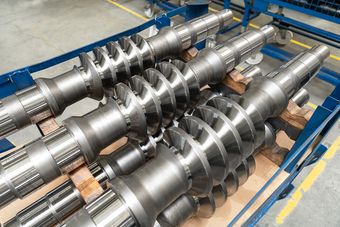

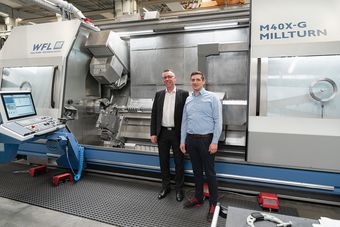
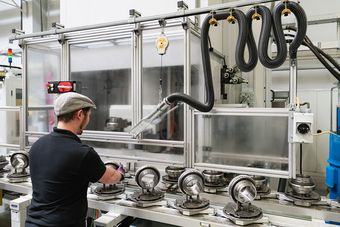
AUMA Riester GmbH & Co. KG is uniting its divisions – AUMA Water, AUMA Power, AUMA Oil & Gas, AUMA Drives and AUMA Industry – under the slogan ‘AUMA – one brand’. The divisions relate to the industries that the company operates in, and the synergies between these areas are exploited in procurement as well as in development, design and engineering. The subsidiary AUMA Drives is based in Coswig. There are around 200 employees at this site – 150 in production and 60 in indirect areas. AUMA Drives is an international active system supplier for customized gear units and actuator solutions. For decades, AUMA Drives has focused on highest quality in gear unit production. The use of modern equipment is of central importance. The production in Coswig received reinforcement in December 2022 in the form of a WFL MILLTURN machine.
As a developer and manufacturer for gear unit solutions, AUMA Drives brings decades of experience to the AUMA Group. AUMA’s company history dates back to 1896. It has been part of the AUMA Group since 1991. Before the company was called ‘GFC Getriebefabrik Coswig’ . The AUMA Group from Müllheim recognized the potential offered by the high-quality worm gear units from Saxony for its own product portfolio. The group took over the company, which was renamed GFC AntriebsSysteme GmbH. With the change of the company’s name to AUMA Drives, the integration into the AUMA Group was completed. It is thanks to Werner Riester that gear production was moved from Müllheim to Coswig. He had a special interest in specialised gear units, which is why there has been so much work and progress in this area.
The product life cycle is a unique selling point at AUMA. From the feasibility study through to disposal, every single stage is covered. The customer’s product idea is first taken into development, followed by the creation of a product concept before a prototype is then produced and analysed. Once quality and production planning are complete, it is on to parts procurement. Labelling and traceability are becoming increasingly important. Indeed, it is essential in CSP (concentrated solar power), because 80,000 drives are delivered in this area, for example. If three plants are not working in a solar field, traceability allows you to determine where these parts are so that you can repair and reinstall them. This provides transparency. “It all works using QR codes and is traceable,” explains Marko Kost, Technical Support Team Leader at AUMA Drives. “In case of a failure in the gear unit – e.g. a defective worm shaft – which is due to a material defect, you search in the corresponding material batch and know exactly which gear unit this affects and which ones have to be replaced. This is done for all standard products in the powertrain or according to customer requirements.”
The part is checked again at the installation stage to make sure that it is genuinely ready for outbound logistics. Then it is on to the final inspection and outbound logistics. Disposal is another important factor that is increasingly on customers’ minds (material decomposition, shredders etc.). “We are really proud to be able to say that we cover all aspects of this. We are also supported in this area by our management system. We are certified in accordance with the ISO 14001 environmental management standard,” says Kost.
Extensive range of products
Development, metal cutting, installation, testing and quality management are all carried out at AUMA’s Coswig site. “When it comes to hardware, we are essentially the development centre for the entire AUMA Group. We cover everything to do with the mechanics of the gear units,” explains the Technical Support team leader. The worm shaft, worm gear and housing are the most important parts made at AUMA (A items) and are located in the powertrain. This is AUMA’s main component and main area of expertise.
“Customized Solutions” is more than just a buzzword at AUMA Drives. Rather, it represents a promise to which all development steps are aligned. Because “customized solutions” require clearly structured processes in the design and development of gearboxes and drive systems – from the first project sketch to the finished product. The goal is a product whose performance and efficiency become a competitive advantage for the customer. With this claim, every customer project at AUMA Drives goes through several stages, all of which are carried out in-house.
The machines in the AUMA Group are developed and procured by a cross-group project team. In the case of the M40X-G, it was a project team consisting of the lathe specialist “coordinator and project manager” Mr. Jochen Pfeiffer from the AUMA Riester plant in Ostfildern, the production management and the shift leader for turning from Coswig, central purchasing at the AUMA Riester plant in Müllheim and Marko Kost, project manager for Coswig. The collaboration with Mr. Pfeiffer, who played a significant role in the success of the project, was crucial to the entire project.
Complete machining of large parts
AUMA is well positioned internationally. The Asian market is major focal point for the company, with a production plant there as well as in India and the USA. It even has an assembly plant in China. The market for escalators is particularly big in that region. AUMA currently has 32 machines in Coswig, including a complete machining centre – the M40X-G MILLTURN from WFL, in fact. Four-axis machining centres are used to manufacture the gear unit housings.
For the worm shaft, there is a dedicated turning area. “We have added to our arsenal here with a turning-boring-milling centre as a complete machining centre. We also have straightforward turning machines. We still use special gear-cutting machines for the further machining of the worm shafts. The only way to achieve the required level of quality in the gear tooth profile is through grinding, and we use a grinding machine to do this. We turn the worm gears and machine them further on a gear-hobbing machine,” explains Kost. All machining steps for the components except the blank shape and heat treatment stages are carried out in Coswig.
