Pushed to the maximum
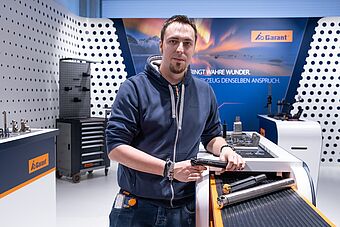
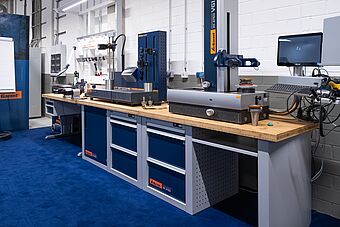
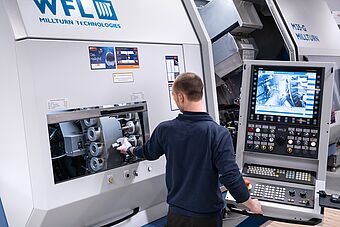
With over 4,000 employees and an extensive range of tools, operating equipment and personal protective equipment, the Hoffmann Group is one of the major players in the industry.
In 2019, its parent company, Hoffmann SE, celebrated its 100th anniversary. The first WFL Millturn complete machining centre was also commissioned last year at the Hoffmann Group. This machine takes on a highly unconventional role – rather than producing components, it is used to test and optimise tools. These are ruthlessly pushed to their very limits. The result is a huge amount of chips and valuable tool data.
Everything revolves around the catalogue
“We don't make tools in this department, they are developed in conjunction with suppliers,” explains Dr Jens Rossaint, Director Engineering, who is responsible for the Technology department and therefore the quality management of products developed for the catalogue. This is extremely important, as the catalogue is key at the Hoffmann Group. The orange ‘tool bible’ has been published annually since 1978. It is available in 18 languages and now comes in four volumes with a print run of 900,000 copies. In 2000, an online version with over 90,000 items to choose from was also launched with the eShop.
“The process for including a product in the catalogue typically goes like this: we define what the tool should be able to do, draw up a specification, integrate technical ideas. Then there’s some kind of tendering process and we narrow down the number of suppliers to a shortlist. These then manufacture prototype tools. This is followed by testing, a comparison with competitor products and benchmarking. The tools are then continuously developed by the supplier. These tools are then only found at Hoffmann in this manner. After testing, the new tools gradually enter the catalogue. We mainly sell standard tools. But we do offer a few special tools too,” summarises Rossaint in regard to their workflows.
Targeted development in the TechnologyCenter
The TechnologyCenter in Munich, opened in September 2019, has been equipped with extensive measurement and testing equipment as well as numerous demonstration and training facilities. In addition to the measuring room which features a coordinate measuring machine, all conceivable analytical equipment, from a hardness tester to a scanning electron microscope, is available for scientifically examining the properties of the tool’s structure. Ultimately, the question is why might a tool be good or bad? The structure allows conclusions to be drawn about the performance and durability of a tool. “We’re not interested in blind trial and error, instead we want to take a targeted approach to development and optimisation,” explains Rossaint. Alongside laboratory equipment, the Munich TechnologyCenter also features operating equipment from the catalogue, which clearly demonstrates the optimum way to set up the machine environment.
If customers want to see specific tools live in action, they can sign up for this through field sales. “We then arrange an appointment with the customer and field sales and define what the demonstration will cover,” explains Thomas Grünberger, an expert in machining and additive manufacturing. In addition to material-removing methods, there is also a lot of focus on additive manufacturing here. Customers can visit the TechnologyCenter individually with members of the field sales team. However, more come to take part in training sessions and the regular ‘get together’. The latter is less about drinking beer and much more about meeting up with experts and specialist talks on tools. Several Hoffmann Group employees also frequently participate in training sessions and familiarise themselves with the catalogue products at the centre. The training rooms where the theory is imparted are located close to the TechnologyCenter where visitors can see everything live in action on the machine. The training sessions always include a practical component. And this is where the new WFL Millturn takes centre stage. In addition to the turning-boring-milling unit with B and Y-axis, the counter spindle machine is also equipped with a tool turret on the lower system. This means the machine can perform simultaneous turning on both spindles or perform 4-axis turning on one spindle. Five-axis machining is also possible with the turning-boring-milling unit and the C-axis. Thanks to a steady rest on the tool turret and a tailstock function for the counter spindle and tool turret, longer shaft components can also be machined. Transfer to the counter spindle means that parts can be fully machined in just one clamping operation. Thanks to a Hainbuch Centrotex quick clamping system, various clamping devices such as chucks or clamping mandrels can be changed over in just 20 or 30 minutes and the machine can be flexibly adapted for the task at hand.
Easy programming on the machine
Programming is carried out with a CAM programming system. Easier programming jobs are completed directly on the control unit using Millturn PRO, a proprietary WFL programming editor. “We also like to use this for specific tasks,” says Thomas Grünberger. “We want to make really great show parts with it. With the tool turret and turning-boring-milling unit also in use at the same time, of course. And we also have the driven tools on the tool turret. We want to push the machine to its limits.” If tolerances are very tight, a Renishaw in-process measuring probe is also used. A whole range of WFL measuring cycles are available for this.
Tests with large inserts also possible
The Hoffmann Group needed to be able to test as many different tools and technologies as possible. It was also important that newly developed tools could be represented in the machine. Another requirement was that the company’s own software developments – particularly for tool management – could be integrated into the machine and that they could build upon existing software solutions for future developments. Willingness to work together with the machine manufacturer is essential here. “It’s a huge advantage to also be able to test large inserts without immediately bringing the machine to its knees. The highly flexible clamping options mean that we can also use larger diameters with ease, to extend the test ever further, obtain even more data and carry it out for a suitable length of time with a high level of machining performance. Ultimately, it gives us the means to test tools more efficiently. With the WFL, we can now perfectly test HSK-63 turning tools and thereby optimise our product portfolio. The B-axis is also a huge plus during turning, as we have great flexibility for adjusting the entering angle. When our field sales staff come back with various customer requests, we can reproduce practically any situation, from VDI40 on the tool turret to any tool in the turning-boring-milling unit at any possible angle. The milling spindle was designed for 16,000 rpm, so we are also well equipped for future requirements.” Since the start of the year, almost 400 customers have visited the machine. The field sales staff also take frequent advantage of the practical testing opportunities with customers. The WFL is a real attraction. A whole bunch of visitors are standing round the machine right now.
Looking ahead: grinding
Grinding with the machine has not been looked at yet. The machine is prepared for this, but it is not currently a primary focus. However, the relevant experience can now be gathered at any time. “Our role is to advise the customer throughout the entire machining process. If the trend for integrating grinding in the turning-milling process picks up momentum, then we are able to fully reproduce this process on the machine at any time. With this machine, we are also able to test our entire portfolio of tools from the catalogue,” explains Rossaint.
Industry 4.0 included
Rossaint also has big plans when it comes to connectivity. “It’s about integration into our CM software – Connected Manufacturing.” This is used to record and evaluate spindle data in real time. This is also of interest in regard to the tool life. The machine is equipped with an OPC UA interface for transferring the data, which means it is ready for any additional IOT solutions that may arise in future. “The machine offers a lot of functions that we haven’t worked with yet.”