Milling down to the finest detail
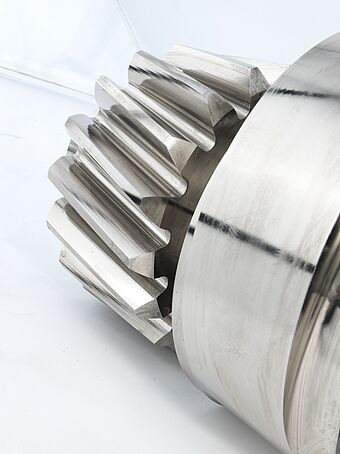
For many years now, DESCH has been a keen advocate of the concept of complete machining. Using a machine park that already includes eight different MILLTURN complete machining centres, drive solutions are designed and produced for a wide variety of machining industries. Components for driving presses and switchable couplings through to highly complex specialised gearboxes, or even large gear units for rolling mills and smelting works, are just a few of the typical applications that DESCH is currently manufacturing.
DESCH GmbH & Co. KG has been run by the Desch family since it was founded in 1906. The company is busy all over the world in modern machine and plant engineering applications, yet remains proud of its roots in the Sauerland. DESCH is seen as the drive engineering specialist that delivers innovative, customised complete solutions for the entire drive train.
The DESCH Group employs more than 450 people worldwide and has a reputation for the highest levels of quality and first-class service. The company is well ahead of the pack in the relevant markets in Germany and Europe and is growing strongly with new premises in Canada, the USA, China, Brazil, Italy, and other
developing markets. In 2019, DESCH took the next big step towards the future by establishing an important strategic partnership with the Nidec Corporation and its subsidiary, the Nidec-Shimpo Corporation of Kyoto, Japan. Strengthened by their strategic partnership, DESCH and Nidec will play a leading role in drive
technology in Europe, particularly in the field of mechatronic system solutions.
A wide range of products and an extensive service offering address the drive technology requirements at the interface between the drive and the machine. The company develops and produces planetary and special gearboxes, press drives, plus innovative coupling technologies for modern machine and plant engineering applications. Wherever high levels of power and force need to be transmitted, DESCH drive technology will be equally at home in asphalt milling on motorways or in crusher plant in quarries. DESCH drives power rudder propellers in ships, swivel ultra-precise parabolic antennae and are widely used in machine tools and agricultural machinery. The company is also developing pioneering technologies, such as drives for the tidal power plants that convert sea currents into electrical energy.
The DESCH product portfolio has changed over time, becoming steadily more complex and technologically demanding, thus paving the way towards complete machining. The overriding objective of DESCH was to manufacture highly sophisticated small series in a cost-effective and reliable manner while keeping lead times to a minimum. Which is why in 2013 contact was established with WFL Millturn Technologies. It all began with a meeting between WFL regional sales manager Reinhold Wieland, former production director Detlef Ebert and Dirk Müller, who was manufacturing manager at the time. „Among the standouts for us as far as WFL was concerned were how sales dealt with the project management and the technological execution on the machines. The projects were implemented very quickly and accurately,“ noted production director Dirk Müller. Three different types of machine, posing various technological challenges, were installed in the factory and up and running within a year. The technology was tested and run in at the same time as the installation at the Millturn Innovation Center in Linz before being implemented in the machines on site. Reinhold Wieland fondly remembers the exemplary teamwork at all stages of the project: „Everything ran so smoothly, from planning right through to implementation and production. Above all, we were able to satisfy the challenging quality requirements.“
Applications in the „MILLTURN machine park“
Crankshafts for presses or pumps, enclosures for machine tools, couplings or centrifuge gearboxes, drive and output shafts for construction equipment, ships and machine building: they are all produced on the MILLTURN machines at DESCH. The manufacture of gearwheels, which are primarily found in planetary gearboxes, pump drives or synchronously driven construction machinery, is another application area.
Manufacturing batches on the various machines range from 1-50 parts. By far the largest share is made up of batch sizes of 1-5 parts. Manufacturing times were reduced by as much as 70 %. „The MILLTURN concept and its supporting slogan „Clamp once – Machine complete“ were totally justified,“ comments a delighted Dirk Müller. In particular, the number of clamping operations and the alignment overhead were reduced significantly, which had a positive impact on the quality of the components. This in turn led to a marked improvement in geometrical and positional tolerances. Lead times and wait times were reduced to one sixth of their previous levels.
The accuracy of the machines came under close scrutiny when deciding which one to choose, as it was going to be equipped with an extremely precise measuring system and the corresponding software. The highest levels of quality had to be achieved, both in the production of single parts as well as with small series of differing workpieces, using all possible technologies. A great deal of importance was placed on the high-quality finish of the machine. Other factors, such as ease of maintenance, accessibility to the machine and the visibility into the working area, also played a key role in the purchasing decision. Last but not least, the many years of experience in complete machining was another decisive factor behind the decision to buy the WFL MILLTURNs.
DESCH now has a total of five MILLTURN models in use in a number of factories at its Arnsberg site. The last four machines were acquired in 2018 to increase capacity, particularly for the manufacture of gearboxes. A new production site has just been created. The machines were purchased on the basis of component classes (sizes) and the required capacities. “Our current machine park allows us to react flexibly to the market,“ says Dirk Müller.
Gear cutting technology
At present, the MILLTURNs are mainly used for the manufacture of spur gears and cylinder wheels. Even as the machines were being purchased, additional software options and technological features were being considered to enable other geometries to be produced in the future. For example, the InvoMilling method makes it a simple matter to modify the gear cutting. The whole process is much more flexible compared with using a gear hobbing cutter. The technology available with a MILLTURN complete machining centre facilitates powerful cutting to the highest levels of precision. In addition, the full spectrum of cutting tools can be utilised, leading to the development of new machining strategies.
Desch uses the TopSolid 7 CAD/CAM system as well as WFL‘s own CrashGuard Studio package, which allows the sequence to be simulated before machining commences.
The Service clinched it
Another reason behind the decision to buy the machines was the fact that there had already been many positive experiences with WFL Service. „Super-fast response times, easy to get hold of, good communications, the technical people in the internal and field sales teams, and the excellent availability of spare parts were important factors that put the icing on the cake. The solution-oriented working method means we‘re in good hands over the entire life cycle of a MILLTURN,“ observes Dirk Müller.
Process reliability through automation
The DESCH Group utilises the most modern machining strategies and is pressing ahead to increase its production capacity and efficiency. The development and extension of all DESCH subsidiaries is intended to pursue the common target around the world of focussing even more on complete drive and system solutions. All production acilities are being significantly and continually upgraded with the most advanced machines to meet the differing requirements of series and one-off manufacturing. „Automation is very important to us. In the first stage we intend to concentrate on the automation of our small series, for instance on parts with a high degree of repeatability,“ concludes Dirk Müller.
ALWAYS-ON – ENDLESS MANUFACTURING POSSIBILITIES:
In its modern production locations in Europe, North America and Asia, Desch is additionally offering a broad performance spectrum in the field of toll manufacturing and the manufacturing of customer specific components. The portfolio includes:
- Turning/multicutting
- Milling/boring
- Grinding
- Gear cutting
- Grooving/balancing
- Measurement technology
- Robots for small component series