Technological versatility in a class of its own
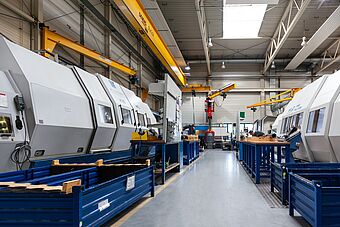
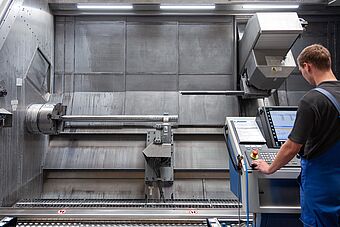
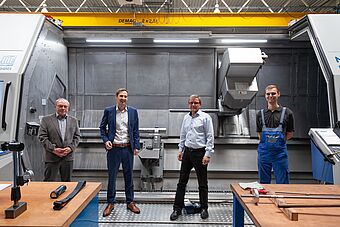
With its 28,000 inhabitants, the town of Meissen in the German state of Saxony is best known for being home to Europe’s oldest manufacturer of porcelain. But it is not only the production of the finest porcelain that defines Meissen; the surrounding area also has plenty to offer in the way of industry.
Kersten, the specialist mechanical engineering company, was established in 1965. After the German reunification, the company ran with two small milling centres and 12 employees, and over the years, the production of parts and components developed into the main area of business. In 2004, the company moved into a newly acquired office and manufacturing facility in the Niederau industrial estate. It was at this time that first contact was established with WFL Millturn Technologies, at which point Kersten Maschinenbau transitioned to complete machining. The first M65 MILLTURN from WFL entered service at Kersten Maschinenbau’s manufacturing facilities back in 2006. It is used primarily for the production of shafts, generators and gearbox parts for the wind power industry.
Range of parts ‘without limits’
Kersten Maschinenbau mainly supplies customers in Germany, Austria and Switzerland, however, the parts that are manufactured here can be found all around the globe. Customers range from mechanical engineering (e.g. electric machinery) companies, generator and motor production companies, rail engines, coupling and gear manufacturers to printing press manufacturers. As a result, there is a constant demand for Kersten products from companies such as textile machine manufacturers, plant manufacturers, measuring technology companies and special machinery manufacturers. “This broad range ensures both flexibility and security,” says Udo Kersten, CEO of Kersten Maschinenbau. “As a supplier, we have a wide range of customers, which means that we deal with an extremely diverse range of parts. To manage this, we have a high degree of vertical integration with cutting of blanks, welding, heat treatment and assembly of components. Three high-precision coordinate measuring machines ensure that all manufactured parts can also be measured and dispatched with records. The mechanical departments comprising turning, drilling, milling and complete machining as well as grinding with cylindrical and surface grinding machines form the core of the manufacturing process. All our machines feature various options so that we can react with maximum flexibility when presented with new customer workpieces,” adds Udo Kersten.
The world of complete machining
Currently Kersten Maschinenbau has four MILLTURN machine models in use. One of the latest additions is the M80X MILLTURN with a 4500 mm centre distance. Quite simply, flexibility and precision were the main requirements for the new model. Starting with the pick-up magazine, a self-centring steady rest with a large clamping range, through to the extended X-travel, it covers the widest possible variety of machining options. Other requirements included stability, multiple technologies and high accuracy. However, the flexibility to use a wide selection of tools in the machines was also of particular importance. As a result, MILLTURN impressed with its excellent tool handling using the large number of standard tools (up to 900 mm in length) and the ability to accommodate large boring bars using the prismatic tool interface.
“The versatility of the prismatic tool magazine and the generously dimensioned tool changer provide us with many options here,” explains Udo Kersten. “On top of that, another major concern was the large Y-travel. Ultimately, however, it was the overall concept or package, which had already shown its worth in previous years, that was once again decisive.”
