The global technology leader focusing on complete machining
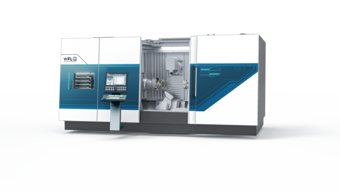
WFL Millturn Technologies GmbH & Co. KG, headquartered in Linz, Austria is the only manufacturer in the world to focus exclusively on the production of multifunctional turning, drilling and milling centers. Today the MILLTURN brand is synonymous with manufacture of complex components with the highest precision required for critical applications like aerospace. The modular structure of the MILLTURN centers as well as individual special solutions guarantee perfect adaptation to the respective production task. A wealth of experience spanning over three decades in complete machining, and thousands of tasks completed guarantee WFL customers the most efficient and reliable machines. India is a very important market for WFL. Naturally the company has taken several measures in the past few years to strengthen its sales and service activities in India, reveals Günther Mayr, Managing Director-Sales & Technics, WFL in an interview with Machine Tools World. Excerpts:
WFL is a renowned name in the machine tools industry. What’s your standing and niche in this highly competitive field?
Having focused on complete machining since 1983, we are the technology leader in the field of metal-cutting production machinery. The combination of different machining technologies such as turning, milling, drilling or grinding in one machine tool is known as complete machining. Clamp once – machine complete: this goes hand-in-hand with enormous economic and production-related advantages. It is applicable for part types that were previously manufactured in several process steps on various different machines.We have been building complete machining centres for well-known customers in the aviation, automotive, engineering and plastics machinery industries. With a ratio of exports of 95% and sales branches and distribution partners in all major industrial countries, we achieved a record-breaking turnover in 2019.
What makes your MILLTURN machines all-in-one and exemplary?
Complete machining is about maximum quality, maximum flexibility, highest degree of utilisation, short lead times and highest level of productivity. Complex machining components are manufactured to the narrowest tolerances and with minimal clamping. In-process measurements guarantee and maintain existing levels of precision and stability. Shortened setup times and a reduction in clamping devices and special tools increase flexibility in terms of machining options. This allows for an efficient manufacturing process and technological optimisation. Several important factors come into play in achieving an increase in the degree of utilisation. Minimal clamping and few internal transport movements increase the efficiency of the production process significantly. Lead times are minimised due to short wait and handling times. The combination of maximum quality, maximum flexibility, maximum utilisation and short lead times results in the highest possible level of productivity.
You have a plethora of jobrated models. Which are the different types of machines and what’s the basis of the right selection by the end-user?
An enormous technology spectrum is covered by the possibility of interpolating the NC-axis B, C, X, Y, Z. Which makes complete machining by turning, drilling, milling, deep hole drilling, OD- and IDsplining, turn-milling and many more operations without manual interventions a reality.
Perfect adjustment to the machining task allows for ultimate productivity with minimum investment costs. The consistent WFL modular concept guarantees flexible standard solutions even for individual requirements and high precision complex workpieces. We currently have over 20 different MILLTURN models available: With turning lengths from 1000 to 14000 mm and turning diameters from 500 to 2000 mm, an extensive range of workpieces can be machined completely. Almost all MILLTURN models are also available as counter spindle variants (with the identification – G).
At WFL, we develop tailor-made technologies and cycles to satisfy specific customer requirements. Any machining technology can be performed on a Millturn – from deep-hole drilling to gearing.
It is not a coincidence that our customers are among the leading producers in numerous high-tech sectors. Components for aircraft, turbines and vehicles –to name but a few – are manufactured from metallic raw materials (cast iron or forged parts).
Whenever highest standards are required there is no better choice than a MILLTURN.The scope of use of MILLTURN turning-boring-milling centres is virtually unlimited. Thanks to our experience, we offer unequalled knowhow in application technology in addition to its mature machine concept.
Which are the industry segments and critical applications you cater to?
We have been building complete machining centres for various well-known customers in the aviation, engineering and plastics machinery industries, among others. The aerospace industry represents an important market segment for us. More and more materials, which are hard to machine are becoming prevalent in this sector. The most important requirement our products must satisfy is absolute process reliability.
