WFL Millturn Technologies GmbH & Co.KG - The technological leader.
WFL is the only manufacturer worldwide that focuses exclusively on the production of multifunctional turning-boring-milling centers ... more
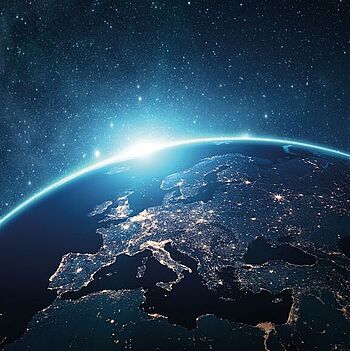
Global contact partner:
Technologies
Combining all machining and measuring operations in one single MILLTURN by WFL will raise the efficiency of your production enormously. This is an investment that pays off in virtually no time.
machining result
News
WFL Screw programming
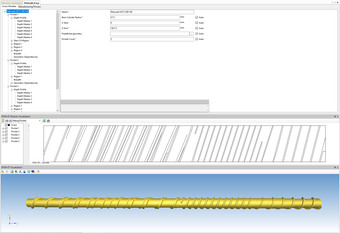
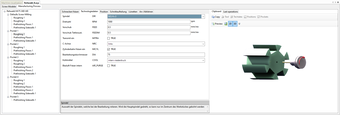
The proprietary simulation and programming software CrashGuard Studio enables users to perform preliminary verification of NC programs on the PC and carry out easy workshop-comparable programming using the programming editor MillturnPRO. The functionality has been significantly enhanced with the option to easily program screw geometries.
Geometries like these are needed for screws for machinery for plastics such as extruders or injection moulding machines, where solid granulates are pressed through one or more rotating plasticising screws in a cylinder. A heating system, friction and pressure cause these granulates to melt during the conveyor process through the screw, at which point they can be processed further. During the melting process, the feed or removal of materials or gases can influence the properties of the end product. This process produces high pressures and forces, not to mention wear due to friction and high temperatures. Suitably resistant materials are
therefore needed, which poses a major challenge during machining. Because of these requirements, the manufacture of cylinders and screws is an ideal area of application for the MILLTURN from WFL.
Demands on the production of screws
Modern screw geometries with the associated compound and shearing parts can only be manufactured by means of complex milling operations; the machining process and programming needed are extremely demanding.
In many applications, the inclined walls can be produced using standard tools, e.g. solid carbide end mills with corner rounding, instead of expensive special milling cutters. This is facilitated by an automatic „best-fit“ calculation algorithm together with the B- and Y-axis.
The entire range of requirements are perfectly covered with the capabilities of the MILLTURN from WFL. As well as wanting to be able to program screws in an easy and flexible manner, very specific clamping devices are also required. WFL has responded to these requirements and now offers a range of new solutions.
Screws are often produced in a customised manner and therefore in very small batches in line with demand. In many cases, especially when manufacturing spare parts, only 2D drawings are available. The new software solution from WFL is designed for such demands and offers particularly simple, quick and flexible programming with direct simulation options and collision checks. Even prototypes can be efficiently and reliably programmed and produced.
Key features of the new WFL screw programming software
Advantages
The WFL screw programming software, which is integrated into the 3D simulation software of CrashGuard Studio, gives the customer the option to use different geometrical and technological functionalities.
During the modelling phase, the software uses the parameters which have been entered, such as diameters, pitches, wall inclines, radii, bar or channel widths, etc, to interactively create a 2D model representation of the cylinder development of the boundary contours and a 3D model of the screw.
The following geometries can be produced:
- Single or multi-flighted screws, including changes to the number of flights
- Changeable depth
- Any change in pitch
- Wall shaping with radius to the channel base and wall inclination angle in the longitudinal cut or in the channel crosssection
The NC programme is then generated based on the target geometry of the screw. For this, the appropriate tools must be defined for the different machining areas and the technology parameters such as cutting speeds, feed depths, feeds, etc. must be determined.
With regard to the technological implementation on the workpiece, the following machining processes are used:
- Rough machining with automatic cut distribution and Y-offset control (turn-milling)
- Finishing of walls with automatic „best-fit“ tool positioning (B- and Y-axis)
- Finishing of channel base
- Chamfering of barrier bars
Before machining the actual workpiece on the MILLTURN, there is a comprehensive 3D simulation in CrashGuard Studio. The machining time is already evident at this point.
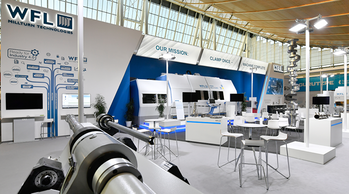
Worldwide
WFL locations
More than
Excited employees
More than
Registered patents
WFL software, service & support
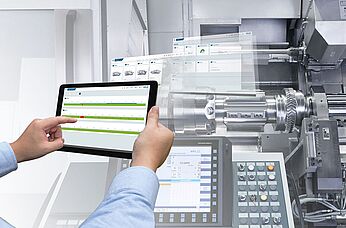
CrashGuard, the patented collision prevention system is a real-time software extension of the CNC control system.
MORE
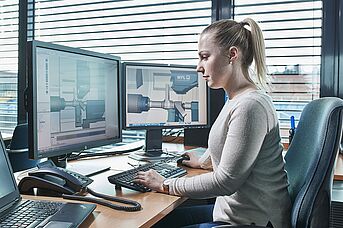
CrashGuard Studio, the realistic 3D simulation software is the ideal tool for testing and optimising CNC programs after they have been created or modified.
mORE
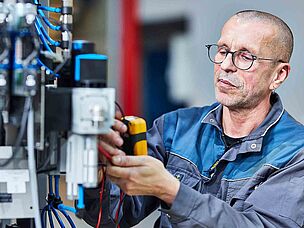
We are close to our customers. Major manufacturers put their trust in WFL’s vast experience. A head start that reflects in WFLs services. Please find here our offers.
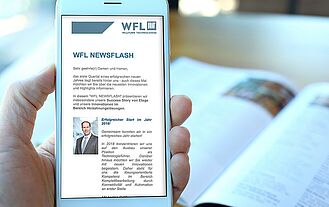
WFL NEWSFLASH
Register now!
The WFL NEWSFLASH informs you about our latest innovations in complete machining, technological highlights and modern services as well as upcoming events and exhibitions.
Register now and do not miss out on any WFL news!
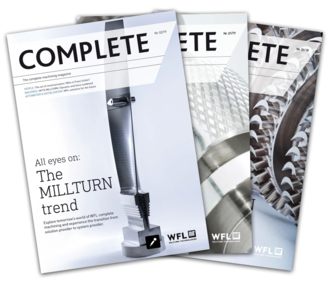
COMPLETE
The complete machining magazine
Explore tomorrow's world of complete machining. Be inspired by innovative technologies, success stories and product highlights.
Dive into the world of WFLs' complete machining.