"Turning is my life"
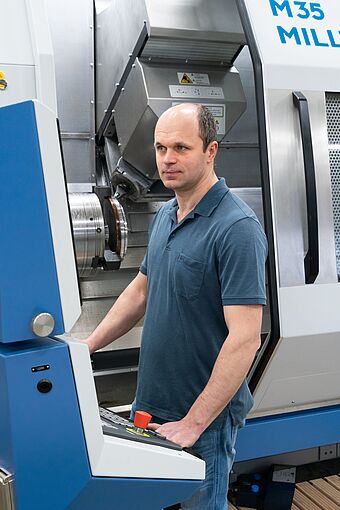
The story of a small company in Bavaria is a perfect example of how to turn a hobby into a successful business. As a machining expert for special alloys, Waldemar Maul – together with his wife Anna – has already firmly established himself in Germany through his company "Edelstahl WM GmbH". Whether duplex, super duplex or V4A steels, higher alloyed materials are produced here with remarkable precision and quality.
Wiesenfelden is a tranquil municipality in Bavaria and the home of Edelstahl WM GmbH's new production hall, which was built at the beginning of 2020. The range of equipment means a multitude of processes can be covered, from turning, milling, welding and grinding right through to measuring. The new M35 MILLTURN will strengthen the company's focus on complex parts and help them win further orders.
Turning in the garage
It all started in May 2011. As a change from his office job, Waldemar Maul acquired a turning machine and started making turned parts in his own garage in Kelheim. Soon afterwards Waldemar became a sole trader as a second occupation. His first customers came from his full-time job at the time as an industrial foreman specialising in metals and were founded on his initial training as an industrial mechanic specialising in industrial engineering. Some of the turning and milling work was outsourced by the customer. This enabled him to support customers in this area with the manufacturing of high-quality products made of stainless steel.
The foundation established in 2012 led to increased sales in 2013 and 2014. "We were able to impress our customers very quickly with our high-quality work and by always meeting deadlines. This enabled us to establish strong customer relationships," reports Anna Maul. One year later, the company finally changed its legal form from a sole trader to a limited liability company.
The year 2015 was a very significant one for Edelstahl WM GmbH. Where previously orders had been processed on private premises, where space was very limited, in December 2014 a production hall was rented in Kelheim. In February 2015, the big move from the Maul's private garage to the large production workshop took place. The managing director also decided to give up his main job and devote himself entirely to Edelstahl WM GmbH.
Over the following years the workshop was equipped with more machines as well as special tools. In September 2016, the first turning-milling centre with a turning length of 1500 mm was purchased. The main reason behind the investment was to increase the quality and accuracy of the manufactured parts. "We were then able to meet customer requirements to a greater extent as well as to expand the order volume due to the broader production spectrum for turning and milling. Setting up an inspection room allowed us to further increase the accuracy of the manufactured parts," says managing director Waldemar Maul.
Edelstahl WM GmbH moved into the newly built production hall at the end of April 2020. The site in Wiesenfelden became its new home, where the managing director is responsible for the entire technical operation, including production. Another employee provides him with support. There are plans to train a cutting machine operator in 2021. Anna Maul is responsible for the commercial aspects of the business, including order processing, financial accounting and human resources.
Practice is key
Edelstahl WM GmbH has specialised in the production of individual and prototype parts through to small series runs from the very beginning, using high-quality, select materials. "The parts we produce are characterised by exceedingly high quality and 100% precision. We also support our customers with internal problem solving. This could include product or project-related suggestions for solutions and improvements, for example" says Waldemar Maul.
"Our customers operate in a wide range of markets, with the majority coming from the chemical, mechanical engineering and medical technology sectors," explains Anna Maul. Ninety-five percent of them are direct customers who assemble the systems themselves and are located in Bavaria and Baden-Württemberg. Since 2011, the company has been producing workpieces made of special alloys such as V4A grades, duplex, super duplex, etc. "That's why we also opted for the WFL machine. I was looking for a powerful and robust machine on which I could process these materials," explains Waldemar Maul.
When asked how he came to specialise in highly complex parts, the managing director says: "You learn a lot about materials when training to become a welding specialist, such as how and where to use materials and process them correctly. Often the wrong materials are chosen for certain environmental conditions and then everything rusts within a very short time. Thanks to my professional experience in a gearbox and pump factory, I also know what is important when installing and removing such parts. What's more, every time I come across challenging manufacturing tasks, it always spurs me on. That's why we've established a focus on complex components."
Navigating the crisis with strategic skill
The worldwide coronavirus crisis has had little effect on Edelstahl WM GmbH. Although a number of orders from the automotive sector were cancelled, by contrast volumes increased from the medical technology sector. The machines are very well utilised.
"Often we have orders involving special alloys – these are predestined for the MILLTURN," says Waldemar Maul enthusiastically. "My goal on this machine is to minimise the number of clamping operations so I can do multiple machining steps. This enables us to achieve higher quality as well as narrower component tolerances."
Due to the extensive equipment in the production hall, blanks can be cut to size in Edelstahl WM GmbH's own facility. The parts are then rough-turned or rough-milled and finally welded. Only the pickling of chromium-nickel steels is outsourced. After machining the parts by turning, milling and (flat) grinding, the workpieces are measured in the inspection room.
Order volumes of 100-300 pieces are typical, with parts being delivered in batches of 10 or 20. "Usually this ranges from one to ten on average. That is the usual batch size," says Anna Maul. Hardly any mass production takes place at Edelstahl WM GmbH; usually individual parts are manufactured.
The strategy of Edelstahl WM GmbH has proven to be successful so far. The specialisation in small batch sizes and individual parts as well as the complexity and accuracy of the components will be further expanded by the investment in the MILLTURN.
Every part must be a good part
At the moment the team is busily testing and programming the M35 MILLTURN. A SolidCAM solution with a 5-axis program was purchased to assist with the programming. "For some orders, we could have done with having the machine sooner. The decisive factor in our decision to purchase the MILLTURN was investing in a machine that would improve our current production processes and take us forward strategically," says Waldemar Maul.
At Edelstahl WM GmbH, the components are largely manufactured by the managing director himself. However, the goal is to hire staff or train machining technicians from scratch. Due to the special orders and complex workpieces, it is often difficult to find suitable personnel. "We want to train employees to the point where they can do the work on their own. Unfortunately, applicants are often put off by the complexity of the components and the required precision," explains Anna Maul.
"Our philosophy here matches that of WFL: every part must be a good part," says Waldemar Maul unequivocally. "Our parts are incredibly demanding, which is why I have very high expectations of an employee."
Experience and specialist knowledge as a guarantee for success
Waldemar Maul knows what is important in his business. As a foreman in a gear and pump workshop, he himself disassembled, overhauled and reassembled pumps and gearboxes. This is of particular benefit to him in his work today. "If I can see the drawings and know where it's going to be installed, I'm already at a distinct advantage."
Customer loyalty confirms this without a doubt. Precise, high-quality work and support when manufacturing parts are of the utmost importance to Edelstahl WM GmbH. "We want to understand exactly what the customer does in order to deliver the quality they need; we are in constant communication. We come up with suggestions for improvement and develop solutions together," adds Anna Maul. "Trust is very important for long-term customer relationships. We have very good partnerships in this respect."