Landing gear, turbine shafts, fuel pump housings and other aerospace components require technological solutions that have been specially adapted. The objective here is to ensure that machining is economical. Therefore, the advantages of complete machining are particularly illustrated in this sector. Thanks to the broad technological spectrum of the multifunctional turningboring-milling centres and decades of experience, our customers can rely on the highest levels of productivity.
Complex geometries and difficult materials are also features of the key components for injection moulding machines. Time-saving programming solutions combined with precise milling enable highly efficient production of screw shapes on a MILLTURN. In addition, sophisticated deep hole drilling solutions give our machines a
decisive advantage in comparison with conventional production methods.
The manufacturing of key components for high-tech engineering is in a class of its own – the highest level of productivity for roughing and finishing without grinding whilst maintaining the narrowest of tolerances, together with integrated workpiece measurement are among the requirements. Alongside technological factors, process-safe manufacturing and a high level of flexibility of the machine design also play a very important role. Our MILLTURNs master these challenges with ease. At WFL our ambition is to take away as much complexity as possible and to guide the customers in a step-by-step approach. In the daily business we get to solve some of the most challenging manufacturing tasks and the projects very often involve a number of digital solutions as well as automation. Our offer is highly flexible and based on very comprehensive internal solutions.
Could you throw some light on your global presence and networking?
In the global distribution market, WFL makes every effort to attract the best possible representatives, sales staff, service and technology experts. Collaborations with research centers such as the AMRC - a leading research institute focusing on aviation - and specialists in the fields of software and technology expand know-how as well as product portfolio.
Regarding research, we count on excellent partners and intense cooperation. The Oregon Manufacturing Innovation Center – or OMIC– is one of these partners. Oregon’s research centre unites manufacturers and universities within one innovation environment. The centre’s objective is to solve real problems for experienced manufacturers by means of applied research in a timely manner.
The Research Centre enables the development and use of new innovative tools, techniques and unique technologies. We support this valuable partnership with a MILLTURN.The machine is mainly and successfully used for research and training purposes. It masters the most challenging manufacturing tasks due to its sustainability and robustness. Thanks to this successful cooperation, we are able to optimize applied technologies in metal processing together with their customers.
What are the tailor-made solutions you offer both in terms of equipment and software?
WFL customers enjoy tailor-made solutions. Our aim is to evolve from a solution provider into a system provider. Complete machining is subject to different demands today, or more accurately put, greater demands. Which is why we are always on the ball, striving to integrate a wide range of technologies, measuring tasks, finish machining operations, gear teeth and much more into our MILLTURN complete machining centres, all to suit our customer‘s needs. Right from the very start, our motto has been “clamp once – machine complete“. That is and remains our goal.
Machining operations are increasing in complexity, so we are acting accordingly and ramping up our technological processes. However, we focus on more than just the machining operation itself; we cover the entire process. And by this we mean defining the machining process, workpiece programming, simulation, production and finally, support throughout the entire service life of a machine. We want to play our part in maximizing productivity.
You seem to champion in the area of manufacturing components of complex geometry. Could you throw some light on your capabilities?
The manufacture of engine modules and complete drives requires working with difficult-to-machine materials such as titanium, Inconel and powder steels. The manufacture of blisks (blade integrated disk) is a key discipline in machining. When it comes to complex workflows and high-quality requirements,wellknown manufacturers are opting for a MILLTURN owing to the extremely precise machining by means of the B-axis, as well as reliability and costeffectiveness.
But not only the technical possibilities are crucial, the right software solutions are also an essential element in the machining process. The patented CrashGuard collision prevention system is a real-time software expansion for the CNC control, which prevents collisions between machine components in automatic or manual mode using a 3D model of the machine. We have created a unique customer benefit with CrashGuard: additional protection against high repair costs and a reduction in downtimes and production losses.
Without any doubt, the pace in optimizing manufacturing through digital support and automation has significantly increased and developments towards that will accelerate in the future. Within manufacturing there are several key targets to meet in order to stay competitive and generate profitable business results in a challenging environment.