The worm shafts are produced on the WFL machine. AUMA’s high-performance worm gear units can be found in concrete mixing plants, among other applications. Kost provides an insight into the original machining process: “The process for manufacturing this shaft part used to involve a lot of individual steps: turning, clamping, pre-machining, pre-milling the gear teeth – grinding the gear teeth is an extremely expensive process. Then it was time for the heat treatment: the part has to be annealed because the milling and turning process sometimes causes the shafts to twist. After that, it was on to the finish milling of the shafts. We would pre-grind the gear teeth and finally carry out the heat treatment and case hardening before re-clamping the shaft on the turning machine. Both sides were turned and slots were then milled before moving the part to yet another machine for the finish grinding of the gear teeth. Finally, we carried out the finish grinding of the seats externally in the cylindrical grinding machine. That’s a lot of individual processes with an extremely long lead time.” With the new machine from WFL, the worm shaft can now be pre-turned completely in just one clamping operation. The gearing is pre-machined, which means that there is no longer any need to pre-grind them. The shaft goes from the machine straight to case hardening. Once this has been completed, the rest of the machining process, right through to the finished worm shaft, continues in the M40X-G.
Other than the case hardening, the finish grinding of the gear teeth is the only remaining process still carried out on another machine. All other processes are carried out on the WFL. Kost is delighted with the savings that they have already made: “We have reduced the set-up time by 50%. The machining time has been reduced by 15–20%, but we can see more potential here. The lead time has been halved. We still have the external hardening process, which sometimes prevents us from being flexible. But thanks to the WFL, in theory we can now theoretically deliver within four weeks if a super urgent order comes in.”
Securing a competitive advantage
The machine is designed specifically for the worm shafts, but there are already plans under way to machine the sleeves that are fitted in the gear unit. These sleeves provide the output drive in the gear unit. At AUMA, the customer chooses the output drive. “For example, we can install a shaft, but the holes are often specified by the customer. We have already done this with internal gears too – we are very much guided by the customer in this area. But as for the gear unit itself, the diameters and so on, we stick to the standard,” says Kost. When it comes to the range of parts in general, Kost tells us that the development and design teams are delighted too: “It’s a big win for them as well, as they can include elements in their new developments that wouldn’t previously have been technically possible. And as long as that production stays in house, then it means a competitive advantage for us as well.”
Batch sizes from 1 to 24 are produced by AUMA at its Coswig site. “Due to the small batch sizes, it was extremely important to us that the machine is easy to set up. That’s why we have a large tool magazine, so that we can set up parallel to machining time. In the past, we would frequently have to change the jaws due to the jaw chuck. Now, we have the same jaw chuck on the main and counter spindles. We sometimes use face drivers for special machining during the high-precision finishing process, and we can attach these face drivers to the jaw chuck so that we are under way in no time,” says Kost. It was important for AUMA Drives to have a suitable machine to produce worm shafts and sleeve components. The WFL MILLTURN was able to fulfill this.
This is what complete machining can do
When you talk about automation nowadays, that actually already exists in the form of complete machining. The operator simply presses the start button and we then get a complete, finished part at the end of the process. So that was already a straightforward piece of automation for us. It’s not just the professional analysis of the parts production process that impressed, however. “We were extremely excited about the performance – about what the machine offers in terms of machining performance. And the fact that we didn’t have to make any compromises on accuracy. We have a very narrow tolerance range, in some cases down to IT6, which we now machine completely using the in-process measuring probe by means of turning. We used to always be told that we had to grind to achieve this, but actually we can get the same result by turning. That’s a massive competitive advantage for us. And of course the design with the slant bed – that’s critical for stability.
Measuring in the machine
The M40X-G is also equipped with a pick-up magazine for the grinding unit. This can also be used for boring bars later on. Kost sees this as a huge advantage: “We used to use parameter software to help us produce the gear teeth on the shaft. The operator entered the data, but this was a big challenge for us because you always had to draw the tooth when programming and then simulate it in the programme. WFL has developed a specific programming cycle for us for this process, so we can now programme the gear teeth directly at the machine. You simply enter the gear teeth data and then mill or turn. There is no longer any need for external programming. The whole process runs extremely smoothly. It really was a fantastic collaboration. We can also measure the gear teeth with a measuring probe and then finish them.” AUMA uses the machine’s measuring technology to do this. The shaft’s concentric running is also measured on the machine without turning the shaft. “That’s really great, because the part can stay in the machine the whole time,” says Kost.
All data at a glance
AUMA uses WFL’s 3D simulation software CrashGuard Studio for simulations. CrashGuard (a patented collision prevention system) is used on the machine to prevent collisions. TopSolid is used for programming at AUMA as it has been in use for a long time and employees are extremely familiar with the software. Nevertheless, due to the small batch sizes involved, the company wants to find a way to simplify the procedure so that the operators at the machine can respond to certain processes. Kost explains the problem: “When you have an external CAM system, it is always difficult because the operator can’t make any further changes to the machine’s program at that stage. That’s why we want to find a solution that will enable the operator to programme at the machine control system. For example, if they want to change three stocks to two.” AUMA uses a wide range of tools for digitalisation. For example, the company tracks the energy consumption of its machines. As for future projects, Kost already has a few ideas: “We definitely want to make further progress with programming and simulations, as that will save us run-in time. We need to be using the machine efficiently. Also, three machines are going to be removed from the production area in Coswig thanks to the new M40X-G. There is a growing space for machines that come with automation. And everyone always needs space. We are also expecting to grow. I can well imagine doing more of our work with complete machining centres and getting rid of the special machines. That will save a lot of time. Above all, it is important to have a reliable partner, and we know without a doubt that we have that in WFL.”