“All MILLTURN models are currently designed for shaft part production, although the machining of chuck parts is also possible. We are currently focusing on the machining of shafts, rollers, bushings and bores. These workpiece groups are mainly run on the MILLTURNs – the different turning length options were important to us,” Udo Kersten comments. The smallest complete machining centre, a M50 MILLTURN, with a turning length of 3000 mm, optimally fulfils the requirements for the parts to be machined on it. The reinforcement on the side of the internal machining options played a major role in the last purchase decision. A specially damped system boring bar for vibration-free finishing was also included in the acquisition of the M80X MILLTURN. This enables automatic tool head change at the boring bar tip, making it possible to machine complex internal contours. The longer the boring bar, the more Z-travel is needed. The M80X MILLTURN with 4500 mm machining length met this requirement and enables the use of vibration damped boring bars up to 1700 mm long and weighing 200 kg. Compared to the standard M80 model, the X-stroke of the M80X has been extended by 150 mm giving a total of 1050 mm. The longer X-stroke enables the use of longer tools, especially for deep cross holes.
Currently, textile industry components are being produced on the M80X MILLTURN, specifically the workpieces for yarn production in textile machines. “Here we produce workpieces with long, slim boring bars that have very high accuracy and run-out requirements. A particularly high standard of internal contour machining is also required,” concludes Udo Kersten. At the end of 2020, the M80X MILLTURN began producing components for yarn winders.
Technological flexibility
From a technological point of view, we can perform any kind of mechanical machining, including internal grooves, serrations and gears. External gears are milled, and the internal gears are punched. When it comes to gear milling, the advantages of the MILLTURN milling unit concept with a high-torque gear shaft come into their own. On the one hand, when pre-machining with large tools, it provides a very high torque combined with high power, while on the other hand, the high speeds during finishing of the gears ensure short machining times. The technologically optimal torque power curve of the milling unit ensures perfect cutting conditions in every speed range. Combined with WFL’s FLANX gear cutting software, this results in an extremely flexible and efficient solution. A slotting tool with an 800 mm deep nut, developed in-house by Kersten, is used on the M50 MILLTURN. “The stability of the MILLTURN machines means that we can keep trying and implementing things like this. These machines have such great stability that they are a natural fit for such applications.”
As a supplier, both the range of workpieces and the batch sizes can vary. The most common batch sizes are between 20 and 100 pieces. The company therefore focuses on flexible and customer-specific order processing. Kersten Maschinenbau can basically cover everything from individual pieces to large batches.
The two most recently acquired machines, the M50 MILLTURN and the M80X MILLTURN, marked an expansion of the plant’s machinery. Since 2013, an M120 MILLTURN with 6500 mm turning length has also been working reliably in a three-shift system. To date, no machine has been decommissioned. The purchases always involved an expansion of capacity, but also with a view to exploiting the additional technological potential of the newer machine models. “Technological progress was important to us here. It is crucial that we are always at the cutting edge of technology,” concludes Udo Kersten.
From programming to production
The programming and simulation of the workpieces is carried out at Kersten using TopSolid CAM. WFL provides 3D models of the machines which can be virtually mapped in TopSolid CAM. The existing postprocessor serves as a link to convert the TopSolid CAM programs into ISO codes required by the control system. Two programmers are currently working on the MILLTURNs.
Many different factors are required in order to run a simulation accurately: the machine model, clamping devices, the blank or component data and tools. Kersten has been working on a major digitalisation project for some time now. As part of this process, the entire tool organisation is optimised in order to have all the necessary 3D models available. The challenge here is to capture more than 20,000 tool items, from which about 150,000 variations of complete tools can be generated. Kersten is currently making excellent progress in digitising tool data. In the CAM system, the 3D digitised tools can then be loaded, and the simulation created in the program – this means genuine added value.
Indispensable
Complete machining ensures higher accuracy and eliminates reclamping errors. The complexity of the workpieces is increasing and can be better reproduced by this type of machine. Five different axes can be used for machining and interpolation in a single clamping. Lead times are shortened, idle times are eliminated, storage space is saved and ultimately the throughput becomes faster and more efficient. “We have been won over by the numerous benefits of complete machining ever since we purchased our first complete machining centre in 2004. We have clearly seen that it has major advantages over conventional manufacturing,” concludes Udo Kersten.