The finishing touches in production
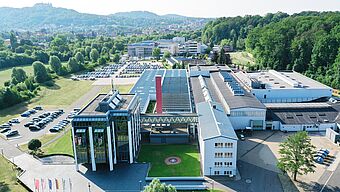
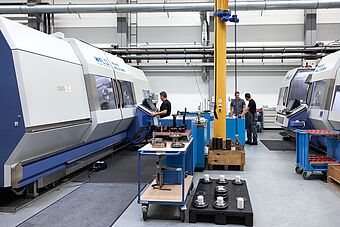
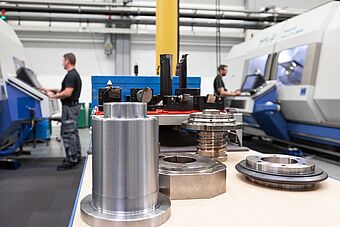
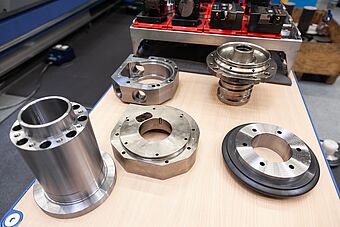
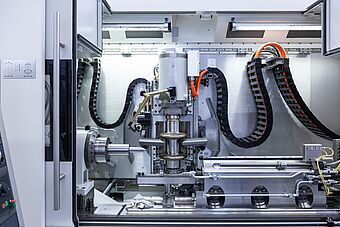
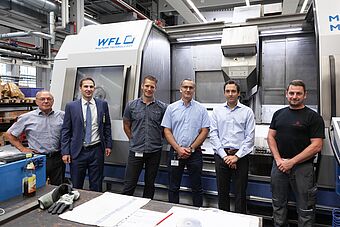
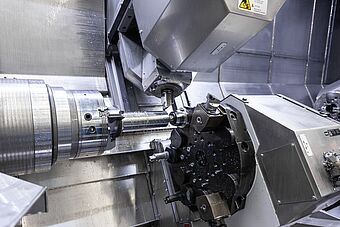
Traditional company Kapp Niles has been in existence for more than 120 years. From its inception, Niles focussed on the development of gear finishing machines and has built up extensive expertise in this area. Bernhard Kapp founded “Kapp & Co.” in 1953 and the two companies merged to form a Group in 1997. As early as 1980, the portfolio was extended to include the production of grinding tools and since 2017 the company has been producing its own measuring machines. The company will soon be managed by the third generation of Kapps: Michael and Matthias. Kapp Niles has nine production sites throughout the world and the Group employs just under 1000 members of staff.
Traditional company Kapp Niles has been in existence for more than 120 years. From its inception, Niles focussed on the development of gear finishing machines and has built up extensive expertise in this area. Bernhard Kapp founded “Kapp & Co.” in 1953 and the two companies merged to form a Group in 1997. As early as 1980, the portfolio was extended to include the production of grinding tools and since 2017 the company has been producing its own measuring machines. The company will soon be managed by the third generation of Kapps: Michael and Matthias. Kapp Niles has nine production sites throughout the world and the Group employs just under 1000 members of staff.
International presence
Typical Kapp Niles applications are found primarily in the automotive and aviation industries. The larger grinding machines are supplied to the mining, wind energy and rail sectors, among others. Europe and Asia represent its main markets. The company’s main products are grinding machines, profile grinding machines, measuring machines as well as grinding and dressing tools. These enable the grinding of workpieces with a diameter of 8 to 8,000 mm and a length of up to 2,200 mm. Special machines on which high-precision aviation components and screw rotors are machined represent a large market segment. It is details like these that make Kapp Niles and its machines stand out and are considered the company’s unique selling point.
The complete package
“Maximum accuracy and optimum surface quality play a central role at Kapp Niles and are the most important features required of our machines,” says Michael Kapp, Production Director for the Group. Strength is a hugely important property when it comes to gear teeth. Once the workpieces have been hardened, they can be ground in the Kapp Niles machines. Reproducibility is another key requirement. Kapp Niles is a system supplier that offers not only grinding machines but also the corresponding tools, technological expertise and coordinate measuring machines, thereby giving its customers real added value.
The company places huge emphasis on service: Kapp Niles covers everything from the overhaul of machines to repairs as well as conventional services, in an effort to increase customer benefits. The motto at Kapp Niles is: The first machine is sold by Sales, the second machine is sold by the service. The concept of digitalisation is becoming increasingly important, and a new user interface (KN grind) with optimum user-friendliness has been integrated into the new generation of grinding machines. The machines are able to network with one another and feature a closed loop connection to the coordinate measuring machine, which issues correction instructions directly.
Around 450 members of staff are employed at the site in Coburg. Around 60 of those employees work in production over two shifts. In 2014, some of the production at the Coburg site was moved to a large new building, where two MILLTURN complete machining centres were installed. To be more precise, these are two M40-G MILLTURN complete machining centres with a machining length of up to max. 2,200 mm.