When it comes to technology, we provide a wide range of expertise, especially in internal machining and feed out tools: deep drilling, boring, bottle boring and facing heads. All the benefits of complete machining for this type of work are being exploited, setting new standards in terms of value for the money and precision.
Please give a brief account of your infrastructure, wherewithal and manufacturing excellence.
Today, WFL is a global technology leader and the only company focusing on complete machining with a full range of MILLTURN machines. The possibilities for machining complex parts up to very big components are endless and more than twenty different machining methods can be performed.
The machines are built in modules and there is a very flexible choice for customers to design the machines to their specific needs. WFL works in close cooperation with their customers and together the most difficult machining tasks are being solved. A tremendous journey has been made in 25 years and today WFL is one of the most respected machine tool companies on the market. The product itself and the advanced software solutions together with the expertise in manufacturing is highly appreciated.
Why should one opt for your retrofit solutions?
A MILLTURN from WFL is always a product for the highest quality demands. Even in the case of used machines, we ensure that our systems are in top condition before they are delivered to the customer. Depending on the customer’s needs, we offer a complete concept with consultation, technology support, commissioning & training for used machinery. A Premium Pre-Owned MILLTURN can prove to be an attractive alternative, especially when additional capacities are needed at short notice or the budget will not stretch to cover a new machine.
The greater focus on second-hand machines in the last two years clearly shows that there is a great deal of interest on the market. We always keep a number of high-quality used machines in stock, with the majority being sold to global corporations in Germany, Sweden or the USA. These machines have already been running perfectly for several years since their retrofit. So why should a customer buy a used machine? Cost efficiency and fast availability are clear arguments in favour of a second-hand solution. If we have a suitable machine in stock, it can usually be delivered within three months.
How do you envisage the growth prospects of the machine tool industry and what are your strategies to make the most of the opportunities available in India?
From our perspective, the machine concept of the future is complete machining – with ongoing optimisation, additional processes, greater information processing and integration in higherlevel systems. There is a rapidly growing market for complete machining. Our customers come to us for solutions that don‘t exist yet. Some of the requirements include automation of a MILLTURN with heavy workpieces and production of a wide range of gear teeth. We are always able to find a solution for these requirements. New technology, products and machines are being developed and adapted to meet the needs of the future. WFL will increasingly evolve into a system partner. Good examples of this include the acquisition of automation expert FRAI Robotic Solutions in 2018 and the introduction of our own system tools for the most challenging production tasks. The new organisation that we are currently developing enables us to give our customers more comprehensive and sustainable support, throughout the entire life cycle of a MILLTURN.
India is a very important market for WFL. Therefore, measures have been taken in the past few years to strengthen our sales and service activities.Service and spare parts are available in India and can therefore be quickly available at the customer’s site. We have been working with an experienced service partner for years. The sales activities have been intensified in the last two years and another “WFL Regional Sales Manager” has been employed.
How far have you come, embracing digitization and Industry 4.0 solutions?
With our development as a total solution provider, we are in a position to provide our customers with comprehensive and sustainable support over the entire life cycle of a MILLTURN. We can also offer many great solutions around the topic of Industry 4.0 or digitization: starting with the updated version of CrashGuard Studio, the completely new process monitoring WFL iControl and further developments in sensor technology in tools and the MILLTURN, we prove strong progress.
The new process control software iControl protects the MILLTURN, even during autonomous production throughout the night. Depending on the machine‘s equipment, up to 16 freely configurable process signals are continuously monitored. The new design contains more complex and more intelligent monitoring options, offering comprehensive safety during production. Multi-stage monitoring logics are used, which respond, if the collision limit or adaptive process limit is exceeded, or if there are significant, rapid changes in force.
What’s the way forward for WFL and how do you look at the future?
WFL has a clear aim – to grow faster than the market. We intend to do this with outstanding products from machines to software and from production solutions to customer services. We want to have a stronger presence in the markets, establish additional branches and look after national regions. We want to use the latest technology, not just in its machines but also in its processes and service support. The expansion of the sales and service network (with 24/7) in the markets is a key strategic goal.
Article MACHINE TOOLS WORLD (February 2021) - www.mtwmag.com