Complete machining on the increase
The machine concept of complete machining is not new to Kapp Niles. According to Sascha Forkel, Head of Cubic Machining, this concept was introduced around 15 years ago and has since had a huge impact on production as a whole. Back then, the advantages of complete machining were already clear to see. This insight lead directly to the investment into two complete machining centres. These years of experience played a key role when it came to replacement investment. The search was on for a counter spindle machine with tool turret. Based on a market analysis and a detailed investigation into possible suppliers, the company finally opted for WFL. “We chose the machines that made the greatest impression on us in terms of quality, and these were the MILLTURNs from WFL,” says Michael Kapp, Production Director at Kapp Niles.
The machines Kapp Niles was using at the time had reached their limits with some machining tasks. With the MILLTURNs from WFL, the full performance potential of the tools can now be fully exploited, including reserves. The machines are currently also achieving the desired quality in hard turning.
Impressive stability, quality and reliability
“When purchasing the machines, our primary concerns were to increase productivity, stability, accuracy, reliability and availability. “We are working on the assumption that we will be using the machines for much longer than 10 years,” says Sascha Forkel. The slant bed concept and the compound slide structure of the MILLTURNs from WFL ensure long-term stability and accuracy. Unique to the market is the mechanical turning-boring-milling unit, which boasts unrivalled performance and its minimal interfering contour. This structure allows short tools to be used, thereby achieving maximum accuracy and material removal.
Another reason for purchasing the machines was the service that is included. We asked around and received excellent references for WFL. “The longer service life of a MILLTURN in comparison with other complete machining centres was what ultimately convinced us to purchase the machines,” continues Sascha Forkel.
The two MILLTURNs are now being used to produce the most diverse range of components for Kapp Niles grinding machines, such as spindles, tool bodies, bearing housings and further machine components. While the previous machines were incapable of carrying out hard turning with the required tolerance, the new machines are now producing reliable results. “In terms of both machining and tools, there is still huge potential,” says Michael Kapp.
From commercial and technical aspects, right through to software considerations during order processing, the entire process was watched over by a competent WFL Project Manager. This meant that all issues and concerns could be dealt with quickly, much to Sascha Forkel’s delight.
“The MILLTURNs from WFL are the latest machines to arrive at Kapp Niles and will also be the first to be automated. “We can be confident about upgrading these machines in the near future, because as well as receiving everything from a single source, we also feel safe in the knowledge that everything will work as it should,” concludes Sascha Forkel.
Uncompromising efficiency
The two M40-G MILLTURN machining centres are used to produce various parts for Kapp Niles grinding machines, including a wide range of flange and shaft parts. They produce workpieces that are particularly rotationally symmetrical. “Many of the components for our machines are machined on the MILLTURNs,” says Michael Kapp. The MILLTURNs have also optimised machining times, as the machines are more powerful and ultimately more stable. All programs are currently being rewritten and transferred to the MILLTURNs. The company is hoping to make even further advancements in terms of production efficiency in the near future.
At Kapp Niles, programs are created externally using CAD (Siemens NX). Before the program is transferred to the machine, all processes are documented and simulated. Two employees are currently responsible for programming a wide range of workpieces on the two MILLTURNs, and also for calculating new clamping situations and making machining as efficient as possible.
Focussing on the details
The full machining lengths and diameters offered by the two M40-G MILLTURNs are being utilised. “The portfolio of workpieces ranges from coffee cup size to the maximum turning diameter of 520 mm,” explains Sascha Forkel. The heart of the machine is the turning-boring-milling unit with X-, Y- and B-axis, with an output of up to 33 kW and a torque of up to 214 Nm. “The design of the milling spindle with 12,000 revolutions per minute enables the efficient use of very small tools and meets all of Kapp Niles’ requirements,” emphasises Bruno Reisbeck, Regional Sales Manager at WFL. The left-hand turning spindle was specifically designed for the toughest machining tasks and, with an output of 54 kW and a torque of 2,000 Nm, delivers the required degree of productivity during turning. The right-hand turning spindle is equipped with a highly dynamic, integrated spindle motor with a maximum output of 33 kW and torque of 550 Nm. In order to guarantee the necessary machining performance, tool life and process stability in the case of very hard and difficult to machine materials, the machines feature 150 bar coolant pumps. These ensure good chip breakage and optimum cooling of the cuts as well as a longer tool life. On the lower slide system, a 2x12-position disc turret with driven tools reliably goes about its work. The upper and lower system can be used on both spindles or on one spindle simultaneously. A decisive factor in productivity is the large swing of 350 mm above the tool turret, which enables even very large parts to be automatically transferred to the counter spindle. Due to the enormous versatility and machine options, it soon became clear that the M40 variant with counter spindle was the right choice.
Digitalisation gains ground
Data recording is becoming an increasingly important topic. The ability to network is essential: thanks to the large volume of generated process data as well as the availability of data on machine status, the machines are perfectly equipped for the future. The iControl process monitoring guarantees extremely reliable processes, which is an important prerequisite for future automation solutions.
WFL also offers an extensive range of automation solutions that it has developed in house. The foundations have therefore already been laid for future success.
Kapp Niles fact box:
|